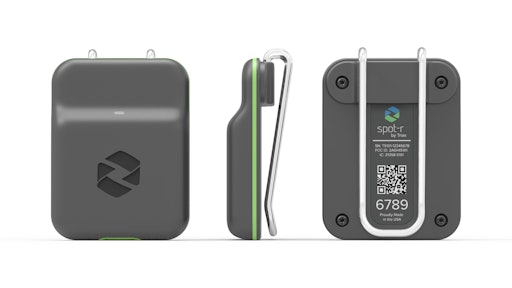
While wearables that robotically augment the physical capabilities of workers—like SuitX by Ottobox or the SenSuit by Sarcos Technology and Robotics are fascinating, more humble wearable devices that increase operational efficiency and safety are easier to find on jobsites.
Most of these devices are not stand-alone—they are components in a solution that includes cloud software. Some wearables though are not part of a proprietary system, and can increase the usability of native construction applications and augment that small form factor with capabilities like push-to-talk, integrated cameras and geolocation.
Android Construction Wearables
Manufacturers of Android and iOS devices offer wearable devices that enable construction personnel on site to communicate and interact with software hands-free.
“The purpose of wearables is to make it easy to use both hands, and get freedom,” Zebra Technologies Global Product Marketing Senior Manager Adriana Patino said. “All will be worn on the wrist, arm, back of the hand or the fingers.”
Zebra’s offering in the space encompasses Android-based devices including wrist-mounted computers just smaller than a smartphone to smaller devices with a two-inch screen.
“Our wearables are Android based—and certain partners have been vetted and validated when they have created specifically for the two-inch display,” Patino said. “Our other devices do not require that degree of development, and customers get the easiness of having Android running, which helps them put on their own application.”
The Zebra WT6300 for instance offers an optional keyboard and a dust-proof, water-resistant package featuring a glove-friendly Gorilla Glass touchscreen and a battery rated for -22° to 122° F.
The more compact WT6300 and the smaller WS50 Android Wearable Computer are available in configurations that can include a camera, a scanner and push to talk over Zebra’s Workcloud Communication, formerly Workforce Connect.
“The WS50 is smaller and has less memory,” Patino said. “It is a simpler version that allows push-to-talk to communicate to groups rather than one-to-one or one-to-many like on the WT6300. It does have geolocation and features including a danger button and an accelerometer to sense a fall.”
Competing products in this space include those from Honeywell, like the Honeywell CW45 or the Effon WT04. One wearable option that is head-worn is the RealWear Navigator Z1, a light yet rugged hands-free intrinsically safe industrial wearable solution for productivity and safety for use in highly restricted zones. The Z1 may be most analogous to Zebra’s HD4000 Enterprise Head-Mounted Display.
Zebra HD4000.Zebra
Construction Wearables Coordinate People and Equipment
While wearable devices are by definition people-centric, construction wearables vendor Triax Technologies goes beyond people to integrate data from the industrial internet of things (IIoT) with data from sensors worn by workers. This helps contractors identify constraints to labor productivity, track equipment utilization and expedite emergency response.
“We focus on a few things—safety, equipment utilization and labor productivity,” CMO and Vice President Maggie Williams Dryden said. “It is equipment to make sure you are utilizing what you are paying for. From a human capital perspective, are you budgeting correctly and paying for labor you are actually using? How much productive time do you have in every day?”
Dryden said that in construction, Triax has focused on engineer, procure construct (EPC) contractors.
“We most certainly do commercial construction as well,” Dryden said. “But in EPC, we can leverage all four of the core value propositions we talk about. We find contractors in process plant construction, oil refineries, downstream oil and gas, anywhere there are large groups of workers and specifically those that are temporary in nature coming onto a large site to do a turnaround, build a new piece of equipment, capital investment projects … anything where there are large numbers of people who may not be on that site frequently, that is where they really see value in a solution like ours.”
For commercial projects, Triax may according to Triax Vice President of Product Anthony Butler be a fit for projects worth more than $50 million.
“It is usually a larger project with hundreds of workers, sometimes thousands of workers, on a site simultaneously, or constantly changing groups of subcontractors due to complexity,” Butler said. “Our customers look to us to help provide clarity of who is on their site, where they are at and how they can get more productivity out of them.”
Why Not Just a Smartphone?
The Triax wearables outperform consumer mobile devices some contractors may use to geolocate workers on site in the areas of privacy protection, resistance to environmental insults, battery life and robustness of communications options.
“I know with my smartphone, I have a hard time getting through the day without a charge, and I am definitely not getting beyond two days,” Butler said. “Our typical devices' batteries last for months. And depending on your particular needs, we can customize something for you and give you devices that will last a year for an individual worker. Another consideration is that we have both a pressure sensor and accelerometer on this device, and we use that to detect worker falls. If a worker falls more than 10 feet, we will pick that up. We also have increased capability for tracking location at height. Your cell phone will do a good job if it can access those satellites determining your location, but it is not good at elevation. We also, with our network, have the ability to work in areas where you have a lot of connectivity issues—some of these sites have a lot of obstructions and are almost the equivalent of Faraday cages where you have a ton of metal, wood or concrete and the vantage point is constantly changing.”
Triax augments its wearables for employees with simple sensors added to equipment, often with magnetic mounts, rather than relying on OEM telematics units.
“What we have found working with customers is that not all of the equipment will have suitable telematics units, and in not all cases will it work,” Butler said. “And often our customers will have subcontractors bringing in their own vehicles, some from United Rentals, some from Sunbelt—we just found it works much better.”
Triax equipment sensors can track location as well as hours of operation through vibration and pressure sensors. Data from wearables augments this data for time-on-tool tracking.
Wearables and equipment sensors communicate on the site through a proprietary protocol similar to a mesh network over a hub and spoke network installed on site connected to local site internet, Wi-Fi, direct ethernet connections or gateways. In some cases, Butler said Triax was using LoRa—Low Power, Long Range transmission.
Eyrus's Zone Dashboard displays the location of workers along with a count for each zone.Eyrus
Eyrus Construction Wearables for Workforce Management
To drive data into its workforce management software, Eyrus meanwhile offers multiple options ranging from cell phones to wearables like beacons and badges.
“Phones do not have their place on every worksite,” Eyrus CEO Alexandra McManus said. “You can have very simple ID cards that you use to tap in and tap out.”
A number of variables determine whether Eyrus customers rely on wearables, including cost, with cell phones or tappable IoT badges being lower cost options.
“The more obstruction-free, effortless options include IoT with BLE badge put on a helmet,” McManus said. “We can have readers across the site and seamlessly and auto-collect when somebody came on site and where they went. You can also add NFC (near field communication) badges to control turnstiles and doors or other physical barriers, while using scanners in open areas that can read that device.”
By combining NFC and BLE devices, a contractor management team gets more complete visibility.
“Supervisors, or safety managers, if somebody has on NFC and BLE, can see who individuals are, whether they are certified to be in that area, and can get all that data if 10 or 50 people are standing in a room,” McManus said. “
This combination of NFC and BLE can also be augmented with video to enable management to check for personal protective equipment and forensic incident recreation. This combination of technologies may work better for some use cases like capturing fall incidents than accelerometers, according to McManus.
“I’m not a big fan of using accelerometers to tell you somebody fell,” McManus said. “They are not that sensitive … for falls, there is lots of technology used on site that does not give you good data because of the massive amount of false positives.”
Leica Wearables and Telematics for Safety Around Equipment
Leica, meanwhile, offers an integrated safety system consisting of its PA10 collision warning system, which uses a wearable tag that sends workers visual, auditory and vibration warnings when they enter a risk zone around machines. The PA10 panel inside of the cab can be configured with three alert distances around machines or moving vehicles delivering these visual and vibratory warnings to both the pedestrian and the machine operator to prevent accidents.
Leica takes this arrangement one step further with the PA80 product, which extends the PA10 with the MC1 machine control system. Thanks to an Xwatch integration with the machine CAN bus, the PA80 can slow or stop a piece of equipment to prevent an accident.
“As it stands, we have done an integration with Xwatch Safety Solutions for excavators,” Leica Product Manager Brad Mullis said. “What this does is give us a proportional ramp down of the machine's hydraulics based on tag proximity. We do not currently support or integrate with any other proximity detection devices. That said, Leica is very open to the possibility and has had early engagement with other providers.”
The PA80 and PA10 systems are competitors to pedestrian detection systems based on machine vision, like the Blaxtair. On the Blaxtair, a stereo camera can determine location and direction of a moving pedestrian, alerting the operator. An Xwatch integration, similar to the one leveraged by Leica, can slow and stop the machine to prevent collisions.
“Both are compelling technologies which aid a safer working environment,” Mullis said. “The key for Leica wearables is that the personnel are warned of the zone they are in through the device. The wearable also gives the ground personnel a means of communication with the operator through a panic alert. It allows the ground personal the opportunity to make decisions and not only the machine operator.”
The Leica wearables-based solution also means that in “unfavorable conditions that include but are not limited to, rain, mist, snow, fog, vegetation or deep excavations the operator, will still be alerted to the presence of the wearable,” Mullis said. “Vision systems require the camera to ‘see.’ If it cannot see, it cannot alert.”
Leica is not the only vendor pursuing this combination of technologies for site safety--Caterpillar extends its Cat MineStar Detect system with the multiple people-based technologies including the HC1 Hardhat, the TA1 wearable tag or a dedicated smartphone app for Android devices.