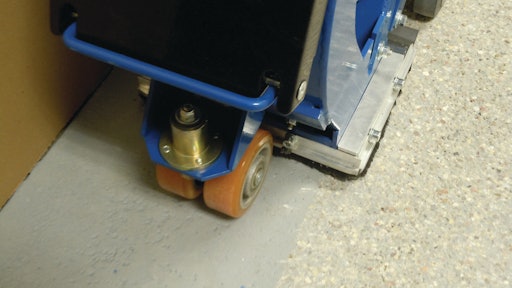
Polishing a concrete floor is an art form. For those of you who do it every day, your instincts and experience guide your work. Your customers depend on your professionalism and knowledge base. Unfortunately, as every restaurateur knows, you’re only as good as your last meal. So, how do you expand your business, keep your current customer base happy, capture more customers and stay within budget? Diversify.
You understand grinding and polishing. So the concepts of down pressure, surface density, consumable quality and dust-collection make sense. Surface preparation is the name of the game and there are additional tools and equipment which can complement your line and work.
Floor scraping
The purpose of floor scraping is to remove old layers of finish from the floor. Scraping a floor can be quick and clean — if you have the correct tools for the job. Using a powered walk-behind or ride-on scraper machine reduces time and labor compared to using manual tools. Floor scrapers can adapt to your job with the variety of tools, blades and shanks available.
Floor scrapers range from small walk-behind, manually propelled units up to big multi-thousand-pound ride-on machines, many of which can cost the same as a new sports car! These machines, also known as tile chippers or strippers, are the strongest foundation of environmental abatement work and the first step to reapplying new surfaces. Just like grinding and polishing, down pressure and surface area are the key components to successful scrapers. In addition, angling the blades or shanks for the appropriate job will make your life much easier. Most ride-on floor scrapers will remove mastic in the first pass when peeling up carpet or vinyl. Typical removal rates for carpet/vinyl tile are as high as 3,000 square feet per hour and ceramic tile removal rates can be as high as 800 square feet per hour, depending on the thickness and hardness of the thinset. These machines are often propane powered; however, the newest generation of batteries allows the same amount of power output while still being able to operate in government facilities, schools and hospitals.
Shot blasting
Shot blasting is an economical and environmentally safe process for preparing concrete, steel and asphalt surfaces for the application of coatings or overlays. These blasting systems can strip, clean and profile your surface simultaneously, saving you time, money and labor.
A shot blaster works by forcibly propelling a stream of abrasive material against a surface under high pressure. This will smooth a rough surface, roughen a smooth surface, shape a surface and/or remove surface contaminants. In shot blasting machines a centrifugal wheel is used to propel the blasting material, referred to as media, but in other forms of blasting a liquid will often be used. These machines are work horses. They will profile just about any surface and are very common for parking decks, highways, gas tank restoration and all the little jobs like driveway lips and concrete edges. These machines are excellent for industrial floor prep, road and airport maintenance, asphalt blasting, decontamination, and more.
Scarifiers
Another option for surface preparation is scarification. Scarifiers are general bulk material removal tools. The spinning drum has attachment heads which operate with hundreds of cutting, smashing and ripping blades, chips or teeth. Scarifiers have a variety of cutters, accessories and tooling selection services: maximum production rates, infinite profile patterns and a variety of depth settings for the most difficult jobs.
Surface preparation can be tricky; the real culprit is the concrete. These tools can help you navigate through the tough and complicated jobs. It’s worth the effort to research and ultimately purchase from a leading manufacturer with a successful history of designing and constructing quality equipment. In addition, it’s important to partner with a manufacturer that supports their equipment with a proven customer service and technical department. Don’t make an expensive mistake by purchasing exclusively on price. An initial cost savings can be quickly eased by an inferior product or non-responsive customer service. Often jobs will be affected by factors outside of your control. Just like in concrete polishing and grinding, if you don’t follow the steps correctly, the finished product won’t turn out the way you had hoped.