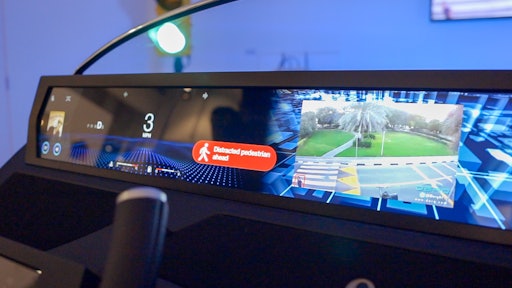
Roads are so intrinsic to the American way of life that our vernacular comprises thousands of road-referencing phrases, idioms, musical lyrics and jokes:
“Every day is a winding road.” – Sheryl Crowe
“The road to hell is paved with good intentions.”
And one of my personal favorites:
“Take the high road.”
Roads, streets, paths, trails and tracks all evoke a sense of progress, and that forward movement can be wandering or purposeful. Whether emphasizing the journey of life or a path toward a noble goal or inevitable downfall, roads are a vital part of both the American infrastructure and vocabulary. It’s no wonder the need for roadbuilding and connectivity go hand in hand. However, since we’re reflecting on word choice and vocabulary, the word “connectivity” begs further inquiry.
What is Connectivity?
The term “connectivity” can refer to broadband internet and its vital important to the infrastructure of the United States, as well as connected construction jobsites via the aforementioned broadband internet, smart roads with LiDAR cameras, roadbuilding equipment with updated sensors to determine and guide proper compaction pressure and techniques, and machine manufacturing processes that reduce carbon footprints for maximum efficiency and productivity. These are all key pieces of the puzzle that add up to an overarching, desirable image—a well-connected map of maintained roads and transportation solutions in the United States.
With advancements in AI and 5G network connectivity, smart-road infrastructure technology offers the promise of being added to many different roads, bridges, and other transit systems across the U.S., in hopes of improving real-time traffic analytics and tackling the most challenging road safety and traffic management problems, Georges Auode, CEO and co-founder of Derq, recently wrote in an expert column that appeared in the August 2022 issue of Equipment Today.
Road connectivity extends to the machinery used to build it, as well. All integrations and equipment – from wireless to wired to steel – must work together to make U.S. roads the best they can be in the coming years. There is no royal road to learning.
Connectivity a Top Trend for the Construction Industry’s Future
AI and connectivity, along with renewable energy and alternative fuels, will dramatically impact the construction jobsite in the next 10 years, according to a recent whitepaper published by the Association of Equipment Manufacturers.
As jobsites become more connected, contractors and construction companies gather thousands of data points for later use. These data points could be monetized and shared with others outside the industry for even greater good and connectivity, according to AEM. From weather mapping with cloud-based systems to wearables detecting when people take falls, the bright future of construction site technology that AEM details in its latest whitepaper suggests more than just contractors and operators can benefit from data collection and interconnectivity.
Simply put, due to more advanced 5G networks and cloud systems, connectivity on the jobsite will improve significantly in the next decade, according to AEM’s data and projections. Better equipment tracking will allow real-time visibility into productivity and maintenance on a jobsite, so operators and contractors can make sure they queue properly and have the most efficient job flow they can, said Ray Gallant, Volvo vice president of product management and productivity region, at an AEM webinar in September 2022.
This increased connectivity has significant implications for the future of roadbuilding, from possible, monetizable data point collection to vigilant planning of safer roads. Let’s get this show on the road.
While drivers are well-versed in traffic signals and signs alerting them to when they should or should not drive their vehicle, AVs need different alerts in the form of radio or cellular network signals.Derq
Smart Roads
A significant part of Pres. Joe Biden's infrastructure plan, the Infrastructure Investment and Jobs Act (IIJA) deals with evolving transportation and roadways with smart infrastructure, which includes Vision Zero. Vision Zero is one of the newer strategies looking to eliminate deaths and severe injuries due to road traffic and unsafe infrastructure. First successfully implemented in parts of Europe, the strategy recently gained traction in North American cities.
Collaborations are integral between traffic planners, engineers, and policy makers alike in the Vision Zero strategy. Committing to Vision Zero means unlearning old ways of the roads and making room for new strategies to better the transportation infrastructure, according to Auode. This means that system designers and policy makers are expected to improve the roadway environment and policies in addition to other related systems in order to dramatically lessen the severity of crashes.
Advanced technologies including video analytics solutions use artificial intelligence (AI) and machine learning approaches to analyze large quantities of video streams in real-time to then provide actionable insights on complex traffic situations including road hazards, congestion and traffic collisions. For example, companies like Waycare, Derq and Applied Information provide software that analyzes behavioral patterns of vehicles, pedestrians, and traffic flows from existing traffic infrastructure in real-time to identify and predict potential road incidents. These advanced video analytics can then activate a pedestrian blinking sign to alert a distracted driver from colliding with a pedestrian about to cross the road. They can also alert a city operator so emergency responders can be dispatched to the location of the incident if a collision is detected. Furthermore, real-time AI analytics provide additional context in the form of incident identification, near-miss heatmaps and accurate traffic counts to traffic engineers and operators, which ultimately allows them to better understand traffic patterns and proactively improve the safety of roads.
In Miami-Dade County, the autonomous vehicle research team at Ford is exploring how emerging technology from smart infrastructure can provide additional information to an autonomous vehicle (AV) before it even arrives at an intersection, Auode wrote in a 2021 ForConstructionPros.com column. While many cities have different types of traffic signals – horizontal, vertical, posted in the corner of the intersection as opposed to in the middle of the intersection – AI algorithms unite smart infrastructure with AVs, which enable the launch of these vehicles in new locations much faster. In Las Vegas, Motional’s driverless vehicles are partnering with Derq to test how driverless technology reacts when given an even broader perspective than it already has. The collaboration has created a “bird’s-eye view” for the AVs at some of the most highly-trafficked intersections in the city.
The focus on technology should not be isolated to the car itself, but also in upgrading the actual road infrastructure, according to Auode. State-of-the-art artificial intelligence (AI) to advance smart infrastructure will not only help driverless vehicles understand the roads better, but also improve overall road safety as AVs are not equipped to see around corners or other impediments. With smart infrastructure now being introduced by AI startup companies such as Derq, having those “eyes” outside of the vehicle also allows for greater visibility overall – making the ride not only safer, but more comfortable and with even better performance. This will also result in less-congested roads. For an average U.S. citizen, congestion costs 99 hours of their time and $1,377 each year. Smart infrastructure can prevent traffic backups by adjusting traffic signals when needed.
While some self-driving companies currently don’t rely on smart infrastructure, the AV industry is realizing that it’s an important piece of the puzzle when it comes to accelerating the ability to deploy more AV routes in different cities and countries. In addition, transportation systems can’t achieve safety without smart infrastructure. The need for innovative technology on the roads is growing. The U.S. Secretary of Transportation, Pete Buttigieg, has even stressed the importance of building better infrastructure as well as technology for self-driving cars.
The incorporation of AI and video analytics in smart roads will further the development of the technology of driverless vehicles. These innovations will also revolutionize the safety, comfort and performance of not only the autonomous vehicles, but also the overall transportation ecosystem. Now, where the rubber meets the road—ensuring the roads themselves get built safely and efficiently with high-tech equipment and connected jobsites.
Smarter Equipment and Jobsites
In North America, competitive bidding of projects is becoming increasingly dependent on being able to guarantee a road surface meets stringent specifications for smoothness or compaction, and contractors are further incentivized by bonuses for meeting these specs—and doing so in as little time as possible. In this way, the market itself is pushing the adoption of technologies like intelligent compaction, digital jobsites, and networked equipment and employees.
Another market pressure is the labor shortage. Contractors are attempting to meet these specs and earn these bonuses with a smaller available workforce to pick from. For some crews these digital efficiencies become the difference between being able to get a job done or not.
And though some North American contractors are not eager to adopt electric machines yet, fuel consumption is still top of mind. There is no better illustration of the adage, “Time is money,” than a roller having to do more passes than is necessary.
Making less roller passes is not the only way to save fuel, and BOMAG is aware of this fact. After all, the company does have two small battery-electric rollers in the lineup and offers the BW 174 hybrid roller. When you become more efficient in your process, you use less fuel; there is much efficiency to be gained.
In fact, BOMAG pavers vice president and current North American head Marco Faulhaber said he has seen a trend of compactor operators who over-compact out of fear of not compacting the surface enough. For some contractors, the rate of over-compaction could be as high as 50%.
“Imagine if I could cut my fuel consumption on a compactor by 50% just by making sure that my operator knows exactly when to stop,” Faulhaber said.
In that way, Faulhaber said the machine and the efficiencies BOMAG has created on the machine itself is a bridge to finding more efficiencies through jobsite connectivity and broader networking throughout the operation. Implementing technology to make road construction work more efficient and accurate is nothing new to BOMAG. The company introduced its intelligent compaction solution Asphalt Manager all the way back in 2001.
“So far this work has been focused mostly on the machine. The next step of course, is to start linking machines and make sure that the total outcome is what you need,” Faulhaber said. “Those digital solutions when you start linking the jobsite together improves the overall efficiency of the jobsite, the quality of the job that is being built, and improves the efficiency greatly.”
When machine control technology is paired with a digital jobsite and a networking of all the processes, “I control my quality throughout the job,” Faulhaber said. That line of thinking is fueling the questions and problems the company is trying to answer and solve with the networking technology it is currently developing.
“So, how do you create this level of confidence, so that the contractor knows that his crew is up for any job, no matter what happens? What kind of support can the machine manufacturer provide the machine application experts with, beyond the digital job tools we have and easy-to-operate machines, so that at the end, you get the best out of the road that you possibly can?” Faulhaber asked rhetorically.
Building upon the company’s machine control offerings is the chosen path. The company is exploring autonomous roller technology and has displayed cab-less rollers at a few trade shows. But at bauma 2022 the real focus was on networking people and machines.
At its booth in Munich, BOMAG had a whole room dedicated to the digital road jobsite of the near-future, complete with scale models and lots of displays. In that room, the company brought in scores of customers to discuss what they are seeing on their jobsites and to see how BOMAG’s vision for connected jobsites matches up.
BOMAG’s vision of connectivity includes ensuring that the key jobsite data is dispersed throughout the jobsite. Rather than one supervisor managing a dashboard of all the various digital touch points, BOMAG wants to equip every operator, driver and employee with that dashboard via a tablet, smartphone or their in-cab display. The idea is that if you arm each and every individual with the information they need to do the best job they can, the strength and efficiency of the jobsite as a whole will increase. In short, the sum will be greater than its parts, but a sum dependent on those parts nonetheless.
If the road, street or adjacent sidewalk is made out of concrete rather than asphalt, connected jobsites and equipment also exist to aid in the efficient and safe production of concrete pathways.
Soracom, Inc., a global provider of advanced IoT connectivity, has partnered with EXACT Technology Corp., a concrete monitoring technology company, to help build future infrastructure projects.
The first seven days of the concrete curing process are critical. The temperature of the concrete needs to be maintained consistently throughout the weeklong period, otherwise it has the potential to crack, letting in salt and water, and compromising the longevity of the concrete. EXACT’s technology checks for temperature fluctuations in real time, collecting data and alerting project managers via Soracom’s connectivity solutions.
Access to this real-time data allows project managers to adjust accordingly by heating or cooling sections of the concrete as needed. Properly managing the curing process means infrastructure projects can last up to 125 years without remediation, while projects not properly cured may last only half that time.
On the equipment side, all GOMACO pavers have the most up to date G+ control system and GOMACO Remote Diagnostics (GRD), both of which allow GOMACO to communicate with pavers remotely. The GOMACO Navigator software consolidates all the G+ paver accessories, allowing pavers to communicate with each other while on the same jobsite.
Additionally, sensors on the jobsite, from safety backup sensors for rollers and equipment to wearables that help detect worker jolts and falls, will proliferate in the next decade, according to AEM.
“It starts with understanding what’s going on on the site and that’s where sensors really came into it. There already are a number of internet-connected devices—sensors on the machines that are feeding information all the time,” Gallant said. “Our problem has not been getting the information. It’s been how we use it, how to consolidate it and how we use it smartly. And that’s, I think, the next big frontier here…We get better and better at controlling the sites and helping the operators be better, more efficient, more sustainable operators.”
Better insight into jobsite safety will ensure proper construction, according to Gallant and AEM, keeping the future of roads on the right track.
Smartest Manufacturing Processes
As Faulhaber put it during a discussion at bauma in Munich, Germany, the path to more sustainable road construction does not pass through the engine—or battery—compartment. While much of the focus around sustainability and construction focuses on the emissions of construction equipment, the majority of roadbuilding’s carbon footprint lies in the production and transportation of asphalt and concrete.
The company believes that type of digital optimization can be effectively expanded beyond the roller and surface to not only the jobsite as a whole, but to every step of the roadbuilding process, including production and transport. Ultimately, these greater efficiencies won’t just reduce the industry’s carbon footprint but will also ease the difficulty contractors face in finding enough skilled workers.
The company envisions fully networked and connected jobsites for the roads of the future and is dedicated to pushing the industry forward through the promotion of these connected jobsites and networking tools.
But beyond the need for solutions to decrease carbon emissions that are optimized and designed specifically road building, BOMAG tempers this work with feedback from customers. And those conversations differ greatly depending on where in the world the feedback is coming from.
In Europe Faulhaber says they do hear from more contractors who name reducing carbon footprint as a core goal of their business. That sentiment isn’t held nearly as widely among contractors in North America where Faulhaber suspects legislation will be the key driver in the industry’s move toward more sustainable fuels such as electric- or hydrogen-powered equipment.
Which points us right back to why optimizing the production and transportation of materials, and making the actual installation of the asphalt or concrete surface more efficient is the best focus for BOMAG and its peers in the industry. While there is little global agreement on the viability of zero-emissions equipment with the current state of charging infrastructure, battery technology, and hydrogen fuel technology in general, process optimizations are hard for anyone to argue with.