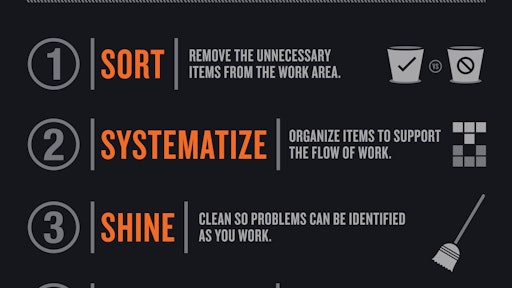
Managing a rental business in today’s “unprecedented” times is more complex than ever, and that means waste and inefficiencies may have crept into your operation without you being aware.
In the 2021 State of the Industry report in Rental, Josh Nickell, vice president of the equipment segment for the American Rental Association, noted the effect of rapid change on the industry, “As an industry, we saw things that might be on a 10-year roadmap became 2020 priorities.” The need for constant adaptation to change can be challenging, but one way to make it easier for your business is with a framework like Toyota Lean Management (TLM).
What is Lean Management?
The core pillars of lean management methodology are respect for people and continuous improvement. The entire concept of lean management is derived from the Toyota Production System (TPS), established over 70 years ago.
Now, TLM focuses on eliminating waste by implementing all of the elements of the lean methodology of the TPS, which can be applied to any industry. Therefore, it's not just for manufacturers; these principles can be applied in any area of your rental business.
If you aren’t familiar with lean management, you may wonder, “How can I get started on my own lean management journey?” Let's talk about that.
The 5S System
The foundation of lean management is the 5 “S” system. This is a workplace organization method that describes how to organize a workplace or business for efficiency and effectiveness. In its entirety, it's a framework that emphasizes a specific mindset and tools to meet a goal.
To dive in further:
- Sort: Sort through materials, keeping only the essential items needed to complete tasks.
- Set in Order: Ensure that all items are organized and have a designated place.
- Shine: Proactive efforts to keep workplace areas clean and orderly to ensure purpose-driven work. This can be maintenance on equipment or dusting/cleaning the office.
- Standardize: Create a list of standards for both organization and processes.
- Sustain: Sustain new practices and conduct audits to maintain discipline.
Overall, the five disciplines are designed to improve efficiency, reduce waste, and create collaboration in work flow, processes, time, and more. The 5S system can be explored in depth in this video created by Toyota Material Handling.
Visual Management
As mentioned earlier, a key building block of Toyota Lean Management is respect for and empowerment of people. Your employees are at the heart of your company’s lean management success. They are the ones who inspire change, produce solutions, and work to reduce waste. If a company doesn’t believe in the value of its employees and support them in that mission, then the processes that connect everything will break.
How can you make sure that all of your employees understand the goals of your business? Visual management practice is an important component in creating a shared vision. This means that instead of just telling associates the goal, you must make that goal understood in a way that is trackable and can be seen.
Therefore, make sure to work on things that you can see when first starting your lean journey. If you see the change, you can start to understand the impact it's making. At Toyota Material Handling, we use problems and problem-solving as powerful opportunities for learning and performance improvement. To do this, you first need to make invisible problems visible. Start with something simple that could make a noticeable impact on you or your company, like your desk or workspace.
Another method for implementing visual management could be as simple as displaying boards that show business goals and updating them when you are behind or ahead of schedule. And remember: make sure they're visible to all employees. Then, establish a cadence for review as a team and decide on next steps as a team, creating alignment and velocity toward improvement.
PDCA Cycle
Once you have identified visible problems, you can plan countermeasures to address the problems. With a countermeasure in place, you must also decide upfront how you will monitor and check its implementation. Knowing who will follow up and when is crucial in the Plan-Do-Check-Adjust (PDCA) cycle.
Just as a circle has no end, the PDCA cycle should be repeated again and again, as it ensures that countermeasures are being implemented correctly. If the execution of the countermeasure is appropriate but the results are not where you need them to be, adjust along the way and restart the PDCA cycle.
And importantly, if you’re a manager, practice Genchi Genbutsu – “Go and See.” You can’t be an effective lean manager if you never leave your office. You have to go and see how your team is working and where they need assistance.
Never Stop Improving
While this all may seem like a small start, getting in the habit of practicing the 5S process, visual management, and the PDCA cycle can be helpful as you move on to larger, more impactful projects.
One thing to keep in mind is that your lean journey will never be “complete.” There will always be something in your rental business you can improve or adjust to eliminate waste. A cornerstone of your lean journey will be kaizen, which means “continuous improvement.” At Toyota Material Handling, kaizen is practiced daily in team meetings, in maintenance shops, on the factory floor – everywhere people and processes are at work. This is especially true now because, if the pandemic has taught us anything, it’s that adaptation is the key to business survival and success.
In the next part of this series, we will examine how standardization—Seiketsu in the 5S process—can be applied in your company to improve efficiency, productivity, and the bottom line.