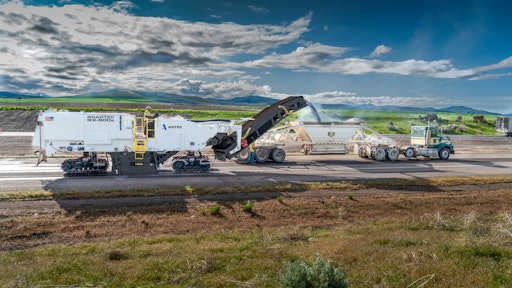
The use of recycled asphalt pavement (RAP) is continuing to grow in the United States. In 2020, the National Asphalt Pavement Association reported that the industry reclaimed 97 million tons of RAP for future use, saving about 58.9 million cubic yards, or enough landfill space to fill up the dome of the U.S. Capitol 1,223 times. This massive reclamation effort also saved $5.3 billion in gate fees for disposal in landfills.
Our country’s most diligent recyclers are in fact asphalt mixture producers, who utilize more than 94 percent of old asphalt pavements in new pavement construction. But are they doing the best they can to ensure these materials are being recycled properly?
“Sizing of RAP can have a dramatic effect on how well RAP goes through asphalt plant," Kyle Neisen product, roadbuilding at Astec Industries says. “A more consistent size coming in off milling machine will be more efficient for everyone involved.”
By maintaining RAP quality in the field, the asphalt plant can achieve a faster turnaround using the RAP in a new mix design. Here are some ways to do that.
Impact of Operator
Operators play a huge role in the success of your operations, but this is especially true when milling where the operator plays the biggest part in ensuring quality.
“How an operator runs the machine will absolutely determine the quality of the RAP,” Austin Miller, paving development manager at BOMAG Americas says. “If he runs too fast or raises the front moldboard too high, it can produce large slabs that will have to be processed through a crusher and screen and stacked for use at a later date. If the operator can produce a consistent material with minimal deviations the material can be processed during the making of the new mix with a small grinder or wrap wrangler prior to being put into the material bin on the asphalt plant.”
Therefore, consistency is key to RAP quality control.
“By maintaining a consistent pace of milling, and not going too fast, operators can help control quality,” Niesen adds. “If the operator slows down a few feet per minute it can help the machine get consistent size material.”
Machine controls can help with this.
“Properly setting things like rotor speed, travel speed, front antislab and rear moldboard position all contribute to achieving the desired pattern or surface finish behind the mill,” Jameson Smieja, global sales consultant with Caterpillar Cold Planers says. “Also proper setting and use of an automatic grade and slope systems significantly improves the profile of the milled surface to be repaved.”
Operators also need to be aware of other factors outside of their control like the material being milled which impacts their water usage.
“The material does have something to do with quality as well,” Tom Chastain, milling product manager at Wirtgen America says. “How much water we are running can affect the RAP once it hits the plant due to how much water consumption the material has. Too much water consumption could mean we need to run the RAP thru the dryer to bring that down some.”
Importance of the Drum
The drum you choose will obviously determine the size of material being processed and that is usually influenced by the desired spec of the job.
“Different cutting tools will affect sizing of material,” Chastain says. “Different sized carbide or diamond tools can either cut the material is small sizes, or larger flakes.”
The finer the drum pattern, the finer the material will be.
“That is not always good you don’t want to create more fines, that is counterproductive in most cases,” Miller cautions. “Bottom line, pick the drum for the surface texture you desire not for the RAP quality.”
“In general, you can hit any smoothness spec with any drum if know how to control machine,” Niesen says. “Not frequently do you have to go to micro milling or quad wrap but doing either can help maintain production speeds while also achieving desired smoothness.”
One you have that drum in place, making sure it’s properly maintained is paramount to the success of your milling application.
“The maintenance of the drum is key in the quality of the RAP produced,” Miller says. “With good tooling you will get a cleaner cut and less breakage of the aggregate. Once the teeth reach stage 4 or 5 of wear, they will tend to break the material or crush instead of cutting. Watching your cut pattern and checking your teeth on a regular basis will ensure you are getting quality material.”
Last but not least, monitor the milled surface and make adjustments as necessary, including the replacement of cutting teeth. This will help maintain the best quality throughout the job.
“Cutting tools affect not only RAP sizing, but machine performance and pattern quality,” Chastain says. “Operators need to keep an eye on what the pattern looks like, how is the machine performing and look at the material that is being loaded into the truck. As cutting tools wear, pattern quality can go down, then the machine performance goes down, then we see the RAP sizing start to be affected. If the cutting tools are wearing evenly, maybe we just need to slow the machine down, or possibly change what working parameters or drum speed we have the machine in.”
Maintaining best practices across the board can be better than changing the drum, both in terms of quality and productivity.
“At the end of the day, control the factors you can control,” Chastain says. “Machines need to be maintained properly and drum maintenance is extremely crucial. We need to have a cutter drum that is well maintained, and the proper cutting tools installed to achieve higher quality. Water spray systems also need to be in proper working order to make sure we are getting proper spray to the key areas.”
Proper Storage & Processing
Once RAP is transported back to the plant, the importance of quality control continues. The transportation, storage and utilization of RAP is always a logistical challenge, but the single most important best practice is to treat RAP the same way you treat virgin materials. This means always keeping the RAP clean and dry before it’s reprocessed and put back on our roadways.
When possible, store processed RAP stockpiles under cover, or at least in an area with a sloped surface and good drainage. NAPA recommends paving underneath stockpiles to allow for proper drainage.
“Storing processed RAP in a covered building is the most desirable,” Miller says. “It will keep the direct sun off the material which can heat the material up and cause it to stick back together. If you have to store out in the open try and process just enough for your job as close to the start of the job as you can so it has less time in the sun.”
One practice that makes higher percentages of RAP more successful is fractionation of the material. A producer should separate the material into two or more stockpiles based on the size of the RAP particles. It's becoming more common to separate RAP into a coarse pile, with particles of more than ½ or 3/8-inch in size, and a fine pile with particles of ½-inch minus or so. That lets contractors use fine RAP in finer asphalt mixtures and coarse RAP in coarse mixtures.
Crush only what you need for a two- to three-month period. Re-use of the RAP material is recommended within two-to-three-month period. Longer storage periods may be expected when the material is under cover. Also, avoid driving loaders on RAP stockpiles, which leads to premature compaction of the processed RAP.
The use of RAP is not going away. Follow these best practices for processing and stockpiling the material and you’ll be sure to produce a better-quality product.