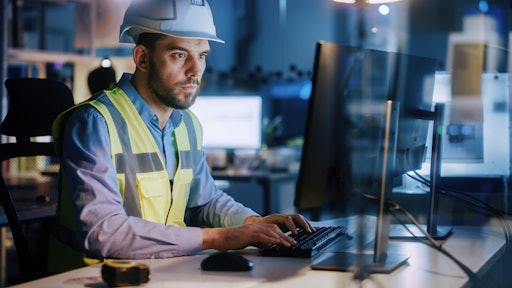
Telematics has become table stakes industrywide—today, everyone expects standard connectivity to all their lift and access equipment.
In the early days of telematics, customers wanted access to all the data from the machine. Then, there was a period when customers said that they were getting too much data and requested less. Today, the pendulum has swung back in the other direction, and users are again wanting more data from the machine, asking for even more than ever before.
To meet this demand, manufacturers need to structure their telematics solutions in a way that is more efficient for contractors to navigate, more meaningful in the way the system provides the data and more effective for them to use the data to proactively manage and maintain their fleets.
3 Challenges
There isn’t one industry over another that benefits more from using telematics. If the application requires the use of equipment that moves, it benefits from telematics.
A trend that has reemerged from this is customers asking for deeper machine insights. Three challenges face the equipment industry today when it comes to data and telematics. They are discussed below.
1. Actionable Data
Historically, customers have been overwhelmed by the amount of data available through telematics, so they asked to receive less. This resulted in too little data being provided. Customers want more data, but they want it in a way that makes the data actionable and digestible.
That means customers need a way to access the data through their telematics systems that allow them to manage the data and prioritize the information they most want to view. This includes:
- Equipment maintenance pages
- Maps that include machine location and geofences
- Reports on many other data points, including diagnostic trouble or fault codes
Having actionable data also means that telematics systems need to be more effective to use. For example, it’s always been a challenge with certain functionalities like geofences, which are great tools but are operationally difficult to develop and maintain.
2. Confusion
Telematics show where and how equipment is operating by providing high-level or finite details on several machine systems.JLG Industries
Trade-offs will always come with this decision because there is no one-size-fits-all answer. The right telematics solution will be the one that meets each business’s unique needs and goals.
3. Connected Jobsites
When considering how telematics can or will be used on jobsites, the decision isn’t all about weighing the pros and cons of a program’s specific benefits. It’s also about the logistics of working on a connected job site. A couple of questions users need to ask are:
- Is there connectivity infrastructure available onsite, such as cellular or WiFi service?
- If infrastructure is available, can work crews have connected devices on sites to access telematics information?
3 Benefits
Because telematics allow users to streamline access to important machine information quickly and effectively through digital channels, three benefits exist and are detailed below.
1. Increased Machine Uptime
Telematics show fleet managers where and how equipment is operating by providing high-level or finite details on several machine systems, including:
- Location to help with service planning and to decrease downtime for field techs
- Diagnostic trouble or fault codes to address machine issues and get them back to work quicker
- Machine hours to help with billing and knowing when to service the machine
- Battery status
- Machine use
- Setting geofences/time fences to protect the equipment investment and to be notified on machine use (leaving a particular area or being used before/after a designated time)
- Schedule maintenance tasks
Access to this type of information allows users to manage machine usage more efficiently and effectively.
2. Enhanced Productivity & Machine Performance
Many telematics solutions also have tools to analyze fleet and operator data and determine the overall effectiveness of a machine in a particular situation. Sharing usage and operator data can significantly improve onsite efficiencies. By using telematics in conjunction with other digital tools, such as building information models, contractors can streamline the planning phase of projects to select the right machine for the job.
3. Decreased Downtime
Telematics can also help manage the servicing and maintenance of machines. For example, analyzers to remotely diagnose machine issues and coordinate the tools and parts needed for onsite repairs.
Telematics solutions can also provide users with the opportunity to receive automated reports and immediate notifications when issues arise. In addition, fleet managers can use telematics programs to proactively schedule maintenance, reducing unnecessary service calls and equipment failure.
Telematics can also help equipment owners and users plan for site visits and rental services, such as equipment deliveries.
Telematics Is Changing Jobsites
When setting up telematics, ensure that connectivity infrastructure is available onsite. If it is, can work crews have connected devices on sites to access telematics information?JLG Industries
During the next decade, telematics will continue to evolve to include even more machine information on electrified products, more finite details from the equipment’s integrated sensors, live/real-time video feed footage, in-the-moment servicing of machines, additional semi-autonomous functionality and much more.
Yesterday’s telematics could only do so much. The next generation of telematics is an Internet of Things platform, offering true, two-way fleet connectivity and machine interactivity.