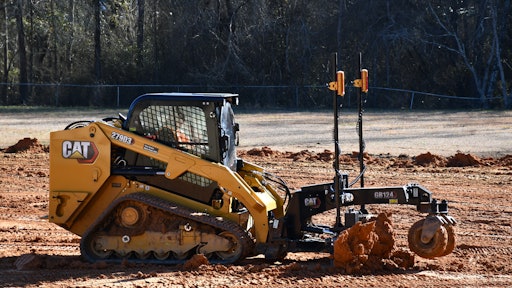
There's no doubt that compact track loaders (CTL) and skid steers are becoming more integral on construction jobsites. Not only are the machines easier to learn than their larger counterparts, but also offer unmatched flexibility in a variety of applications. With this trend, contractors are relying more heavily on interchangeable attachments, which can be digitally linked to the machines. Automatic grade control technologies have also advanced, transforming compact equipment into powerful precision grading solutions.
Several equipment manufacturers offer advanced grading options, through attachments and technology, to help contractors complete jobs faster, even if they’re short staffed. For instance, CASE Construction Equipment’s Precision Grader Blade is designed to give operators the performance of a motor grader in an agile, compact footprint. Compatible with 2D and 3D machine control systems, such as the CASE SiteControl grader solutions that are powered by Leica Geosystems, the CASE Precision Grader Blade is providing operators the benefits of machine control, along with large-scale enhancements.
“As an example, the grader blade is enabling operators to finish their work in fewer passes, while offering them greater quality assurance, too,” said Jeff Jacobsmeyer, product manager, CASE Construction Equipment. “In addition, it’s not only reducing the wear and tear of operators’ equipment, but it’s also delivering enhanced efficiency and quality in fine grading applications.”
Created for applications where operators need a motor grader’s precision performance, but are unable to justify it, based on its access, cost and size, the CASE Precision Grader Blade is allowing them to convert each of their large-frame CTLs into powerful precision grading solutions, as well. Aside from its power, the CASE Precision Grader Blade can be used on jobsites where larger machines aren’t feasible.
Furthermore, the CASE Precision Grader Blade is compatible with GNSS/GPS (single or dual), laser receivers (single or dual), sonic tracers (again, single or dual) and total stations. As a “plug and play” offering, it also has auxiliary hydraulics and a 14-pin electrical connection, which are suitable for large-frame CTLs.
“And it has a 108-inch moldboard that’s capable of jointly changing elevation and slope through dual lift cylinders, while achieving 60 degrees of combined blade rotation and 26 inches of combined blade side shift too,” Jacobsmeyer added. “All motion and action for the grader blade are controlled through a CTL’s existing joysticks, as no additional controls are required.”
Grading Box Provides Highly Accurate Performance
Alongside the CASE Precision Grader Blade, CASE Construction Equipment has created yet another automatic grade control technology offering: the CASE Precision Laser Grading Box. Used with CTLs and skid steers, the grading box is designed for fine-grading applications, ranging from concrete subgrade, to driveways and parking lots.
Featuring a reversible cutting edge on each of its sides, the grading box can also create very accurate finish grades — to within 0.1 inches. The grading box has distinct push-pull design grades, which can either move forward or in reverse, enabling operators to capitalize on the maneuverability of CTLs and skid steers, while also increasing their productivity.
In addition, the grading box has a hydraulic valve system, which can be modified whenever operators require adjustments. As a result of each of these attributes, it can provide operators highly accurate and effortless performance as well, even when it’s used in severe environments.
“The CASE Precision Grader Blade and the CASE Precision Laser Grading Box are also easy to use and learn, and they offer operators precision construction capabilities on equipment that’s highly accessible to a wide range of companies,” Jacobsmeyer said. “To experience these capabilities, companies won’t need to own any larger dozers or graders either.”
He continued, “And, by utilizing CTLs and skid steers, alongside the grader blade and grading box, operators are able to enter areas that larger machines, which also have precision technologies, simply can’t. Due to the CTLs’ and skid steers’ smaller sizes, they’ll be easier to transport from one job to the next as well.”
User-friendly Grading Products
For several years, Caterpillar has provided operators a variety of automatic control technologies, including Cat Grade solutions, which are attachment-mounted, aftermarket offerings that have been developed particularly for CTLs and skid steer loaders.
Meanwhile, the company has also added Cat Grade/Earthworks products — with sensor types like Global Navigation Satellite System (GNSS), laser and sonic, along with Universal Tilt Sensors (UTS) — on its box blade and grader blade attachments. And, finally, the company also has a laser-based grade system for box blades and grader blades, with Trimble’s Earthworks GO!, which is intended to be affordable, easy to use and entirely user-installed.
“In cooperation with Trimble, we have recently introduced the Earthworks GO! 2.0 2D system too, which is an update that’s providing operators Bluetooth-based communication, along with more robust components and improved user interfaces, when compared to the first version that was released,” said Jason Knowles, engineering specialist, Caterpillar.
Additionally, the company is offering operators Cat GB121/GB124 Smart Grader Blade attachments, which come directly from its factories with an Operator Assist feature. Developed by Caterpillar, the feature automatically controls cross slope as operators are grading.
The company also has blade slope sensors that are used with Operator Assist. Included with the Trimble Earthworks GO! 2.0 2D system, the sensor allows operators to upgrade to a grade control system in a more affordable and effortless manner, in comparison to other attachments, especially when it’s combined with a standard grade system wiring harness.
“Another new offering is the dual GNSS Cat Grade/Earthworks sensor on our company’s Cat Smart Dozer attachment,” Knowles stressed. “This system fills a different niche than the grader blade and box blade. After all, since it doesn’t guide wheels out front, the Smart Dozer is more suited to grading in small spaces and near obstacles, as operators can also spread truck dumps and cut out hard material.”
He added, “Similar to the grader, the Smart Dozer will arrive from the factory with an Operator Assist feature, thereby helping operators control blade slope and make smooth passes as they operate manually. When the grade system is installed, Operator Assist will work in parallel with Cat Grade to prevent ‘wash boarding’, while the grade system will drive the blade to target.”
Increasing Uptime
Kubota Tractor Corp. has also collaborated with Trimble, providing its dealers the Trimble Earthworks GO! 2.0 2D system, enabling them to offer their customers a complete system — through Kubota as a single source.
“The system is incredibly simple to set up and operate, as it can be installed or disassembled in just a few minutes,” said Jerry Corder, product manager, construction equipment, Kubota. “Not to mention, its calibration is simple and intuitive too.”
Operators’ smart phones can be used as control pads, as they’re connected to the system wirelessly, via a free app. As a result, operators can easily add updates and troubleshoot onsite, leading to a considerable decline in downtime.
“All controls and instructions are clearly laid out and shown on the app with animations and simple phrases, ensuring that nearly anyone can operate the system,” Corder explained. “This, in turn, will help operators fill positions on their jobsites.”
Aside from offering dealers and operators the Trimble Earthworks GO! 2.0 2D system, Kubota is also providing an open platform, bi-directional box blade, the BB3084/96. Compatible with third-party automated grade controls, the box blade is able to grade slopes and flat surfaces.
“And it will not only accept 2D and 3D grade controls systems, but a majority of the control systems that are on the market today, as it’s set up as an open platform,” Corder added.
Trimble’s technology is also used on Doosan Bobcat machines, which is a partnership dating back to 2015. Due to the collaboration, the company has offered the Trimble GCS900 3D grade control solution as an option for its CTLs and skid-steer loaders.
Paired primarily with Bobcat grader attachments, the system allows operators, particularly smaller contractors, to quickly and effectively work on complicated projects that require 3D machine control and digital designs. On the other hand, large contractors can use the system’s 3D machine control to finish the final phases of their projects more cost effectively and accurately, while using their Bobcat machines.
“Operators can choose between a GPS-based option for outdoor applications, and a universal total station (UTS) for indoor and outdoor applications,” said Mike Fitzgerald, marketing manager, Doosan Bobcat North America. “After the computer-generated model is loaded to the 3D system, it will automatically grade the ground with an accuracy of roughly 0.12 to 0.2 inches.”
He continued, “The UTS is able to measure angles and distances; by measuring known points of a jobsite, a total station can calculate its position, relative to known points and coordinates. In robotic mode, the total station will measure the position of the UTS target and report the position information, via radio link, to the UTS controller.”
Boosting Productivity With Automatic Grade Control
CASE Construction Equipment’s automatic grade control technologies, according to Jacobsmeyer, will help operators conduct their work tasks more efficiently in a variety of ways, including the following:
- Enhanced performance: Due to the technologies, operators will get up to speed, so to speak, quicker than they previously did, enabling them to enhance their productivity, which is especially critical as labor shortages continue.
- Quality: Not only will grading quality improve, but so will operators’ overall performances, leading to more efficient work productivity overall.
- Productivity: By reaching their grades or the contours of their plans faster, operators will also be able to focus on the next phases of their jobs in a timely manner.
- Reduced equipment wear and tear: Since they’ll complete their work in fewer passes, operators will also decrease the wear and tear of their equipment on a short- and long-term basis.
Meanwhile, by using Caterpillar’s grade control for CTL and SSL attachments, operators will arrive to their grades faster, more precisely and more effortlessly than they otherwise would have been able to, especially if they had previously used manual operations, Knowles said.
“In the real world, this means higher quality with less experienced operators, as operators are also able to achieve cost savings through more efficient material usage and move on to their next jobs sooner than they would have in the past,” Knowles said.
One operator can set grade and move materials accurately and efficiently without requiring any assistance whatsoever, while using the Trimble Earthworks GO! 2.0 2D system with the BB3084/96, Kubota’s Corder said.
The system, for example, will eliminate the need for extra workers on site, as operators no longer need assistance while acquiring measurements or using a grade stick. Furthermore, the system will completely remove the need for a second machine on site to pull from a spoil pile and add materials for an operator’s leveling machine, as one machine can conduct all of these tasks.
Corder said that, by adding the Trimble Earthworks GO! 2.0 2D system, along with the BB3084/96, to their toolboxes, operators will notice immediate increases in profitability and productivity, concerning the following areas:
- Labor: “A single operator with a single machine can do the work, so fewer workers are needed to perform the job,” Corder said.
- Materials: Due to the rise in accuracy that’s associated with the Trimble Earthworks GO! 2.0 2D system, operators’ material requirements are identified up front, enabling them to know exactly how much they need to order whenever they have to purchase materials.
- Timeliness: “With no measurements needed throughout the job to guarantee grade and level, operators’ jobs are completed much quicker so that they can take on more projects,” Corder added.
In full agreement with Corder’s insights, Fitzgerald has added that fleet owners are typically buying grading systems for one primary reason: to achieve materials savings.
“While conducting significant grading work for applications like asphalt, concrete (commercial or residential) and site prep, a highly precise grading system — such as Bobcat’s Trimble package, the Trimble GCS900 3D grade control solution — will ensure that there is no wasted fill material, along with more even spreading,” he said.
Operators will notice an increase in efficiency, along with a decline in the amount of time they have to spend on jobsites, when using the Trimble technology, Corder said. For instance, according to Fitzgerald, a Bobcat customer was able to complete a job in three weeks, rather than three months, as the customer had originally projected.
Along with the Trimble GCS900 3D grade control solution, operators are also implementing the Bobcat Automatic Grade Control Laser attachment on their jobsites. Able to be moved from one machine to another, the attachment is allowing operators to use industry standard Controller Area Network (CAN) harnesses for effortless transferring. Consequently, operators have another means to decrease their downtime and, ultimately, increase their bottom lines.
Preparing for the Future
While looking ahead to the future, Jacobsmeyer has predicted that precision construction technologies, particularly those that have been built for use on compact equipment, will continue to be adopted on a more frequent basis. This increase will especially occur as business owners and operators realize the practical benefits they provide, he said.
“These technologies won’t work for every CTL or skid steer owner,” he emphasized. “But there are countless types of work in which a practical grading solution, matched with compact equipment, has the opportunity to drive efficiency and performance for a business.”
Knowles, on the other hand, has projected that Caterpillar’s Cat Smart Dozer and Cat Smart Grader attachments will become increasingly utilized within the equipment industry, as a whole, for two main reasons.
“First, they are precision grading tools that can be used with our Grade Control,” he said. “And second, by integrating each of the attachments with our Cat host machine, operators will have easy, intuitive manual operation, as they can implement a joystick in the same manner that they would have if they had utilized a conventional dozer instead.”
These attachments can also be used in several applications.
“The attachments are also useful in a wide range of situations, which would have otherwise been difficult for operators in the past, as they would have had to use on/off push button controls, which are featured on other attachments,” Knowles said. “Therefore, the Cat Smart Dozer and Cat Smart Grader attachments will continue to be used more often. And, as a result, operators’ return on investments will be faster than they previously were.”
As CTLs and skid steers continuously become a more critical component of operators’ fleets, automated grade control technologies are subsequently being viewed as more integral offerings by various manufacturers, including Kubota. Due to automatic grade control technologies’ ever-rising popularities, Corder has noticed that more emphasis is being placed on the integration between the company’s powered units and their attachments during the products’ actual conceptions.
“The saying ‘work smarter, not harder’ has definitely applied to this segment — automatic grade control technologies as a whole — of Kubota Tractor Corporation’s business,” Corder said. “As owners utilize CTLs and skid steers more regularly, automatic grade control technologies will continue to positively impact more and more construction jobsites worldwide.”