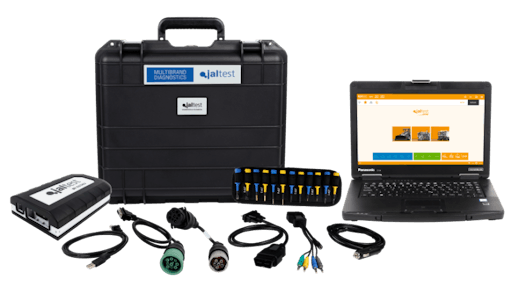
Modern construction equipment has journeyed through a transformation from mechanical systems to electronically controlled systems over the past couple decades.
This has a major impact on the role of the service technician. “Repairs used to be mainly mechanical,” says Bruno Gattamorta, vice president of sales and marketing, Cojali USA. “There were some thermal dynamics and some basic electronics, but it was pretty much mechanical.” The solution was typically pretty easy to identify.
This changed as electronic engine controls were introduced to meet ever more stringent emissions regulations. “Technicians were trained to fix mechanical issues and now the vehicles have electronics.” Now technicians must address electrical and emissions systems issues, which requires a different skill set. “We need a solution for fleet managers or rental yards to be able to connect to these machines and identify what’s wrong, because it is no longer a mechanical issue,” notes Gattamorta. “There’s code behind it. There is a fault code. That’s where the necessity of diagnostics comes along. It helps you build a game plan to see what is wrong.”
For example, emissions systems now account for a significant amount of the downtime issues. This is something rather new to the more senior technicians. “If you are a technician that has been in the field for 20 or 30 years, you had to learn on the fly, so it turns into a big problem,” says Gattamorta. Cojali dedicated some of its training resources and wrote a white paper on the aftertreatment [emissions] systems and how you can monitor the SCR and DPF with diagnostic tools to keep the machine operating.Diagnostic software will allow you to identify the fault code downstream and track it upstream all the way to the maintenance issue.Cojali
Diagnostic tools, such as Jaltest, can help the service department identify and head off costly oversights. “If I have to run a regen because my operator didn’t run the manual regen and you have to do a forced regen, you are talking $600 to $1,400 per operation,” says Gattamorta. “That’s an automatic impact on the bottom line. Having the right tool is just the forefront to building a maintenance plan. What this tool offers you is the opportunity to identify, build a game plan and control the elements so you’re always in that situation where uptime is increased.”
Become Self-sufficient
Relying on outside services, such a dealer, to troubleshoot machine fault codes can lead to increased wait times vs. identifying the root cause yourself. Technicians can almost immediately identify the value of diagnostic tools. The challenge comes when the customer needs to purchase five or 10 of the diagnostic tools for the shop, which can turn out to be a significant investment.
But the return on investment needs careful consideration. “It’s a matter of giving your team the right tools,” notes Gattamorta. “What good is it to have the best mechanics in the world and not give them a tool to identify what is wrong? It allows you to take advantage of your human resources, which are one of the most important things that you have. Everybody knows how difficult it is to find a good diesel technician, so why have a good diesel technician and have to call a dealer or have a mobile mechanic come out and do these actions for you?”Cojali
“Sometimes you get guys who have never worked with a diagnostic solution,” he explains. “They have only been able to call the dealer. They have a great relationship with the dealer. It’s been solving their issues.” But using a diagnostic tool allows you to quickly identify the problem yourself, which saves time.
The software guides the technician to the exact problem. “It’s not hit or miss.” You are no longer throwing parts at the problem. “It will allow you to identify the code downstream and track it upstream all the way to the issue. All the way through the value chain you are going to be able to see, point and identify. It is going to turn your average tech into a rock star.”
Diagnostics Must Be User-friendly
One key to success is the user interface. “The learning curve is probably of the biggest hurdles for adoption,” says Gattamorta. “We try to simplify that so it can be intuitive and easy to use.” Sometimes the user interface makes the diagnostics software difficult to use. Technicians and service managers are great with machines. “Are they great with software? Some yes, some no,” reports Gattamorta.
Right now, the aftermarket offers basic code readers which use the J1708 and J1939 industry standard protocols. “They are low level code readers, small guidance and it’s going to be better than nothing. But it’s not going to be that dealer level function that you want to go into.
“Then you can jump into the higher-level tools,” he says. “These are the ones that are actual game changers. The focus is on proprietary data. That means getting the codes with the exact same reference that the OEM has.” These transcend simple reading devices and allow bidirectional communication so you are able to calibrate injectors, run regens, etc.
“The technical information that gets embedded into these tools and the guidance, those are very important elements,” Gattamorta explains. With the emergence of digital media there are on-line videos and tutorials that can walk a technician through how to use the tools, including specific tutorials on how to run a regen, how to calibrate an injector, etc. “These things are important because just having the right tool doesn’t mean you are going to know how to take advantage of it.” It is a constant learning curve and the vendor needs to be there and available.
“Everything is shifting to a digital model, so we’ve created what we call the Jaltest Crash Course,” says Gattamorta. “When you buy a tool, there is a set of videos. There are about 12 videos that you can connect on your own time on YouTube.” There are quarterly webinars on what is new and how to use it.
History is critical
Sophisticated diagnostic systems, like Jaltest, do more than read fault codes. “We like to say that we are more than just diagnostics,” he explains. “Sometimes you have multiple technicians in the shop and they don’t know what the last guy did, or they don’t remember what happened four months ago. So we integrated a Garage Resource Planning (GRP) system. Every time that you do a diagnostics report, every time you do a maintenance report, it gets stored. That is directly associated to the machine’s vehicle number.”Using a diagnostic tool allows the user to quickly identify the problem, which saves time and cost.Cojali
“How many times have we gone into a shop and seen a work report covered with grease,” says Gattamorta. “That’s not going to last very long. It is going to disappear, and that paper is going to disappear. How many times do you need a PDF document with key operating values on components on a specific engine that are supposedly in the shop and realistically they are not?” The GRP system eliminates these issues.
It allows the technician to pull the history of the machine. You can see which PMs were done and which ones are due. You can check maintenance notes, including notes on how to perform the procedures. Wiring diagrams, technical values and images are all included.
“You have trouble shooting trees associated with the fault code,” he adds. “It is going to tell me my 10 steps or seven steps to do and in between those steps there’s going to be a hyperlink to carry out that action.” This can make technicians who may not be experienced with a particular model very productive. “They are going to be more confident on the repair process.”
A key consideration is to pick a tool that will interface with all machines in your fleet. Most contractors run mixed fleets with several different brands represented. You want one solution that integrates with all of the different available machines.
Looking Toward the Future
Remote diagnostics is the future. “It’s an exciting time for the electronics and repair business and there’s a lot of things that are going to be coming online shortly,” he adds. Big data and AI promise a path toward proactive repair. “You’re going to be able to see that this machine tends to break at X hours.” So you can identify what is likely to break and adjust your PM structure to better manage uptime.
“The more information that you have, the better you can manage it, the better you are going to be at managing your uptime,” says Gattamorta.