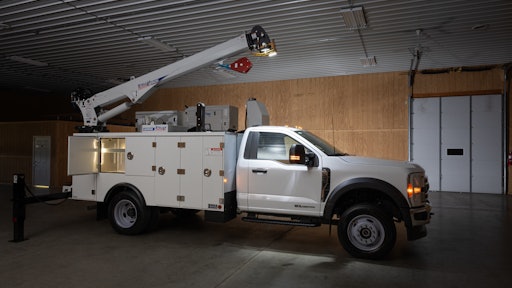
Considerations such as the nature of the job, the environment it will be working in, driver and CDL requirements, and weight regulations will help operators in deciding the components of a mechanic truck.Stellar Industries
One primary advantage of mechanic trucks is their ability to be configured to meet the unique needs of different industries. From construction sites to oil fields, these trucks offer a level of onsite support that can significantly impact a contractor’s bottom line.
This article delves into some of the options available when building a mechanic truck, offering a quick guide to help contractors make informed decisions that align with the needs. Specifically, it will examine the crane, chassis, body, storage and equipment options for mechanic trucks.
Where to Begin: Understanding the Job & Regulations
Building the right mechanic truck starts with a thorough understanding of the job it’s intended for. Considerations such as the nature of the job, the environment it will be working in, driver and commercial driver’s license (CDL) requirements, and weight regulations will help contractors decide the components of a mechanic truck. The crane, chassis and body are all related, and the build can start with any of those elements depending on which of the three is most important to the daily tasks the team wants to accomplish with the mechanic truck.
Starting with the Crane
Knowing how often the crane will be lifting, what will be lifted, how much weight needs to be lifted and how much reach is required will help operators select the type, length and capacity of the crane.Stellar Industries
Starting with the Chassis
One key aspect to keep in mind is the gross vehicle weight rating of the chassis. This is an aspect that determines driver CDL requirements, and it influences the payload available. Understanding the specific regulations applicable to the contractor and where the truck will be operating is important. Whether the chassis is gas or diesel and the transmission type impact how the equipment on the truck is powered.
Starting with the Body
The options related to the body include the length, the height of compartments, the body material, bumper options, stabilizers and load bed covers. The length of the body and height of compartments determine storage space for tools and parts. Depending on the environment the truck will be operating in and the payload needs, teams want to carefully consider the material the body is made of.
Material Considerations: Aluminum Versus Steel
Depending on the environment that the truck will be operating in and the payload needs, teams should carefully consider the material that the body is made of. Historically, mechanic trucks have been made from steel, because of its durability. Although steel is a valid option for some, aluminum has become increasingly popular.
Factors driving that popularity are:
- Lighter weight: Aluminum enables a significantly lighter body, compared to steel, increasing payload capacity.
- Enhanced corrosion resistance: Aluminum mechanic trucks offer the corrosion resistance needed for long-term service, crucial in areas with high humidity or heavy snow.
- Drill-free mounting rails: Some aluminum bodies use an extrusion with built-in mounting rails for accessories on top of the truck body. This makes it easy to add and move components while avoiding drilling holes.
Crane Considerations: Maximizing Mechanic Truck Capabilities
When it comes to telescopic service crane options for mechanic trucks, three main categories are available: electric, electric-hydraulic and hydraulic cranes.Stellar Industries
When it comes to telescopic service crane options for mechanic trucks, three main categories are available: electric, electric-hydraulic and hydraulic cranes.
The Case for Electric Cranes
Electric cranes offer the advantage of not needing a power take off (PTO) and pump installed on the chassis to run hydraulics. The electronic cranes operate with an electric winch and an electric pump to run the self-contained hydraulics on the crane, making them a cost-effective option when a smaller crane with a lower duty cycle is required. These cranes typically operate at one set speed.
The Case for Electric-Hydraulic Cranes
Electric-hydraulic cranes, like electric cranes, don’t require a PTO and pump on the chassis. The difference is that electric-hydraulic cranes will use the electric pump to operate a hydraulic winch and other crane functions. These cranes typically can offer proportional control of the cranes, giving the operator more precise control over the speed at which the crane operates.
The Case for Hydraulic Cranes
Hydraulic cranes offer robust performance, providing a versatile solution with increased lifting capacities and duty cycles. These cranes are typically proportionally controlled, and their remotes usually have more features. These cranes are often favored for heavy-duty applications in which maximum lifting capacity is crucial.
Equipment Considerations: Toolbox Systems, Air Compressors, Lube Skids & Power Units
The toolbox systems in mechanic trucks often feature drawers that are rated up to 500 pounds per drawer to ensure long-term durability.Stellar Industries
Keeping in mind what side of the truck the team will be working on and how tools and parts should be stored is important. A well-organized toolbox system, parts bins and shelves serve as the cornerstone of efficiency, ensuring that every tool has its designated place to streamline workflow and minimize time spent searching for equipment.
Specific considerations such as size, material and handle options should be considered to enhance the functionality and accessibility of the toolbox system. The toolbox systems in mechanic trucks often feature drawers that are rated up to 500 pounds per drawer to ensure long-term durability. Like the body, some manufacturers offer heavy-duty aluminum drawer sets in addition to steel.
Air compressors provide the power needed to operate pneumatic tools, clean debris and offer inflation. Air compressors can be hydraulically driven if the chassis has a PTO and pump or driven by a small horsepower engine. Compressors can use rotary screws or pistons to compress the air. Knowing the volume of air and pressure needed and the duty cycle needed will help contractors select an air compressor.
Permanent-mounted and mobile lube skids are becoming a more popular addition to a mechanic truck because they enhance the overall efficiency of the maintenance and repair operations. They provide a centralized, convenient solution for dispensing and storing new oil, waste oil, grease and other lubricants. With lube equipment, a mechanic truck becomes a mobile hub for maintaining equipment.
Auxiliary power units are an alternative to a PTO and pump to power equipment. These self-contained units can power hydraulic systems, electric tools and even offer welding capabilities. They are driven by a small horsepower engine but some run on their battery power.Permanent-mounted and mobile lube skids are becoming a more popular addition to a mechanic truck because they enhance the overall efficiency of the maintenance and repair operations.Stellar Industries
Crafting Efficiency & Durability
Building a mechanic truck requires thoughtful consideration of several factors and how all the components relate to each other. A lot of decisions must be made to craft the ultimate mechanic truck. This guide will help contractors navigate common options available, ensuring that their investment aligns with the demands of the job and stands the test of time.
For more personalized guidance and assistance in making informed choices, contractors should partner with a manufacturer or one of their distributors. Their expertise can ensure that the truck is tailored to each contractor’s needs and built to the highest quality standards.