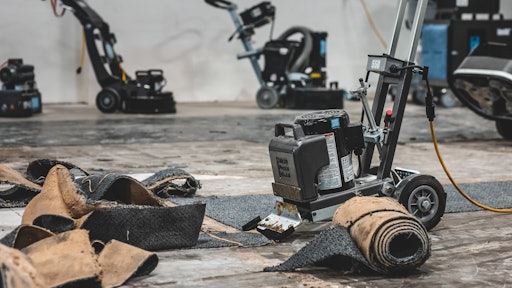
When you watch a professional chef at work, you might notice that they’re using a selection of knives. That’s because chefs, like any craftsman, will select a tool based on the task — for example, while one knife might easily cut through vegetables, it might be impossible to use it for filleting fish. Similarly, contractors have different blades at their disposal for different surface preparation jobs, but is it always clear which blade is best to use? Let's look at the variations between different types of blades for floor preparation and when to use each.
When preparing for any surface preparation job, contractors will assess the job site to determine the current floor material and condition, access to the space, and power availability. These parameters will influence machine choice — for example, a walk-behind scraper will easily remove soft goods on higher floors with weight limitations. In contrast, a ride-on scraper works better when removing hard goods in larger, ground-floor spaces.
While contractors often take the time to select the best type of floor scraper for material removal, it’s not always the same case when it comes to tooling choice. Instead, our team often receives phone calls from contractors part way into their job claiming that the machine is broken. However, when we look at what they’re doing, the machine is fine —they’ve just selected the wrong tooling for the job.
So, how do contractors select the right tool?
Performance Not Value
It might sound cliché, but in most cases, it is true that you get what you pay for. This is particularly true for surface preparation equipment tooling where I often see contractors trying to save money by selecting the thinnest blade on offer for their ride-on scraper.
While thinner blades are the cheaper option, they are designed for smaller jobs and walk-behind scrapers, so are likely to wear down quickly on a larger machine and tougher application. As it gets dull, contractors can increase the angle of the tool to remove material, but this can cause the metal to bend, making work harder or stopping it completely.
Alternatively, using a blade that is too long or wide during floor removal can slow down production. Concrete will never be completely flat — the aggregate used in the material will cause some undulations. As a result, using a longer blade against concrete means contractors must move very slowly to ensure they only remove the covering or adhesive, leaving the concrete intact. Take this comparison: if a contractor is using a longer 14-in. blade on concrete, they might have to move so slowly that they can only remove 10 ft. of a material a minute, but if they swapped to a 10-in. blade in the same application, they could remove 100 ft. of material a minute.
Contractors might not always know what blade is best for the job, so just like chefs have multiple knives in their restaurant, contractors should consider having a toolkit of multiple blades on-site. They can start with one blade and if removal begins to slow or the blade becomes blunt quickly, they can drop down until they find the right tool for the job.
Bevel Up Or Down?
When selecting a blade for floor removal, should you choose a bevel-up or a bevel-down blade? Often, when talking to contractors, they are unaware that there is a difference between the two, let alone when to use each type.
A blade with the bevel up — where you can see the angle of the blade from above — is best for removing flooring from concrete. A blade with the bevel down — where the bevel is underneath and cannot be seen — is best for removing a covering from wood. It is often easier to remember it as bevel-up blades are for downstairs, where contractors are more likely to use ride-on scrapers on concrete, and bevel-down blades are for upstairs, where contractors use lighter walk-behind scrapers on wood.
When removing a covering or adhesive from concrete, using a bevel-up blade at a higher angle creates more pressure to separate material from the substrate. However, if you used the same blade on a wooden substrate, that pressure would hit the wood, scratching the surface. Instead, having the bevel on the bottom allows the tool to glide over the wood.
If a contractor finds that floor removal rates are low, it doesn’t necessarily mean that the machine is broken. Preparing a floor is like preparing a meal, if you take the time to select the right tools for the job, you can be more precise and end up with a better result.
About the author
Dave Bigham is Global Director of training at National Flooring Equipment.