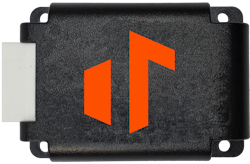
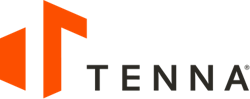
Tenna has announced the release of a new hardware product for heavy equipment that allows for tracking third-party powered accessories. Tenna also released a new add-on product: Custom Inspections.
Tenna’s new TennaCANbus tracker is an updated way to track heavy equipment. By installing the TennaCANbus on heavy equipment, users can now track and monitor idle time, fuel consumption, asset information, engine information, battery level, fault codes and decoded messages, environmental data and tracker analytics—in addition to the location, utilization and maintenance data previously collected.
CAN (Controller Area Network) or CAN bus is a widely used communication protocol that allows different electronic control units (ECUs) within a vehicle or piece of equipment to communicate with each other. It is a network protocol that helps data exchange between various systems—such as the engine, transmission, brakes, sensors and more. CAN bus caters to real-time, reliable and robust communication, making it possible for applications requiring data coverage and integration between different machine components.
TennaCANbus enables construction equipment managers to make decisions about rentals, replacements, preventative maintenance and resource management. The tracker also makes it possible to track external power take-off (PTO), which enables the use of an asset’s engine power to drive added equipment or perform specific tasks. External PTO is used to provide power to external accessories, including hydraulic pumps, generators, winches, compressors and other types of equipment that require mechanical or electrical power to operate.
“This is an evolutionary step for us to have hardware that can get even more data off of a machine,” said Jose Cueva, co-founder, and vice president of product at Tenna. “It also captures any factory installed or after-market PTO, making it a comprehensive device for a wide array of data that can inform better field decisions, maintenance planning, and resource management.”
TennaCANbus can be used to support construction operations. Maintenance, diagnostic troubleshooting and service planning are supported with additional information on runtime and frequency of PTO engagement. Fuel use and idling metrics provide information related to the occurence of waste and excessive wear and tear. Understanding more about how heavy equipment is being used, including when PTO is engaged, can simplify reporting around compliance with safety regulations and support billing.
Tenna’s new Custom Inspections is an add-on to the Safety and Compliance license, which lets project, safety and administrative personnel manage and monitor safety and compliance across an equipment fleet. Tenna’s digital inspections are designed to replace paper-based methods. The new Custom Inspections add-on allows users to create inspections specific to jobsites, use cases or types of equipment, mandate custom fields and signatures and apply new forms to all applicable assets.
“Custom inspections are an excellent way to tailor inspections to unique use cases. If a certain type of asset is prone to leaks, you can add custom fields to an existing inspection form to check for that. If assets on a particular job site seem more prone to external damage, you can create new forms for anything allocated to that site. Inspections become more useful and more meaningful," said Cueva.
With the launch of these new products—as well as ongoing enhancements to existing features—Tenna demonstrates its commitment to helping construction companies.