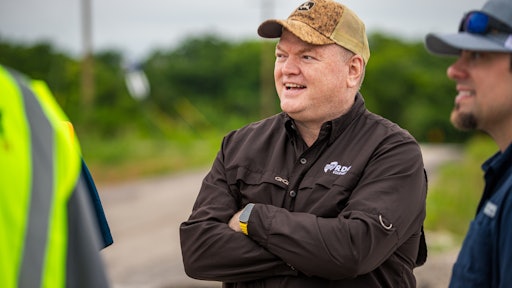
To build a strong home, you need a solid foundation. And you need a solid, experienced team to prepare the ground before building. That’s where teams like Hamett Excavation are essential.
Earlier this year, Hammett’s Project Manager Darin Stroud and I discussed how the Hammett team integrated GPS technology and machine control into their fleet. The company’s decision to adopt these new technologies proved to be a defining moment for the whole team in that it catalyzed the team’s proficiency to complete projects, even while dealing with a challenging skilled labor market.Hammett Project Manager David Stroud.RDO Equipment
Stroud explained they started using GPS technology more than 20 years ago when RDO Equipment Co. team members encouraged Harry Hammett, the company's founder, to try something new.
“Harry was one of the first ones to demo the GPS technology on his dozer,” Stroud said. “Once he saw how the GPS and machine control systems displayed how deep to cut in real-time, he told the RDO technicians to leave it on the machine.”
Before this technology, however, operators like Harry had to manually check grade and position machinery themselves—a less accurate, more time-consuming process with higher safety risks. Technology on dozers like Harry’s has evolved to automated machine control, which moves the blade to grade by talking to the machine’s hydraulics.
Harry’s son, Gaylon, now runs Hammett Excavation, which has grown from five to more than 300 team members during its 60 years in business. According to Stroud, integrating Hammett’s equipment fleet with technology increased their team’s capacity to take on more complex projects. Their business growth created new opportunities for team members and allowed managers to hire people to fill positions others had outgrown as their technology skills advanced.
“I don't think there's any way that we would be this big and be able to manage the work and the business without this technology,” Stroud said. “Our in-house staff does everything from start to finish.”
In just the first six months after onboarding GPS technology, Hammett’s efficiency increased by 70%. Hammett’s increased productivity has kept them competitive and profitable.Crews will condition approximately 10 feet more of soil, then dig 10 feet below the final grade (depth) of a house pad–the level at which the foundation will be poured for a home to be built.RDO Equipment
In recent years, Topcon GPS technology and RDO Equipment Co.’s real-time machine monitoring service created an effective solution to labor challenges. A recent study by the Associated General Contractors of America indicates that 88% of construction firms with open positions are having trouble finding the right person for the job.
According to Stroud, who still considers himself an operator above all else, jobsites are a mix of older, more experienced operators and younger ones who have just started working on excavation sites. While the saying "heavy equipment operators never retire" holds true, many of the more experienced ones are working fewer hours, either to spend time with family or because they have transitioned into a new role, like Stroud. This means that newer operators miss out on learning from the more experienced ones when they are not around as much. The Association of Equipment Dealers' labor report first identified this knowledge loss challenge. To combat it, the Hammett team is using GPS technology to maintain consistency and accuracy for precise grading.
“Both age groups get set up and going quickly,” he said. “Old school and new school operators alike say the technology can be intimidating if you don’t know anything about it, but overall, it simplifies everything.”
Stroud said operators don’t have to be “computer savvy," as he’s not a tech guy. As an “old school” operator with two kids, ages 18 and 21, Stroud said he and other older operators sometimes miss the old way of doing things, but this new way has increased their productivity and made things easier for them.According to Stroud, who still considers himself an operator above all else, jobsites are a mix of older, more experienced operators and younger ones who have just started working on excavation sites.RDO Equipment
“I’m a dozer operator, but now, with this technology, I create and build out some of our survey models,” he said. “It was easy to learn after RDO (team members) came out and provided a couple of hours of training. It does everything itself.”
On this jobsite, Topcon's GPS technology decreased the time it took to survey the large area and develop his grade plan, Stroud said. Before stepping onto this jobsite, Stroud worked with a geo-technician who performs soil tests to define the exact amount of compaction needed based on moisture and other environmental factors.
Through these tests, the geo-technician and Stroud will determine the soil conditioning process—a vital step to creating a structural sound housing pad. Soil moisture conditioning is a process to prepare the soil for building by reducing or increasing soil moisture levels. When levels are too high or too low, it will lead to unstable ground that can damage a home’s foundation. Too much moisture can cause swelling, problems with over-compaction, and unsuitable bearing capacity. When moisture levels are too low, it can cause sediments to shrink, creating voids in the soil, leading to foundation failure.
Once completed, Stroud set a predetermined depth for his team to dig based on the approved compaction. Then, they bring this plan to a larger group along with Hammett’s QA/QC Framework, a simple document Stroud prepares to explain what his team will do to ensure quality and efficiency despite any other challenge. After the project plan is approved, Stroud works with his team to input specifications to create computer-aided design (CAD) files to house 3D and 2D models for machine control software to follow.
Crews will condition approximately 10 feet more of soil, then dig 10 feet below the final grade (depth) of a house pad–the level at which the foundation will be poured for a home to be built.RDO Equipment
Stroud can check compaction in real-time to stay on schedule by monitoring Hammett’s equipment working, including John Deere 850 dozers, excavators, and articulated dump trucks through Topcon machine control and monitoring software. Earthmoving machines like dozers and excavators with Topcon receive signals from these systems and compare them to the model of the proposed plans. Topcon combines the Global Navigation Satellite System (GNSS) and GPS to maximize equipment connectivity to the in cab displays and software to record data. This process allows the equipment to determine exactly where and how to grade the terrain.
“It’s so much easier with Topcon’s GPS technology,” Stroud said. “Before we had this technology, we would have to wait up to a week after the project plan was approved to start because surveyors needed to place stakes. And while working the job, our operators would have to work around surveyors walking around to check grades.”
Newly-hired excavator and dozer operators feel more confident with Topcon on their machines as it safeguards against potential hazards and helps them achieve the right grade based on Stroud’s compaction plan. Even experienced operators say seeing their machines’ earth-moving progress increases their job satisfaction.Earthmoving machines like dozers and excavators with Topcon receive signals from these systems and compare them to the model of the proposed plans.RDO Equipment
Stroud said even though they had to invest upfront in this type of technology, it has paid off exponentially as it speeds up production. And 20 years ago, when Hammett found an equipment and technology service provider with similar values, the Hammett Excavation team took advantage of technology’s catalytic effects.
“As long you have people that are willing and have the drive to learn technology, it's not complicated,” Stroud said.
Stroud said he and all his operator friends agree: The chance to build new things and see how we can improve them and make them better makes all their hard work worthwhile.
“I love driving with my wife, and seeing all the areas we excavated and other things we were able to help build,” he said. “It gives me a lot of drive and hope for the future.”
Check out this video to see some of the equipment in action.