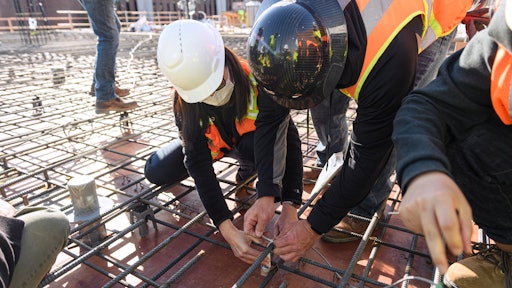
How long it takes to construct a building depends in large part on when the concrete of each floor is strong enough to take on loads. Purdue University engineers have developed sensors that could safely speed up a construction timeline by determining concrete strength directly onsite in real time.
Typically, concrete mix designs require testing before implementation in a construction project. Once those mixes have been vetted for use, the mix design cannot be altered without additional offsite testing.
The technology that Purdue engineers designed would remove the need for extensive offsite testing by allowing construction contractors to verify the concrete’s maturity onsite.
“Our sensors could help make better data-driven decisions to determine the construction schedule and improve the quality of concrete construction,” said Luna Lu, Purdue’s American Concrete Pavement Association Professor of Civil Engineering.
Purdue University engineers developed sensors that can instantly measure concrete strength, speeding up a construction timeline.Purdue University photo/Rebecca McElhoe
The Purdue team is working with F.A. Wilhelm Construction Co. Inc. to test and compare the technology with traditional commercial sensors installed into a floor of what will be Purdue’s five-story Engineering and Polytechnic Gateway Complex. The complex will be one conjoined building housing Dudley Hall and Lambertus Hall. The construction site is managed by Shiel Sexton Co. Inc.
Lu and her research team also are testing the sensors in highways across Indiana as part of an effort to better determine when concrete is ready to take on heavy truck traffic.
“We’re trying to work with contractors to find out how much saving we can do for them in terms of time, cost and the number of people needed at a site, which reduces risk and improves construction safety,” Lu said. “That starts with industry collaborations to evaluate how well the sensors work.”
Over the last decade, general contractors have used traditional sensors to make reliable and accurate estimates of concrete strength and maturity. But before even pouring the concrete, the method requires a monthlong process of testing the concrete mix design in the lab. A line graph is generated to note the strength of the mix design based on specific temperatures over time.
This line graph is then used to match up temperature measurements from sensors in the field. Strength values on the graph, called a “maturity curve,” help workers estimate when the concrete is strong enough to continue construction.
If unexpected weather or any other changed schedule impact calls for changing the mix’s main ingredients, then a contractor has to generate a maturity curve all over again for the new mix.
The sensors developed by Lu’s lab would measure concrete strength directly from the floor deck in real time, eliminating the need for generating a maturity curve beforehand.
“These new sensors are more of a ‘plug and play.’ We could make judgment calls on the fly,” said Ryan Decker, Wilhelm’s corporate quality assurance manager.
Like commercial sensors, Lu’s sensors would remain in the concrete. The sensors provide a more direct measurement of strength by using electricity to send an acoustic wave through the concrete. How concrete responds to particular wave speeds indicates its strength and stiffness.
“A wave propagating through concrete can tell us a lot of information. We can find out not only how strong the concrete is, but also detailed information about the concrete’s microstructure,” Lu said.
Twelve of Lu’s sensors have been installed into various sections of the Gateway Complex’s third floor so that the teams can best understand how well they work compared with commercial sensors in use on the site.
Lu’s lab has validated the technology and is now developing a system that contractors could use to remotely receive the concrete’s strength information. The sensor technology has a patent filed through the Purdue Research foundation Office of Technology Commercialization.
Construction of the Gateway Complex is expected to complete in fall 2022. The interdisciplinary hub will connect project-based instructional labs, design studios and other collaborative spaces to increase interaction between the Purdue community and Indiana companies. The creation of the complex is externally funded by the Lilly Endowment, the state of Indiana and private giving.