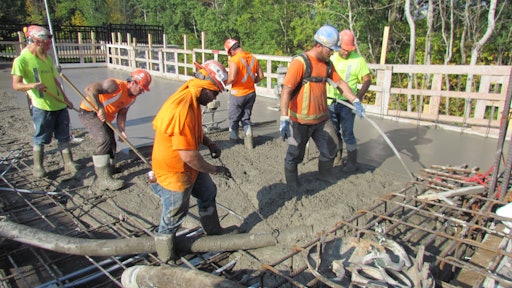
When choosing a method for monitoring the compressive strength of concrete, it’s important for project managers to consider the impact each technique will have on their schedule. While some testing processes can be done directly onsite, others require extra time for third-party facilities to deliver strength data. Time is not the only factor that contributes to project managers’ decisions. The accuracy of the testing process is just as important, as it directly effects the quality of the concrete structure.
The most common method for monitoring the strength of in-situ concrete is the use of field-cured cylinders. This practice has remained generally unchanged since the early 19th century. These samples are cast and cured according to ASTM C31 and tested for compressive strength by a third-party lab at various stages. Usually, if the slab has reached 75% of its designed strength, engineers will give the go ahead to their team to move on to the next steps in the construction process.
There have been many developments to speed up the curing process since this testing method was first introduced. This includes the use of heating blankets, additives and vapor retarders. However, contractors still wait three days after placement before testing for strength, even though their targets are often reached much earlier than that.
Despite knowing that, many project managers prefer to stick to this testing practice because it’s “the way its always been done.” That doesn’t mean this technique is the fastest and most accurate method, however, for testing the strength of all placements. In fact, there are many different practices aside from cylinder break tests that can be used. Here are seven different approaches to consider when choosing a method of strength testing.
Methods for Testing Compressive Strength of Concrete
1. Rebound Hammer or Schmidt Hammer (ASTM C805)
Method: A spring release mechanism is used to activate a hammer which impacts a plunger to drive into the surface of the concrete. The rebound distance from the hammer to the surface of the concrete is given a value from 10 to 100. This measurement is then correlated to the concretes’ strength.
Pros: Relatively easy to use and can be done directly onsite.
Cons: Pre-calibration using cored samples is required for accurate measurements. Test results can be skewed by surface conditions and the presence of large aggregates or rebar below the testing location.
2. Penetration Resistance Test (ASTM C803)
Method: To complete a penetration resistance test, a device drives a small pin or probe into the surface of the concrete. The force used to penetrate the surface, and the depth of the hole, is correlated to the strength of the in-place concrete.
Pros: Relatively easy to use and can be done directly onsite.
Cons: Data is significantly affected by surface conditions as well as the type of form and aggregates used. Requires pre-calibration using multiple concrete samples for accurate strength measurements.
3. Ultrasonic Pulse Velocity (ASTM C597)
Method: This technique determines the velocity of a pulse of vibrational energy through a slab. The ease at which this energy makes its’ way through the slab provides measurements regarding the concrete’s elasticity, resistance to deformation or stress, and density. This data is then correlated to the slab’s strength.
Pros: This is a non-destructive testing technique which can also be used to detect flaws within the concrete, such as cracks and honeycombing.
Cons: This technique is highly influenced by the presence of reinforcements, aggregates, and moisture in the concrete element. It also requires calibration with multiple samples for accurate testing.
4. Pullout Test (ASTM C900)
Method: The main principal behind this test is to pull the concrete using a metal rod that is cast-in-place or post-installed in the concrete. The pulled conical shape, in combination with the force required to pull the concrete, is correlated to compressive strength.
Pros: Easy to use and can be performed on both new and old constructions.
Cons: This test involves crushing or damaging the concrete. A large number of test samples are needed at different locations of the slab for accurate results.
5. Drilled Core (ASTM C42)
Method: A core drill is used to extract hardened concrete from the slab. These samples are then compressed in a machine to monitor the strength of the in-situ concrete.
Pros: These samples are considered more accurate than field-cured specimens because the concrete that is tested for strength has been subjected to the actual thermal history and curing conditions of the in-place slab.
Cons: This is a destructive technique that requires damaging the structural integrity of the slab. The locations of the cores need to be repaired afterwards. A lab must be used to obtain strength data.
6. Cast-in-place Cylinders (ASTM C873)
Method: Cylinder molds are placed in the location of the pour. Fresh concrete is poured into these molds which remain in the slab. Once hardened, these specimens are removed and compressed for strength.
Pros: Is considered more accurate than field-cured specimens because the concrete is subjected to the same curing conditions of the in-place slab, unlike field-cured specimens.
Cons: This is a destructive technique that requires damaging the structural integrity of the slab. The locations of the holes need to be repaired afterwards. A lab must be used to obtain strength data.
7. Wireless Maturity Sensors (ASTM C1074)
Method: This technique is based on the principle that concrete strength is directly related to its hydration temperature history. Wireless sensors are placed within the concrete formwork, secured on the rebar, before pouring. Temperature data is collected by the sensor and uploaded to any smart device within an app using a wireless connection. This information is used to calculate the compressive strength of the in-situ concrete element based on the maturity equation that is set up in the app.
Pros: Compressive strength data is given in real-time and updated every 15 minutes. As a result, the data is considered more accurate and reliable as the sensors are embedded directly in the formwork, meaning they are subject to the same curing conditions as the in-situ concrete element. This also means no time is wasted onsite waiting for results from a third-party lab.
Cons: Requires a one-time calibration for each concrete mix to establish a maturity curve using cylinder break tests.
More On Concrete Testing
How to Get the Best Results from Concrete Core Testing - Understanding the factors that affect core testing results will help you achieve accurate in-place concrete strengths.
What Contractors Need to Know about Field Testing Concrete - Project delays can be avoided by correctly field testing concrete products using appropriate methods and procedures.
Who Pays for Additional Testing? When an engineer, owner or general contractor requests extra testing for defects on a concrete job, know the facts on contractor responsibility for payment of those tests.
Concrete Densifiers Performance Test - Read about an industrial densifier/hardener performance test conducted by the CTL Group and Mark Wetherell. The test measured abrasion resistances of four different densifier types in accordance with ASTM C779-05.
What is Concrete Testing Software & How Can It Help? Four ways concrete testing software - or a construction materials testing platform - can make the concrete testing process easier and more accurate for concrete contractors.
Combined Methods of Strength Testing
A combination of these methods for measuring the compressive strength is sometimes used to ensure quality control and quality assurance of a concrete structure. A combined method results in a more comprehensive overview of your slab, allowing you to confirm strength data by using more than one testing method. The accuracy of your strength data will also increase as using multiple methods will help account for influencing factors, such as cement type, aggregate size, and curing conditions. For example, a combination of the ultrasonic pulse velocity method and the rebound hammer test has been studied. Similarly, when using the maturity method on your jobsite to test compressive strength, it is recommended to perform cylinder break tests on day-28 of your concrete’s lifecycle for acceptance purposes and to confirm the strength of your in-situ slab.
Summary of the accuracy and ease-of-use of in-place strength measurements techniques.Giatec Scientific Inc.
Choosing a Compressive Strength Method
Tests like the rebound hammer and penetration resistance technique, while easy to perform, are considered less accurate than other testing methods (Science Direct). This is because they do not examine the center of the concrete element, only the curing conditions directly below the surface of the slab. Practices, such as the ultrasonic pulse velocity method and the pullout test, are more difficult to perform as their calibration process is lengthy, requiring a large number of sample specimens in order to obtain accurate data.
Your decision in choosing a testing method may simply come down to what you know and are used to. However, the accuracy of these tests and the time they take to obtain strength data are significant factors that are not always taken into consideration as heavily as they should. Think about where all of your time and money goes during the construction of a project. How much of that is spent on repairs, fees for testing labs and extra labor to make sure your project finishes on time? The accuracy of the technique you choose can lead to future durability and performance issues of your concrete structure. Furthermore, choosing a technique that takes additional time to receive strength data can be detrimental to your project deadlines, negatively impacting productivity on your jobsite. Conversely, choosing the right tool can positively impact project timelines and allow you to finish the project below budget. How do you decide which strength testing method to use?
Editor’s Note: This article was contributed by Giatec Scientific Inc.