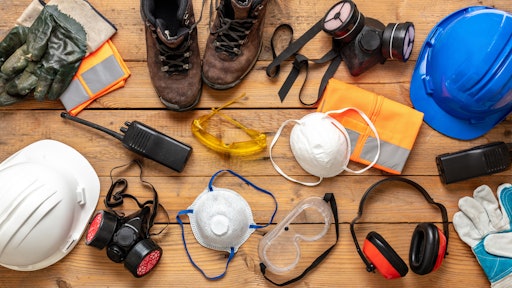
Safety technology in tool design is like a personal bodyguard that stands between a worker and a hazard 24/7 to prevent injuries. In tool design, safety technology physically reduces workers’ risk of exposure with very little change to their workflow. Unlike a seatbelt, where the operator still must actively think about putting it on, the safety technology designed and built into the next generation of many solutions will protect workers whenever the equipment is running.
On jobsites, safety professionals address the hazards and risks of a job through application of the Hierarchy of Controls issued by the National Institute of Occupational Safety and Health (NIOSH). Within the Hierarchy of Controls, safety technology is considered an engineering control.
The National Institute for Occupational Safety & Health (NIOSH) has stated, “Engineering controls are favored over administrative and personal protective equipment (PPE) for controlling existing worker exposures in the workplace because they are designed to remove the hazard at the source, before it comes in contact with the worker. Well-designed engineering controls can be highly effective in protecting workers and will typically be independent of worker interactions to provide this high level of protection.”
Advances in Technology
In general, safety technology encompasses all new technologies now being applied to workplace safety. They include: machine sensors, mobile apps, wearables, cloud-based software, predictive analytics, robotics, real-time employee monitoring and tracking, PPE tracking with embedded sensors, and others.
Here are some recent examples of Safety technology designed to help protect workers:
- Noise reduction: Every year, thousands of construction workers experience hearing loss from excessive noise exposure on the job. “Noise-induced hearing loss” affects workers’ quality of life and increases the risk of injury. Some manufacturers conduct product sound power tests in fully isolated Hemi-Anechoic Sound Chambers. The investment in this type of research allows manufacturers to collect objective noise data to positively influence product design.
- Self-cleaning vacuums: Some HEPA vacuums feature automatic filter cleaning mechanisms that make them Table 1 compliant with the Occupational Safety and Health Administration (OSHA) regulation on respirable crystalline silica dust (29 CFR 1926.1153). These filtration systems capture 99.97% of all particles greater than 0.3 microns and do not require the user to spend downtime cleaning them.
- Blade stop: Grinders, which may be set down and picked back up in a quick sequence, are among the most common tools involved in jobsite injuries. The safest way to set down a grinder is to bring the wheel to a stop – but on some grinders this can take up to 9 seconds. Some grinders have innovative braking technology and can stop the accessory in as little as 1 second when a finger is lifted from a trigger.
- Anti-vibration: Excessive vibration can lead to improper blood flow and the potential for long-term debilitating injuries. To help reduce the occurrence and severity of these injuries, the Anti-Vibration System (AVS) in rotary hammers was designed for continuous drilling and reduces the tool’s vibration by utilizing a variety of mechanical designs. With the constant activation of this system, users will experience less fatigue and fewer issues with circulatory concerns, specifically around their hands.
Support for Health and Safety Professionals
Building a company-wide safety culture to protect workers is a choice that is reinforced in daily decisions, such as equipment selection. Safety technology can support an organization’s safety goals:
- Protect workers and help build a safety culture: Safety technology can become a cultural grounding point for an organization, letting workers know that the everyday risk is recognized and that they work for an organization that cares. Workers are a company’s most important resource. Purchasing equipment with safety technology and educating workers on benefits and use is a responsible investment in future worker health.
- Use equipment budgets to strategically support the business: Organizations recognize that the ramifications for injuries on the job impact more than just the worker – they also have a domino effect on the company’s bottom line. While it’s not surprising that the upfront cost of new solutions can be an initial hurdle for some companies, the long-term cost savings, productivity improvements, and overall impact on worker morale can provide significant savings. As NIOSH affirms: “The initial cost of engineering controls can be higher than some other control methods, but over the longer term, operating costs are frequently lower, and in some instances, can provide a cost savings in other areas of the process.”
- Save the direct and indirect cost of injuries: Equipment featuring safety technology can help prevent insurance rate hikes due to claims, along with the productivity cost of days away from work. In 2016, musculoskeletal disorders (MSDs) of all types, which can be caused by core drilling injuries, comprised about 40% of all lost-time workplace injuries (356,910 of 902,200). The numbers are likely low, as several studies have found that both workers and employers may under-report MSDs, according to the NORA for Musculoskeletal Health. Battery-powered light equipment featuring safety technology can help reduce claim costs and help avoid injuries, such as MSDs.
Bottom Line
While elimination of hazards and substitution rank at the top of the NIOSH hierarchy in dealing with jobsite risks, new solutions focused on safety technology are often some of the most impactful. Safety technology is part of a larger jobsite evolution that’s changing the way work gets done. New and safer battery-operated solutions redefine light equipment, including core drills. These solutions offer user-driven designs, including engineering controls that supply safety, productivity, and ease of use. The mindset on today’s jobsites has changed. Workers realize that the historic safety risks they used to accept as “part of the job,” such as the risks surrounding traditional core drilling, are now addressable on jobsites. As Koetter Construction Hardscape Manager Nick Moses said, “You don’t know what you don’t know. We accepted the problems, but now we realize we don’t have to.”