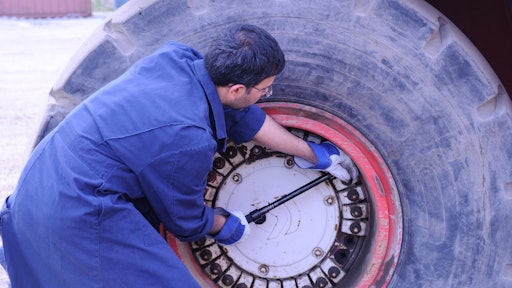
The torque wrench is one of the most important tools for equipment maintenance and reliability when securing critical parts to exact tolerances with zero margin for error. Choosing a reliable torque wrench will help users perform basic fastening jobs. It will also provide the peace of mind that everything was carried out according to the required specifications.
What Is a Torque Wrench?
A torque wrench is a precision instrument used to apply an exact amount of torque to a fastener. Once the desired torque value has been achieved, the operator is notified through a visual and/or audible alert, preventing under- or over-torquing.
Choosing the appropriate torque wrench for the user’s specific needs requires a good understanding of the options available, usage requirements, proper maintenance and recalibration.
Preset Versus Adjustable Torque Wrenches
If a user is working on an application that requires torquing to a specific value that remains constant, then a preset torque wrench is a good choice. Preset torque wrenches are factory-calibrated to a specific value. Once this value has been reached, it becomes impossible to apply additional torque.
Preset torque wrenches are used to prevent operator adjustment of the torque settings. If a project requires a change in the torque value, the manufacturer can reset the wrenches to the new value. As a result, preset torque wrenches are ideal in assembly line environments or applications in which the wrench will only be used in a single, repeated application.
On the other hand, adjustable torque wrenches offer the operator flexibility in setting the desired torque value according to each application. These torque wrenches feature a scale, usually expressed in imperial and metric values, and they allow for the selection of the desired torque value within a lower and upper limit in specific increments.
Torque Wrench Styles
Click-type torque wrenches are the most used kind.Gray Tools
Available torque values are displayed on a dual scale (metric, expressed in Newton-meters, and imperial, expressed in foot-pound or inch-pound) on the barrel of the tool. Torque wrench capacity is indicated by the minimum and maximum value on the scale. The operator sets the desired torque value by unlocking the wrench and twisting the handle, which moves a precision indicator along the scale.
Just like a ratchet, the head of click-type torque wrenches houses the gear and paw mechanism. The repetitive force applied to its mechanism leads to the need for regular maintenance and recalibration.
Dial-type torque wrenches are considered the most accurate available. These wrenches feature a double-end square drive that can be used for tightening and loosening fasteners. The torque value is displayed on an easy-to-read, analog, dual-scale dial (hence their name). Two memory needles are inside the dial. The first needle is set to the desired torque setting while the second needle is set to zero. As torque force is applied, the second needle moves along the dial. When the two needles meet, the desired torque has been achieved.
Because of their simpler torque mechanism, dial-type torque wrenches do not require as much maintenance and recalibration as click-type torque wrenches. Most models feature an audio-visual alert that indicates when the target torque is achieved. Dial-type torque wrenches are widely used in quality control applications to ensure that the torque applied in the production process complies with the stated specifications.
Electronic torque wrenches have become popular recently and are now available in traditional and dial-type designs. They use an electronic sensor to measure torque and show the torque value on a digital display. An audible and visual indicator informs the user that they are approaching the desired torque value and when the exact value has been reached.
Electronic torque wrenches are very accurate. However, their more delicate construction requires extra care when handling, and they require batteries to operate.
Dial-type torque wrenches do not require as much maintenance and recalibration as click-type torque wrenches.Gray Tools
Electronic torque wrenches are ideal in automotive and transportation settings because they can be linked to hardware, such as laptops, tablets and printers. In many heavy-truck repair environments, printed proof of wheel torque adjustments must be available as part of a certified repair service.
Finally, beam torque wrenches are the most basic torque wrenches available. However, they are difficult to read and the least accurate. As a result, they have virtually been eliminated from use in professional work environments.
Factory Certificate of Calibration—a Must-Have Document
A torque wrench should include a certificate of factory calibration. This proves that the tool has been inspected and tested at the manufacturer’s facility before final packaging and is within the stated accuracy range. Torque wrenches with missing or expired certificates of calibration should never be used.
A valid certificate of calibration should include the following:
- Torque wrench type, manufacturer, model number and range
- Equipment used to perform the calibration
- Torque reading clockwise and counterclockwise (if applicable)
- Calibration date
- Name of the person who performed the calibration and his/her supervisor
- A statement indicating that the torque wrench was calibrated to meet the accuracy in specifications as stated in the American Society of Mechanical Engineers (ASME) B107.14M-1994, GGG-W-686, Type 2, Class A Style 1, 2 and International Organization for Standardization (ISO) 6789
- A premium quality torque wrench will also include text indicating that the wrench was calibrated on a torque standard traceable to the National Institute of Standards & Technology
Generally, all torque wrenches should be recalibrated at least once per year or every 5,000 cycles. More frequent calibration is strongly suggested if the tool is used regularly. Because torque wrenches are stored in their protective cases at their lowest setting when they leave the factory, the one-year calibration guideline does not begin until the tool’s first use.
Torque Wrench Selection Checklist
The next step is choosing the ideal torque wrench that best suits the application (for multiple applications, more than one wrench may be needed). Here are some guidelines:
- Do you need to tighten fasteners to multiple or single torque values?
- What is the lowest and highest torque value at which you will be setting fasteners?
- What drive sizes are the sockets you will most commonly be using (¼ inch, ⅜ inch, ½ inch, ¾ inch or 1 inch)?
- Do you need the torque wrench to operate in clockwise and counterclockwise directions?
- What level of precision do you require?
The most important consideration in the selection process is understanding the torque range that the user will most commonly be working within. Torque wrenches operate best within 40% to 80% of their working scale. Therefore, do not choose a wrench that will be primarily used at the bottom or top end of the scale.
Torque Wrench Use & Maintenance Do’s & Don’ts
Good quality torque wrenches are an important investment for any professional. Because of their role in ensuring that critical parts are correctly fastened, proper use and maintenance are required. Here are some things to consider:
- Never use a torque wrench with a missing or expired certificate of calibration.
- Never use a torque wrench to break fasteners loose.
- Always perform the preventive maintenance required by the manufacturer.
- Never set the wrench at values higher or lower than those indicated on the scale.
- When not in use, clean and keep the torque wrench in its storage case at its lowest torque setting.
- Handle the torque wrench with care. Dropping a torque wrench will cause a loss of calibration.
- Never disassemble a torque wrench yourself. Repair and recalibration should only be done by an accredited laboratory, as per the manufacturer’s instructions.
- If you buy a used torque wrench, properly calibrate it before the first use.
- Never exceed the rated torque of the tool. Over-torquing will result in a wrench or part failure.
- Do not use a cheater bar or any other type of extension on the handle to apply extra torque. If extra torque is required, consider a larger torque wrench or the use of a torque multiplier.
With proper care and maintenance, a torque wrench should provide reliable service for many years. In addition, users will have peace of mind knowing that the fasteners on their equipment are properly secured, helping ensure safety and success on the job.