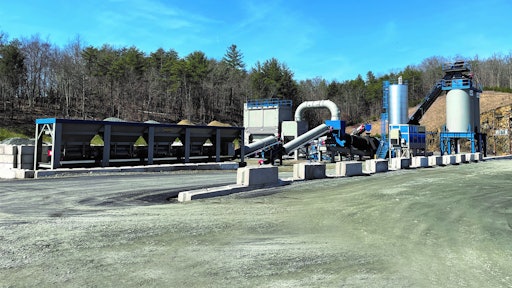
The conversation around asphalt plant emissions can be highly technical, and sometimes confusing. However, with the passage of new legislation like the Inflation Reduction Act, there are more direct incentives than ever to bolster your production efficiency, evaluate weaknesses in the systems you use, and either upgrade or retrofit them to reduce your carbon footprint and overall emissions.
In a memo request for comments on energy security tax credits for manufacturing posted to the IRS government website, (2) Section 48C(c)(1)(A)(ii) adds to the list of eligible projects any project that re-equips an industrial or manufacturing facility with equipment designed to reduce greenhouse gas emissions by at least 20% through the installation of certain systems, including through the installation of energy efficiency and reduction in waste from industrial processes.
The National Asphalt Pavement Association (NAPA) has set a highly publicized goal of net zero carbon emissions by 2050, and it's an admirable, if not ambitious goal considering some of the technological innovations such a leap might require, from where the industry stands today. Also, it's not purely about innovation, it's also about adoption. NAPA concluded as much in the industry emissions inventory it released in June of 2022.
"Cradle-to-gate GHG emissions could be reduced by up to 24% relative to 2019 emissions by implementing certain environmentally preferable technologies and practices," the report continues. "Even with widespread adoption of readily available technologies and practices, the 24% reduction in GHG emissions is not sufficient to achieve net zero GHG emissions. New technologies and additional innovative practices will need to be developed and implemented to achieve more significant GHG emission reductions."
Making the Proper Distinctions
When facing the task of reducing plant emissions, there's a somewhat innocuous question that comes up, that may seem obvious on the surface, but when you closely consider it, the answer isn't so straight forward. Are all plant emissions controllable through technological (either by mechanical or chemical) means?
"It is important to distinguish between types of emissions from a facility – process and fugitive. We must also distinguish between carbon emissions and all other emissions," said Catherine Sutton Choate, IPS Director of Product Documentation and Environmental Compliance at Astec Industries. "We can effectively control all types of emissions through application of suitable technology and implementation of recommended operational procedures."
Process emissions means those from industrial processes themselves involving chemical or physical transformations. This includes all gases discharged from the exhaust stack. Fugitive emissions are those unwanted and undesired releases of gasses, fumes, and/or other particulates not intended as part of that regular transformation process. Think blue smoke, dust, and other fines that can escape and be blown around the environment of the plant. The primary process emissions controlled are:
- nitrogen oxides (NOx)
- carbon monoxide (CO)
- carbon dioxide (CO2)
- particulate matter
In addition to these, sulfur dioxide (SOx) are primarily caused by oxidation of fuel-bound sulfur and volatile organic compounds (VOC) are caused from unburnt asphalt fumes when liquid asphalt is introduced into the drum mixers.
There can be multiple sources for these emissions throughout any asphalt plant, but generally, the largest contributor of these emissions is from drum mixers, due to the dryer burners and the fuel they consume. This means both the type and volume of fuel consumed. Hot oil heaters, the plant's exhaust stream, and, those emissions from the heated asphalt cement binder and final asphalt mixtures due factor in. However, according to Choate, "Overall emissions from the asphalt binder associated with silo filling and truck loading are more prevalent than emissions from the hot oil heater, even if it operates year round."
If the drum mixers and their burners are the primary source of green house gasses, then what can be done about it? A large amount of heat is needed to dry aggregates allowing for the proper production of asphalt pavement.
Controlling the Process
What Goes in Must Come Out
This is the foundational concept behind understanding emissions and GHGs. The fuel used to heat the asphalt mix, to power the burners, is the front line in the emissions battle. Some fuel sources are better and cleaner than others. What fuels are better at bringing down the threshold?
"The lowest levels of NOx are achieved using natural gas. It burns cooler than oils and has no nitrogen in it, making it inherently a lower producer of NOx," said Gencor's Dennis Hunt, Senior Vice President.
In fact, according the NAPA inventory, the asphalt production industry is already the leader of all industrial sectors when it comes to natural gas fuel consumption as a percentage of overall adoption. But their study showed there's still room for significant improvement. NAPA said that when natural gas is not available, plants typically burn used oil or diesel fuel instead. However, there is a growing market for using liquid natural gas (LNG). From their baseline evaluation, on average, plants were utilizing 69% natural gas in overall fuel consumption, and sees the longterm goal as shifting that needle towards 90%.
Hunt continued, "The use of low NOx burners, and low NOx burners with flue gas recirculation introduced into the highest flame temperature region reduces the flame temperature from the burner and effective burner controls are the current tools in place that are now effectively used to meet the most stringent air quality districts rules for NOx emissions."
These burner controls are extremely important, in fact, just as important as the type of fuel you choose. Jeff Meeker, President of the Meeker Equipment Company said, "The industry has really tightened down on initial requirements for the asphalt plant. Which means the burners and the burner controls are very critical to the asphalt plant."
The modern burner controls are such that all of the ignition points across a plant can be digitally stored so that as the burner opens up and starts to produce more emissions, it tries to keep the optimal emissions for that specific burn, bringing it back within a desired range.
A Complimentary Element
Hydrogen is poised to be a major player in more ways than one. As an alternative to EVs, hydrogen powered trucks, excavators, and other heavy construction equipment can reduce overall carbon footprint for a plant's operations. According to some experts, by 2030 the amount of permissible hydrogen content in existing natural gas lines could increase by up to 20%.
This is far from a "new" technology, it's a clean fuel, and it can reduce GHG emissions. Hydrogen is light, energy-dense, and produces no direct emissions of pollutants and no greenhouse emissions. "[However], when hydrogen is added to natural gas above 5% by volume the flame temperature will increase with a resultant increase in GHG emissions from the burner, Hunt warned that, "Mitigation efforts will need to be introduced to compensate, such as flue gas recirculation, water injection in the low NOx burner technology."
Producers who are able to take advantage of the increases in hydrogen will be in a more flexible position, and should stay aware of their state and local regulations regarding its use as the rules continue to evolve.
It's Electric!
In the January 2023 issue of Asphalt Contractor, in the article "The Heat is On", it covered one of the best ways to improve energy consumption. From that article, "When choosing energy for asphalt heating, it’s important to look at the entire picture. Cost-per-unit of energy to heat asphalt and oil is certainly part of the puzzle — but it is not the only cost. Also important is the heater’s thermal efficiency. A small difference in efficiency can make a big difference in how much fuel a heater burns over its lifetime."
Jeff Meeker mentioned a forthcoming product from his company, to be shown at ConEXPO later this year, "Electrically heated, heat transfer oil is a product that we know is going to be good for the industry in terms of planning missions," he said. "Plants are permitted based upon total emissions. They add up the hot oil heater, as well as the main aggregate burner. This will substantially reduce the hot oil heater emissions as opposed to gas or oil fired burners."
ALmix, as well as Astec, both offer versions of the electrically heated systems for AC storage systems, which does increase the amperage draw for plant. "Electric heating elements are used to maintain the AC temperature in the tanks," said Ryder Harman, Sales Manager at ALmix. "Pumps and piping can be heated with heat trace cables and insulated, or hot oil systems heated by scavenger heat can also be utilized in these electric applications, depending on customer preference." ALmix also offers these types of electric heat systems on portable AC tanks as well. These electric heating systems allow for a reduction in emissions from the hot oil heater burner they replace and are often simpler to run and maintain than traditional hot oil heaters.
Adjustments on the Fly
When talking about becoming more energy efficient, however, there are lots of capital investments available on the market today. Variable frequency drives (VFDs) for motors, pumps, and fans can substantially decrease electricity consumption, according to NAPA. Gencor, Astec, ALmix, and Meeker, as well as others, are able to equip their own versions of VFDs which aim to improve the overall fuel needs of the main burners, making the heating and drying of aggregates more efficient, thus resulting in a subsequent decrease in the electricity needed, because the volume of air managed by the baghouse fan is lowered. Even a small reduction in air volumes can yield significant results.
In a more detailed explanation how VFDs are utilized in today’s modern asphalt plants, the ALmix's Insignia Control System offers benefits at multiple junctions in the production process, that cumulatively provide even better efficiency and needed flexibility at the plant, allowing the plant to run efficiently at various production levels..
- Drum Mixer: Allows producers the ability to adjust the rotational speed of the drum mixer. Useful during the production of high percentage RAP mixes and Warm Mix Asphalt to allow the changing of aggregate veiling characteristics.
- Drag Conveyor: Controls the speed of the inclined drag slat conveyor allowing for a reduction in conveyor wear by running at slower speeds during slower production runs. This also maintains the level of mix in the slats, the mass, and as a result, better maintains the mix temperature.
- Baghouse Exhauster: No need for a fan damper. The baghouse fan is adjusted with the click of a button. The fan runs at the exact speed needed for desired pressure drops across the baghouse.
- Burner: The burner turbo air blower can be set to track specific process temperatures and automatically adjust output as necessary based on real-time data from the plant, including mix temperature, baghouse inlet temperature and stack temperature.
Similarly, Astec utilizes a system called V-Pack Stack Temperature Controller which enhances production efficiency by varying drum rotational speed to maintain desired stack temperature during production. Facilities using this system can enhance heat transfer with the drum and significantly increase RAP usage. Another process efficiency improvement is their StackPack Heat Exchanger for hot oil heaters that reduces fuel consumption by preheating combustion air to the burner.
In addition to their VFD systems, Gencor has a drum mixer flight design system, Converta Flight, which maximizes drying efficiency in which drum speed controls are not normally needed.
A Fix on the Mix
This is a good point to bring up the mix itself, because there are three major aspects of the asphalt mix that have been mentioned in passing thus far, but not really highlighted or explained in detail. None are revolutionary, but, perhaps one or more of them aren't being utilized to their maximum potential at your facility. As mentioned previously, there's never been a better environment to tweak, retro-fit, or improve your process. Take advantage of the government incentives while they're available, and get ahead of the curve.
The three aspects of the mix that can most effect emissions are warm (WMA) versus hot mix asphalt, virgin aggregate moisture content, and RAP. According to NAPA, WMA technologies have been demonstrated to reduce burner fuel consumption by 1,100 Btu/°F/ton, and WMA alone can account for a reduction in asphalt mix temperatures by at least 30 degrees F. Design mix temperatures can be reduced from 300 degrees F down to 260-270 degrees F, reducing fuel consumption by as much as 20%, now setting the standard for the industry. Less fuel means significant lower stack emissions of CO2, NOx and VOC.
"The Astec Green System, which mechanically foams liquid asphalt, not only enables lower fuel consumption and reduces carbon footprint, but the resulting reduced production temperature also lowers the 'blue smoke' hydrocarbon emissions," explained Trevor Wagoner, Product Manager of Sustainability for Astec Industries.
The ALmix WarmWare Warm Mix System operates in a similar fashion, and can also yield contractors additional benefits such as a reduced odors at the plant, improved workability of the mix, and extended hauling distances for mix transport.
Switching to WMA confers many other production benefits in addition to emissions improvements, according to Hunt. "It turns out to be a great tool to ensure coatings of hard to coat mix designs like large rock," they said. "The Gencor Ultrafoam process is a tool to improve workability of high RAP mixes, that are considered to be 'hard mixes' at normal mix design temperatures or reduced temperature mixes. Plant blue smoke emissions are reduced and it highly reduces laydown emissions on the road, while improving worker comfort and safety.
The Not-So-Secret Sauce
Perhaps, one of the most surprising aspects of energy consumption and, thus, overall emissions control is the proper storage and care of virgin aggregates and RAP. In fact, it may drive the largest benefit to cost ratio. For example, the June 2022 study by NAPA reported that for every 1% reduction in aggregate moisture, the average energy intensity for asphalt mix production was lessened by 27,100 BTU/ton.
Drive by any asphalt plant facility and you are likely to see huge piles of RAP stored wherever they can fit. More attention should be paid to these details
"One of the best 'technologies' that is available to an asphalt producer is good stockpile management," Said Wagoner. "Reducing the moisture in the aggregates feeding an asphalt plant can result in significant improvements in the heating energy required from the burner."
Common ways to aid in the reduction of aggregate moisture is to slope the grade and include a drain under the storage piles, lay pavement under them, and/or build structures that cover or house them. When this is combined with some of the other process related controls like we've discussed can mean a reduction in necessary heat by at least 20%.
Gencor takes this one step further with the Ultradrum Advanced Rap Entry technology. "It utilizes the convective heat of the combustion zone to preheat and advance the release of internal moisture in the recycled pavement," said Hunt, "This release of moisture in the RAP offers an increase in energy efficiency, by allowing the RAP material to move through the combustion zone absorbing conductive, radiant and convective energy while controlling and preventing overheating. It permits 50% RAP capability with lower aggregate temperatures."
The Other Fugitives
It might feel like a long time ago, but at the start we discussed the difference between process and fugitive emissions at asphalt plants. Obviously, the process emissions are a varied and the ways to reduce them are numerous and growing. Technology continues to evolve, and need further innovation to achieve the goals set by the industry for net zero carbon emissions. But we can't ignore the other side of the coin, because there are plenty of improvements available for you plant today.
"Dust and fine particulate matter emissions have been controlled by baghouses for years," said Harman. "The ALmix baghouses use a reverse air rotary cleaner to clean the bags during production, which allows for gentle cleaning of the bags without the need for compressed air. We offer nearly limitless dust metering, storage, and return options to help contractors manage different volumes and types of dust at the plant. Different states have different requirements for dust handling, but the overall goal here is to keep the dust and fine particulate matter out of the air around the plant and reuse as much as possible in mix products."
In parallel with that, Gencor has the Ultraflo baghouse filtration system meets and beats some of the most strict and rigid dust collection rules and requirements for PM 2.5 and PM 10 particulate emissions.
What's Still on the Table
The research shows that, even with all of the technology, planning and implementation discussed here, there's still a lot to overcome. The vast majority of emissions related to the industry happen before or after the production process, so that discussion will have to wait for another time.
However, it is worth mentioning that according to NAPA's report, "From a raw materials perspective, asphalt binder production is the most significant contributor of upstream GHG emissions in an asphalt mixture, comprising 94% of the emissions associated with raw materials (A1) and 53% of cradle-to-gate emissions."
In addition to this, 63% of GHG emissons associated with the binder production come from the extraction of crude oil. At the heart of the matter, once again, the reliance on fossil fuels continues to anchor the industry, and our whole industrial economy to an undesirable ecological outcome. The asphalt industry, NAPA, and its goals are admirable and act as a leader for others to follow. With the vast majority of America's roadways being paved in asphalt, the hope is that will equal an influence to drive continued sustainable innovation.