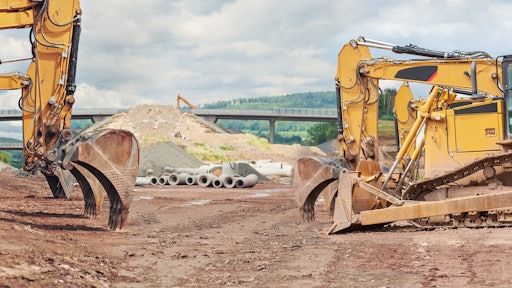
To operate effectively, most construction businesses regularly review key aspects of their operation to identify where efficiencies can be made. This often falls to equipment operators or maintenance technicians due to the technical complexity of most operations. However, rather than view each area in isolation, it’s considered best practice to take a holistic approach.
One key consideration should always be the engine oil. There are a multitude of factors that can impact fuel economy and overall efficiency, such as the equipment’s operating environment and average load.
For engine efficiency and fuel economy, selecting the correct engine oil is fundamental in helping to reduce fuel consumption and carbon emissions, as well as reducing unplanned maintenance.
Engine oils play a vital role in the protection of engine components by minimizing metal-to-metal contact between moving components while reducing pumping and rotational losses. This helps prevent wear that can result in unplanned maintenance and downtime, while improving engine performance and, depending on the oil used, fuel economy.
When selecting a heavy-duty engine oil, there are some essential considerations that equipment managers and operators should be taking:
1. Seek Original Equipment Manufacturer (OEM) Advice
The process should always start with consulting the Original Equipment Manufacturer (OEM) manual for advice on oil selection. If further advice is needed, the OEM can be contacted directly for information and guidance based on the engine’s specification.
2. Consider the Operating Conditions
The environment and operating conditions of the engine should be the next consideration when selecting any heavy-duty engine oil.
The temperature range in which lubricants can perform optimally is denoted by its SAE grade, which is a measure of the oil’s viscosity. The viscosity of the oil dictates its ability to flow and move around the engine to lubricate its inner workings.
In cold conditions, if the oil’s viscosity is too high, it may resist movement and delay the lubrication of vital engine components, which can result in increased engine wear. In these conditions, lower viscosity engine oils, such as SAE 5W-40 or 0W-40, are more suitable as they allow the oil to flow better at lower ambient temperatures.
When operating in the hot summer months, construction equipment can get very hot, so to effectively deal with these temperatures, an oil with a viscosity of SAE 10W-30 or 15W-40 may be more suitable. These oil grades resist the breakdown associated with higher temperatures to allow adequate flow and lubrication of critical engine components.
3. Compare Synthetic vs. Non-synthetic Engine Oils
Fully synthetic and synthetic blend engine oils offer better stability than conventional oils and improved performance in varied weather conditions. Synthetic blends can also enhance engine protection and performance in certain operating conditions.
Fully synthetic oils are formulated with synthetic base stocks and are blended with high quality and performance-enhancing additives. These typically provide a greater level of performance than both conventional and synthetic blend lubricants due to the superior formulation components.
4. Request Proof of Performance
Oils must maintain industry licenses such as API CK-4 and FA-4, so it’s important that proof of this and any OEM approvals can be provided. Testimonials and case studies are also valuable examples of real-world use, especially when highly relevant to your application or business. The testing carried out by a lubricant manufacturer is also important and should be considered when selecting your oil.
5. Seek Expert Lubricant Manufacturer Support
The final step to making a fully-informed lubricant choice is to seek expert support and guidance from a reputable lubricant manufacturer. Expert lubricant manufacturers have experienced lubricant technical advisors who can provide advice based on specific requirements, and they also invest significantly in comprehensive testing of products so they can provide informed and invaluable lubricant recommendations for business’ equipment and its operational needs.
Looking Ahead
While these steps will help you to make the best lubricant decisions for your equipment, it is equally important to be mindful of future trends and upcoming regulations, so that you can stay one step ahead of the game.
The development and introduction of API PC-12, the next proposed lubricant category, will likely further accelerate the transition to lower viscosity solutions, helping to reduce carbon emissions and improve fuel economy. The new specification is being developed to help OEMs meet the latest greenhouse gas and fuel mileage regulations issued by the U.S. Environmental Protection Agency (EPA) and the California Air Resources Board (CARB).
While the details of the new specification are yet to be finalized, PC-12 lubricants will be formulated to meet the performance needs of the latest engine and emissions systems technologies. This means that wear protection will be even more important, as will oxidation control, due to engines working harder with increased operating temperatures to help meet new regulation guidelines.
The new category is expected to have two subcategories, including one which takes advantage of lower high temperature high shear (HTHS) oil viscosity (similar to API FA-4). This category will be designed for specific OEM hardware architecture and offer even lighter grades of lubricants (possibly even SAE 0W-20s) that provide wear protection and durability, while further reducing viscous drag to ultimately improve fuel economy.
Because of this, new engine lubricants will undergo rigorous testing, similar to their predecessors, to provide reassurance that high-performance qualities have not compromised protection of the engine’s componentry. This will likely see these lubricant categories face new tests developed in line with the latest engine architecture.
Performance and regulatory demands will continue the trend towards lower viscosity solutions. Equipment operators should embrace this change, along with the fuel economy benefits that it will bring them.
For businesses on a journey toward improved efficiency, the right choice of lubricant can improve fuel economy, engine performance and help reduce unplanned downtime. However, selecting the best heavy-duty engine oil for your equipment can be a complex task that requires expert insight and experience, especially given the upcoming category change. Seeking professional advice throughout the process can help you make the right decisions, including selecting the most appropriate engine oil for your equipment, to maintain proper lubrication and improve equipment performance.