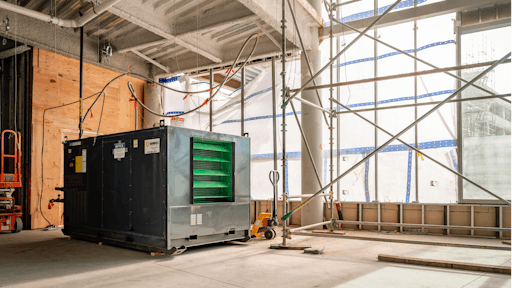
heater, providing high CFM to a large hospital build in a metro area.
As the construction industry gears up for the winter months, the importance of climate control on construction sites becomes increasingly evident. Properly maintaining the climate on a jobsite can be a game-changer for construction site managers, ensuring the project remains on schedule, stays within budget, and meets the quality standards for building owners. Climate control plays a critical role on construction sites, and this article will explore the consequences of neglecting it and the solutions available to safeguard project success.
One of the most significant consequences of failing to maintain the proper climate on a construction site is the risk of permanent finishes and materials swelling, shrinking, or cracking. When construction materials are exposed to unfavorable conditions, they can experience significant damage, requiring removal and reinstallation. This leads to additional labor and material costs, potentially triggering liquidated damages and warranty noncompliance. To avoid these costly pitfalls, acclimatizing construction site materials to the specified climate, temperature, and relative humidity requirements is paramount.
Ensuring Proper Climate Control in Each Phase of Construction
Temporary heating plays a pivotal role in maintaining the optimal climate on a construction site. Delays caused by improper climate temperatures for building materials can significantly impact a project. Superintendents must adhere to a tight schedule to complete the project, ensuring trade contractors can effectively perform their tasks when multiple predecessors need to happen.
All phases of construction require certain temperature and humidity levels to ensure materials are climatized to the space. This includes most prefabricated materials brought on the jobsite and the installation of those finishes.
Construction Site Considerations
Different materials and phases of construction demand distinct climate control solutions. Construction site managers need to consider these solutions throughout every stage of construction to avoid costly setbacks. Temporary climate control solutions need to adhere to the specifications of each of the finishing materials.
For instance, flooring materials, interior finish work, and millwork all require specific temperature and relative humidity levels for correct installation. Failure to follow these guidelines can result in issues such as drywall curing problems, tape not adhering properly or at all, cracking, or swelling, which would mean the materials should be removed and reinstalled, further delaying the project. Laying down glue for high-end flooring provides another example highlighting the importance of climate control. The glue will have a Material Safety Data Sheet (MSDS) that outlines installation instructions, ideal temperatures to store the product, and relative humidity levels for installation. Many different factors contribute to the successful installation of building materials.
Environmental considerations are becoming increasingly relevant, especially as more environmentally friendly building products and practices are adopted. These products, often water-based rather than solvent-based, are more sensitive to temperature changes and drying rates can be affected.
To further emphasize the relevance of climate control, consider materials such as gypcrete, drywall, stucco, or high-end millwork finishes. As construction progresses and the building nears completion, temporary climate control becomes even more vital. Interior and exterior materials need to be climatized well in advance of installation to prevent swelling, shrinking, or cracking, reducing both costs and environmental impact.
Types of Construction Site Solutions
Several types of temporary heating systems are available for construction site use, each with advantages and
drawbacks. These include:
- Indirect-fired heaters
- Direct-fired make-up air heaters
- Electric heaters
- Direct-fired recirculating heaters
- Radiant heaters (which are crucial for exterior work)
- Steam heaters
An indirect-fired heater is a desirable option for many contractors, especially in high-end or environmentally conscious projects such as a medical building or a green environmental/ESG building. These heaters offer clean, dry heat without volatile organic compounds, making them a safe, efficient, and clean temporary heating solution. However, they can be more costly and less fuel efficient. On the other hand, a direct-fired make-up air heater is economical and nearly 100% efficient and utilizes fresh outside air to reduce VOCs and CO2 buildup inside the building.
A direct-fired recirculating heater can be used early in a project for tasks such as curing an elevated deck pour, fireproofing, or freeze protection. In early phases of construction, buildings are typically not well sealed yet. This prevents the buildup of combustion byproducts from these styles of heaters. This is an economical option with a smaller footprint, taking up less space on the floor, and is extremely fuel efficient.
Costs associated with temporary heating equipment typically break down into 20% for equipment rental and 80% for fuel costs. Fuel costs can vary based on regulations, regional considerations, and code requirements. Some downtown or metro areas restrict certain fuel sources, such as natural gas or propane, and often utilize diesel-fired or electric options.
From a fire protection standpoint, the choice of fuel source is critical. The focus remains on the general contractor, their budget, and the timeline at hand. Making informed decisions about fuel sources helps balance budget constraints with project safety and efficiency.
Why Rent?
Renting climate control solutions offers a hassle-free and cost-effective approach. A rental company provides valuable support in defining project scope, assessing equipment requirements, and ensuring proper equipment maintenance, ultimately saving time and money. Rental companies, like Sunbelt Rentals, offer 24/7 availability and emergency support to keep customers operational and can quickly replace malfunctioning equipment, ensuring the project stays on schedule and within budget.
The value of partnering with a good rental company comes from the availability of experts assisting contractors in developing a fuel-efficient, safe, and economical solution with the right equipment to meet needs.
Innovative climate control solutions are a linchpin in ensuring construction projects proceed smoothly and meet the expectations of all stakeholders. These solutions not only benefit the construction site but also the end user. They provide peace of mind by reducing callbacks and ensuring that projects stay within specified parameters. As the construction industry continues to evolve and embrace environmentally friendly practices, the importance of climate control becomes increasingly evident. To meet quality standards, adhere to project timelines, and reduce costs, construction sites must prioritize climate control solutions throughout every phase of the building process.