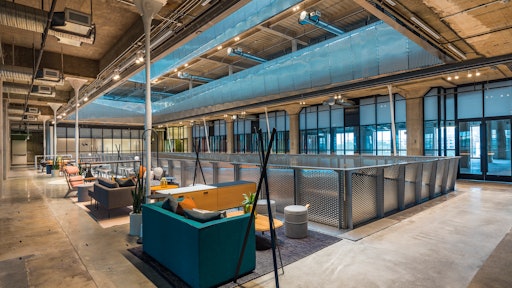
Constructed in 1939, with additional modifications completed in the 1960s, a three-story concrete building in Houston's Midtown was not structurally designed for expansion. In 2017, Rice Management Company, stewards of the Rice University endowment, purchased the remaining years of a 99-year lease of the building - what was a former Sears department store.
During the proposal phase, Rice Management Company decided to proceed with the steel-framed vertical expansion of two stories as well as a horizontal expansion of the existing concrete structure on the lower three levels. This repurposed structure would be known as The Ion. The final solution involved a more significant extent of demolition both on the building exterior and interior.
Repurposing existing structures, especially those made of concrete, has proven popular of late as a means to cost-effectively develop creative space, shorten construction schedules, and reduce the impact on the environment. While the former two are well-known strategies, the latter typically involves the reduction of embodied carbon. Emissions associated with extracting and installing new materials are reduced as well as the amount of waste produced during demolition.
The goal was to repurpose the existing structure into a collaborative technology innovation hub for Houston’s entrepreneurial, corporate, and academic communities.
However, repurposing the stand-alone “concrete box” while maintaining its original character presented numerous engineering challenges. “The original building was a dark box,” says Dennis Wittry, managing principal at Walter P Moore. “To make the building inviting to commercial tenants, bringing daylight into the space was critical. The original scope of work anticipated using punched windows to bring in nominal daylight into the space while minimizing demolition of the exterior concrete walls that were serving as the primarily lateral system for the building.”
Rice Management hired Walter P Moore as the structural engineer of record, three design and architectural firms—James Carpenter Design Associates, SHoP Architects, and Gensler—while Gilbane served as the general contractor and Encore Concrete Construction was the concrete contractor.
G. Lyon Photography
Adaptive Reuse
The design intent to repurpose the building was to strengthen or adapt the structures in ways that made it look like it was part of the original construction. Therefore, the horizontal and vertical expansions would serve different roles once the building was repurposed. The horizontal concrete-related expansion was a completion of the historic original structure. New openings in the existing structure were framed out by creating new concrete beams within the existing slab, rather than introducing new steel beams. This created an uncluttered look that complemented the original structure.
“Conceptually and practically, the horizontal expansion made most design sense in concrete, the system of the original structure,” says Anneli Rice, project director at SHoP Architects.
As for the two-story vertical expansion of the structure, the use of steel framing minimized the increase in load on the existing structure. To support the added load required strengthening of the existing spread footing foundations. However, the existing columns did not require strengthening. Walter P Moore worked with a geotechnical engineer to determine that the existing soil was adequate to support a higher pressure than the foundations were originally designed.
“This limited the need to expand the spread footings, but required their strengthening,” Wittry says. “To strengthen the spread footings, the space between the top of footing and top of basement level slab on grade was utilized. We drilled and epoxied dowels into the existing top of footing to compositely connect it to a new thickened section.”
G. Lyon Photography
Meanwhile, the framing for the existing roof at the third level did not have sufficient load capacity to serve as an occupied floor. As a result, new steel overbuild framing was spanned between the existing columns. The new framing did not require fireproofing due to the existing concrete roof slab directly below.
In order to introduce daylight into the structure, multi-story openings were cut into the concrete walls for a new curtainwall. Furthermore, a stunning 26 by 92 ft light well was constructed in the center of the structure. Designed by James Carpenter Design Associates, the light well makes the adaptation of the large floorplates into workspaces possible, providing critical access to daylight and the outdoors.
“We wanted the center of the building to come alive with light and activity, and this central volume created a canvas for these spaces to connect to the sky,” says Joseph Welker, studio director at James Carpenter Design Associates.
To create the light well, four concrete columns were demolished in the middle of the structure as well as a large area of three existing concrete slabs. The light well cut an angled slice out of the building to follow the path of reflected light from a skylight above. However, it also left a cantilevering concrete slab condition of varying lengths at each level.
“To avoid cracking of the existing slabs, they were ‘overcut’ to the column edge to allow distribution of reinforcement based on the new support conditions,” Wittry says. “A construction sequence was developed for the construction of the light well to avoid overloading existing elements.”
The remaining concrete slabs were hung at each level via three-inch diameter hanger rods from new concrete transfer girders that were poured over the existing roof within the depth of the steel overbuild. The original plan was to extend the hanger rods to the new roof and support them from the steel.
However, Walter P Moore designed them to stop at the existing roof level, which freed the two new upper floors from visual obstructions in the light well.
G. Lyon Photography
Structural Concrete
Rice Management Company preferred to keep the existing concrete structural components as well as the retrofitted structural concrete exposed throughout the building as part of The Ion’s design. This included all columns and floor framing.
Each retrofitted area in The Ion includes existing exposed 9.5-in. concrete flat slab structure with 4.5-in. drop panels at each column. Walter P Moore’s structural design widened existing concrete beams or cast new 4.5-in. deep beam stems doweled into the soffit of the existing slab where existing openings needed to be infilled or existing beams strengthened. By matching the depth of these beams to the existing drop panels, the beams appear as part of the original construction.
Due to the extensive new openings for curtain wall in the exterior concrete walls and the additional wind exposure due to the two-story vertical expansion, new concrete shear walls were introduced at the concrete floors of the building near the stair and elevator cores. Steel braced frames were used over top of the concrete shear walls, at the vertically expanded floor levels.
The beams and shear walls were constructed using self-consolidating concrete pumped through new holes created in the existing slabs.
“Self-consolidating concrete was used in the concrete beams that were added to the existing structure as well as in the new shear walls,” says Aaron Smith, project manager at Encore Concrete Construction. “In an existing structure, when placing new concrete beams underneath an existing floor plate, standard concrete with a 5-in. slump could not be placed from above. Self-consolidating concrete was used as a means to ensure quality.”
To pour the self-consolidating concrete, large core holes were placed roughly 10-ft apart through the existing slab and it was poured from the top. Smaller holes approximately 0.5-in. in diameter were drilled approximately 2 ft. apart between the larger holes so air could escape and not become trapped between the new self-consolidating concrete and the existing slab and beams.
G. Lyon Photography
Exterior Upgrades
The Ion seamlessly integrated the original art deco style of the structure, particularly at the ground-level storefront façade on the north side. The addition of the glass curtainwall on the building’s south end, and introduction of daylight through large openings in the east and west concrete exterior walls connect the open interior to the surrounding streetscape. Large, multistory exterior openings were added for new windows in the concrete walls, as well as the two-story vertical expansion.
The Ion was designed to maintain the aesthetic of the northwest and northeast storefront corners, while vertically extending the curtainwall in the corners by 15 ft. It was a challenge for the building team to achieve this while concurrently maintaining the stability of the areas, which supported the existing concrete façade and concrete roof framing.
“Maintaining the storefront aesthetic was extremely difficult from a construction standpoint,” says Taliah McGowan, senior project manager at Gilbane Building Company. “To install the curtainwall and maintain the corner aesthetic, the existing concrete walls needed to be demolished and opened up.”
This required the existing concrete structure to be reinforced with a new steel structure, but the reshoring required to carry the existing roof beams—weighing upwards of 100,000 lbs. that were previously supported by the concrete to be demolished—impeded the placement of the new structure, according to McGowan.
Shoring was installed in the center portion of the wall so the outer locations could be demolished. Once this was complete, a portion of the new steel framing was installed to support the wall. After the center shoring was removed, the remainder of the demolition and steel installation occurred.
Final Transformation
G. Lyon Photography
Repurposing of the 1939 concrete structure involved demolition of existing stairs, escalator, center columns, and floor slab, and cutting new openings in the exterior walls and floor slabs for new stairs and elevators, while infilling existing stair and elevator openings. Transforming the original department store in lieu of its complete demolition and new build minimized embodied carbon, provided a platform for innovative design and engineering, and created a truly unique space to inspire “outside the concrete box” innovations for many years to come.
About the author
Rachel Calafell, PE, is a principal and project manager at Walter P Moore. She can be reached at [email protected].