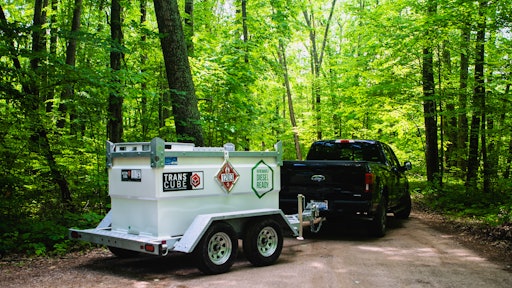
The construction industry is constantly changing. The days of operating diesel-powered equipment without worrying about environmental regulations are long gone. As more fleets and jobsites strive to meet “green quotas,” reduce emissions and operate sustainably, they’re upgrading to new equipment powered by Tier 4 Final engines. This adds the wrinkle of constantly filling this equipment with diesel exhaust fluid (DEF). On the surface, environmental considerations and the DEF factor can be intimidating. However, opting for renewable diesel and the proper storage solution for both fuel and DEF can lead to worry-free compliance.
A New Diesel
Diesel-powered equipment is vastly popular since it excels in heavy-duty jobs. Petroleum diesel has been the norm, but it contributes to air pollution and is derived from a nonrenewable energy source. Biodiesel entered the conversation and offered an option to reduce these concerns. However, it has limitations. It’s not a direct drop-in replacement for diesel and doesn’t perform as well in cold weather because of its chemical composition. Additionally, biodiesel is more prone to growing mold if stored in a warm storage tank for too long. Renewable diesel, though, features components that maximize the perks of both biodiesel and petroleum diesel, making it viable for both now and the future.Renewable diesel is a sustainable, low-carbon biofuel derived from waste products and other biomass such as vegetable oils, greases and natural fats that reduce particle emissions.Western Global
Renewable diesel is a sustainable, low-carbon biofuel derived from waste products and other biomass such as vegetable oils, greases and natural fats that reduce particle emissions. It’s processed by treating oils with hydrogen, which removes the limitations related to reduced shelf life and cold-weather performance that first-generation biodiesel encountered.
Renewable diesel production starts by saturating feedstocks, like vegetable oils or waste fats, with hydrogen at temperatures above 572°F. The process ends with isomerization, which creates a fuel almost chemically identical to petroleum diesel. This allows renewable diesel to be used interchangeably with petroleum diesel without additives or special blends.
The Perks of Going Renewable
Renewable diesel provides an array of benefits when used as a direct, drop-in alternative to petroleum diesel. From reduced equipment maintenance to prolonged storage life to environmental benefits, renewable diesel’s positives make it an ideal option for any application requiring diesel power.
Its clean-burning properties reduce particle production by 50%, improving air quality. This helps contractors meet carbon emission targets for jobs while potentially limiting the need for other changes that could take a toll on worksite efficiency. The reduced particulate production also aids in improving engine cleanliness and extending the machine’s life.
Before opting for renewable diesel, it’s important to confirm that the original equipment manufacturer has approved the use of the fuel with its engine and ensure that your fuel storage tank or other solution is renewable-diesel compatible.
Adding DEF to the Mix
Another prominent component in a reduced-emission construction world is DEF. As contractors upgrade to equipment powered by Tier 4 Final engines, DEF has cemented itself as an industry mainstay. DEF provides safer emissions, improved fuel efficiency and optimized combustion. It also has its challenges, including:
- UV sensitivity
- Storage requirements to maximize shelf life
- Transfer into equipment without contamination
The fluid is vulnerable to impurities, so even miniscule contamination can cause considerable issues for an operation. DEF is also sensitive to ultraviolet rays and extreme temperatures with an optimal storing temperature range between 12°F and 86°F. Given those stipulations, finding proper DEF storage solutions can be complex.
Converting to Bulk Storage
Contractors typically obtain DEF stocked on pallets with several 2.5-gallon jugs. Storing these jugs in a temperature-controlled environment can be challenging, and manually carrying the jugs to pour DEF into equipment is time-consuming and may impact the operation’s efficiency while producing a large amount of plastic and cardboard waste. Furthermore, the relatively small quantity requires frequent monitoring and refilling equipment.
DEF storage tanks range in capacity, allowing contractors to select a tank that maintains the proportional relationship of about 10% of DEF per gallon of diesel fuel, allowing DEF and diesel drops to coincide.Western Global
Larger tanks supply many benefits, but some still pose challenges, and not all are universal DEF solutions. Several aspects must be weighed when looking for the optimized DEF tank:
- Equipment. One aspect to consider is whether the equipment is stationary or moves throughout the jobsite. For mobile equipment, consider a storage manufacturer that offers a manual transfer pump with a nozzle compatible with the full fleet. Many DEF storage tanks are on the market designed to accommodate specific stationary equipment. While they provide a custom-engineered solution for machinery, they may not work for the entire fleet. To extend the runtime of stationary equipment like generators and pumps, look for a system that is compatible with all equipment on the jobsite. Some universal solutions also monitor the level of DEF and automatically refill the equipment as needed. This removes the need for constant monitoring to refill the machine and can match an auxiliary fuel supply to extend runtime by up to a week.
- Capacity. DEF storage tanks range in capacity, allowing contractors to select a tank that maintains the proportional relationship of about 10% of DEF per gallon of diesel fuel. Ensure that the selected DEF storage allows for this ratio to time DEF and diesel drops to coincide. If fueling mobile and stationary equipment from the same tank, consider a 20% DEF-to-diesel ratio to align consumption rates for fuel drops.
- Construction. Contractors should then consider their fuel storage solution and determine whether a separate DEF tank or two-in-one solution would be optimal for the jobsite. Standalone DEF storage tanks have a large capacity and are more transportable with features like four-way forklift pockets, stackable corner brackets and a rugged exterior. They can be situated next to onsite fuel storage tanks, allowing operators to simultaneously fill DEF and diesel. Look for standalone tanks that offer double-walled containment and a design that provides DEF storage over an extended period in any climate. DEF storage tanks that have built-in, weatherproof containment eliminate setup time by not requiring secondary pans or basins. Some offer a poly inner and steel outer tank for a lighter-weight solution that makes it easier to store DEF onsite in both hot and cold conditions. Alternatively, some manufacturers offer DEF storage tanks that mount on top of transportable onsite tanks for a convenient, two-in-one solution. These tanks should include an RSV for closed liquid transfer. This means the valve automatically closes once disconnected, keeping the fluid in the hose as well as sealing the tank against contamination.
- Transportability. Lastly, contractors should consider whether their DEF storage tank needs to move throughout the jobsite. Top-mounted tanks move along with the fuel tank, and some standalone DEF storage tanks feature forklift pockets for easy transport. Additionally, some models have corner brackets to make them stackable to reduce their physical footprint.
Storage Solutions
Fuel storage considerations also play into sustainability on the jobsite. From containment to tank placement and fuel management, several elements must be considered. Fuel storage regulations vary depending on location and the tank’s purpose, but typically require a UL-listed tank and some sort of secondary containment.
Some manufacturers offer DEF storage tanks that mount on top of transportable on-site tanks for a convenient, two-in-one solution.Western Global
Fuel storage onsite can further reduce operating costs and environmental impact by being strategically moved and placed in areas that reduce the distance that equipment needs to travel to refuel. It also minimizes the number of deliveries to the site, meaning fewer emissions from transport. Furthermore, reduced travel distance reduces undercarriage wear and tear on equipment. Using onsite storage tanks with a fuel management system allows contractors to monitor fuel usage as well, which delivers accountability for every drop of fuel.
A More Sustainable Future
In an industry that’s becoming increasingly conscious of protecting the environment, regulations will likely continue to increase. Using fuel and fluid storage tanks built and ready for renewable diesel and DEF sets contractors one step ahead, while offering improved efficiency for operations.