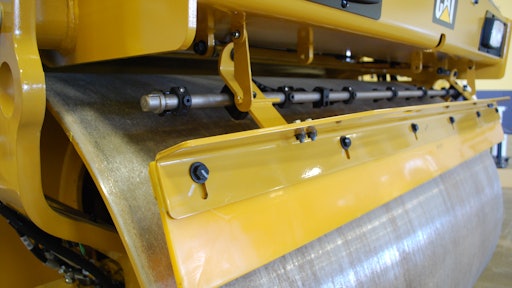
Asphalt rollers are highly reliable machines, but when one goes down unexpectedly in the middle of paving, it can have costly repercussions for the entire operation. It can affect mat quality, result in lost time and potential risk of fines due to project delays, plus there is the extra expense associated with any unscheduled service and repair.
Keeping rollers in peak condition throughout the season can help you reduce such risks and maximize the potential to meet both project specs and deadlines. As with any machine, the better it is maintained, the better it can perform its intended task throughout its lifetime in your fleet.
Inspect and Maintain
Regular service checks are essential to keeping rollers working properly, and a number of them can be completed as part of the daily walkaround inspection. Review the service manual for specific guidelines, but at minimum:
- Check engine oil and hydraulic oil levels and fill as needed.
- Check coolant levels and ensure the cooling system is clean and clear of debris; replace the air filter if needed.
- Inspect engine, hydraulic system and fuel filters and replace as needed.
- Visually inspect external hardware for loose connections or leaks.
- Check controls, brakes, backup alarms, warning beacons, headlights, etc. for proper operation.
- Make sure the drum is clean and there are no dings or scrapes in the drum surface(s) that could mar the mat.
- Ensure tires on single-drum rollers are in good condition and are inflated to the recommended pressure.
- Periodically inspect the shock mounts, which isolate the vibration of the drum from the operator; replace as needed.
Maintenance of engine and hydraulic system components is particularly critical. The engine must be able to operate at the specified rpms in order for the vibratory system to achieve the proper compaction output. Follow manufacturer recommendations for scheduled engine and hydraulic system service intervals to ensure optimum performance.
Keep Water Flowing
The water system serves as a lubricant to prevent asphalt from sticking to the drum and damaging the mat. As such, it’s important to make sure all aspects of the water system are properly maintained and in working order.
One of the most common problems encountered is clogged spray nozzles, which can lead to pump failure over time. To minimize the risk of debris entering nozzles from the water tank, fill the tank with clean water from a known source whenever possible. If you will be working in an area where water quality is uncertain, make sure the operator checks the water filtration system frequently.
Initial filtration for the water system is at the fill point; it serves as the first and best line of defense against debris ingress. Caution operators against removing the screen to speed the water fill rate.
Even if the roller has multiple filtration points prior to water reaching the pump, continual use of an unclean water source can diminish water system performance. Filters can become compromised, making it harder for them to remove debris. To maintain proper water flow:
- Check the filters according to manufacturer recommendations; adjust the frequency of inspection as needed based on water quality.
- Periodically remove and inspect the sprinkler bar nozzles to ensure they’re not clogged or damaged.
- Make sure spray nozzles are properly adjusted so they distribute water evenly across the drum.
- Check the water tank regularly for algae, calcium deposits or other contaminants.
Scraper bars also play a role in water system performance. Not only do scraper bars keep the drums free of material buildup, they hold the water in between the scraper and drum to keep the drum lubricated. The scraper system needs to be in contact with the drums at all times to spread the water consistently.
If scraper bars are not properly adjusted, or have excessive wear, water may not reach fully to the edges of the drum, causing asphalt to stick and mar the mat. Check scraper bars regularly for proper adjustment and excessive wear, and replace them as needed.
Proper Operation
Operating procedures greatly affect the life cycle of any machine, and rollers are no exception. Jumping curbs, shifting quickly from forward to reverse, rolling over sharp rock or uneven materials, etc., can accelerate wear and/or damage the drums and other components. Make sure operators are trained in what they should, and should not, do during roller use.
Over compaction can have negative repercussions on roller longevity, as well. As material is compacted, it absorbs less of the energy generated by the drum. That energy can be transferred back into the machine, potentially damaging the isolators within the drum, or causing premature bearing wear or damage.
To minimize and/or eliminate over compaction, establish a rolling pattern for each job and verify it through testing. Compaction meters or monitors can further reduce over and under compaction risk.
Resources: BOMAG, Case Construction Equipment, Caterpillar, Hamm Compaction, Wacker Neuson