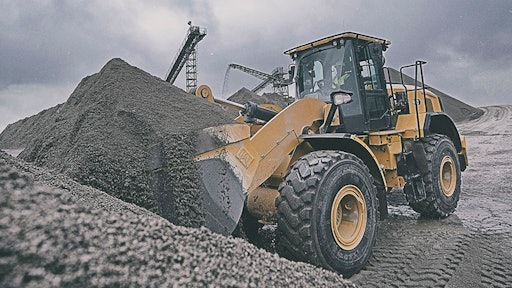
Tire selection matters — affecting the performance, stability, ride quality and efficiency of your wheel loader. The right tires can help improve cycle times and lower fuel consumption. The wrong tires can hamper productivity and drive up costs. For most loader applications, it comes down to a choice between radial and bias tires. Which is right for you?
What’s the difference?
The terms “radial” and “bias” describe the pattern of your tire’s plies. Those are the layers that lie beneath the tread — you won’t actually see them unless you wear through the rubber.
Bias tires feature crisscrossed cords of material — usually polyester and nylon — placed at an angle to the tread’s centerline. Radial tires feature a casing made of rubber-coated steel cables that arc from one bead to the other. Rubber-coated steel plies are placed under the tread.
When should I choose radial tires?
Radial tires often make the most sense for loading applications on finished surfaces — where traction, tread wear and distance are key factors. That’s because they tend to have less flex than bias tires and offer better control at higher speeds. The lower rolling resistance of radial tires also makes it easier for operators to turn.
When do bias tires make more sense?
If you work with abrasive materials like gravel or in a pit or quarry where you run the risk of cutting the sidewalls, bias tires may be a better choice. Their thicker sidewalls are more resistant to cutting, and they’re also easier to repair than radial tires — so you can extend life and lower costs. Bias tires also offer a smooth, stable ride to keep operators comfortable.
What’s the cost difference?
Bias tires typically cost less to purchase. Keep total cost of ownership in mind, though. If you put a bias tire to work in an application better served by a radial tire, you might save money up front. But it may cost you more down the road in terms of fuel consumption, tire wear and overall loader productivity.
What about tire pressure?
Tire pressure is just as important to life and performance as tire selection, so always follow the manufacturer’s recommendations.
Operating on underinflated tires can increase fuel consumption, affect loader handling, shorten wear life and ultimately lead to tire failure. And operating on overinflated tires is dangerous, because they’re more likely to be cut or punctured.
A good practice is to check tire pressure at least once a week. Do it when the tires are “cold” — after the loader’s been stopped for three or more hours or operated for less than a mile at moderate speed.
Looking for more tips on choosing the right loader for your job? This selection guide walks through the top considerations, including tires, buckets, attachments, technologies and more.