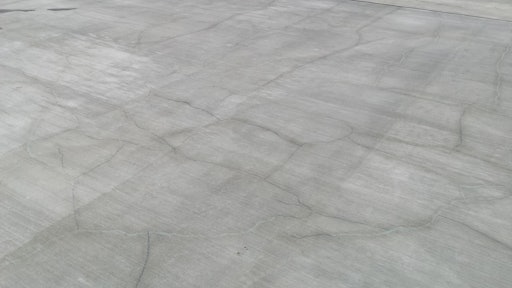
Concrete cracks for various reasons including plastic concrete shrinkage and settlement, thermal contraction, drying shrinkage and loading of the structure. Because the tensile strength of concrete is only about 10 percent of the compressive strength, even small tensile stresses associated with shrinkage and loads can crack concrete. Regardless of the cause, cracks in new structures typically raise concerns about an increased risk of rebar corrosion and premature concrete damage, especially if the structure is exposed to moisture.
Historically, there have been two theories related to cracks and steel reinforcement corrosion:
Theory 1 - Cracks significantly reduce the service life of structures by permitting access of carbon dioxide, chlorides, water and oxygen to the reinforcing steel that accelerate the onset of reinforcement corrosion.
Theory 2 – While cracks may accelerate the onset of corrosion, it is localized and confined to the bar area intersected by the crack.
Over the years, researchers have debated theories one and two using both laboratory and field test data (Ref 1). An abundance of published information appears to support both theories. However, A.W. Beeby, Dr. Chanakya Arya, and Professor Laurence Wood essentially ended the debate by concluding both theories are correct (Ref. 2 and 3). Briefly, these researchers (and others) concluded the following:
- Crack width have little influence on corrosion.
- Major factors controlling corrosion are concrete quality (e.g., cementitious materials content and water to cementitious materials ratio - w/cm ratio) and concrete cover.
- Corrosion potential is strongly influenced by the orientation of the crack relative to the reinforcement (i.e., coincident versus intersecting). Theory one applies to cracks that coincide with the reinforcement and Theory two applies to cracks that intersect the reinforcement.
Reinforcement corrosion
Corrosion of steel reinforcement in concrete is due to an electrochemical process as illustrated in Figure 1. There are four essential parts to an electrochemical corrosion cell:
- Anodic site where ferrous ions (Fe++) pass into solution and due to a secondary reaction with oxygen and water form rust (or the expansive product of steel corrosion).
- Conductor (steel reinforcement) that provides a conduit for excess electrons (e-) to move to the cathodic site.
- Cathode where electrons are consumed in the presence of oxygen and moisture.
- Electrolyte or wet concrete that provides a conduit for hydroxyl ions (OH-) to flow to the anodic site.
Steel reinforcing bars embedded in concrete do not corrode because the high alkaline conditions in concrete (pH > 13) produce a passive oxide film on the surface of the steel. The passive oxide film prevents corrosion. However, carbonation and/or chlorides in solution can destroy the passive oxide film. Carbonation and loss of passivity can occur when atmospheric carbon dioxide penetrates into the concrete and in the presence of moisture reacts with the calcium hydroxide to produce calcium carbonate. Calcium hydroxide is a cement hydration product that helps create the high alkaline condition in concrete. Due to the formation of calcium carbonate around the steel, the alkalinity (pH) of the concrete falls from above 13 to less than nine. Subsequently, the low alkalinity destroys the passive oxide film.
Carbonation is a very slow process in good quality concrete. Therefore, the risk of depassivation of steel reinforcing and onset of corrosion depends on the permeability of the concrete, concrete cover and exposure conditions (i.e., moisture). Of course, cracks can open a direct pathway for carbon dioxide to reach the steel and disrupt the passive oxide film. If the other essential conditions for corrosion exist, then an anodic site can form and corrosion can occur where the crack intersects the reinforcing bar.
For corrosion to occur, oxygen and moisture must be available at both the cathodic region and along the hydroxyl ion conduit (concrete) between the cathode and anode. Since these two requirements for corrosion are independent of the crack width, it follows that the corrosion rate of the steel reinforcing is also independent of the crack width. Many researchers report there is no correlation between crack width and steel reinforcing corrosion in concrete (Ref 4).
Therefore, the major factors controlling the risk of steel reinforcing corrosion of cracked concrete are the quality of concrete and concrete cover — not the crack width. Good quality concrete (i.e., low permeability) and adequate concrete cover inhibits the cathodic site and the hydroxyl ion conduit from forming. Without the cathode and hydroxyl ion conduit, the electrochemical corrosion cell does not form and steel corrosion does not occur.
High quality of more specifically dense concrete reduces the risk of corrosion by restricting the penetration of oxygen and moisture into the concrete, restricting ionic movements within the concrete and increasing the bond strength of the concrete to the steel. Of course, the quality or more specifically, the permeability of the concrete depends on several factors including the cementitious materials content, water-cementitious materials ratio, concrete consolidation and curing. Increasing the cement content can help reduce permeability but also increases the alkali loading or content of the concrete that helps maintain the concrete’s alkalinity and preserve the passive oxide film on the steel reinforcement.
Building codes establish the minimum concrete cover according to the anticipated exposure of the concrete to moisture. As the concrete’s exposure to moisture increases, the minimum specified concrete cover increases. For a #6 bar, the specified minimum concrete cover is three-quarters of an inch when concrete is not exposed to weather or in contact with the ground, two-inches when concrete is exposed to earth or weather and three-inches when concrete is cast against and permanently exposed to earth. Increasing the concrete cover reduces the risk of steel reinforcing corrosion.
Crack orientation
There are two orientations of cracking in reinforced concrete:
- Longitudinal (i.e., cracks running parallel or coincidental with the steel reinforcing).
- Transverse (cracks intersecting the steel reinforcement) as illustrated in Figure 2.
Longitudinal cracks follow the line of reinforcement and transverse cracks cross the reinforcement. Transverse cracks include diagonal cracks.
Longitudinal cracks
Depending on the width of the crack where it intersects the steel, longitudinal cracks may promote corrosion of the steel reinforcement. Increased risk of corrosion occurs because passivity of the steel may be lost at several locations along the reinforcing. In addition, the same crack may allow the migration of oxygen and moisture to the cathodic sites and to the hydroxyl ion conduit completing the formation of the electrochemical corrosion cells. Theory One applies to longitudinal cracks.
Typically, longitudinal cracks occur due to plastic settlement or subsidence of the concrete, poor concrete quality and inadequate concrete cover. Poor concrete quality and inadequate cover may allow the formation of electrochemical corrosion cells and expansive corrosion products and subsequently cause longitudinal cracks to occur. Of course, the formation of longitudinal cracks typically and classically promotes the corrosion of the steel reinforcing.
Transverse cracks
Intersecting cracks may open a direct path for carbon dioxide, oxygen and moisture to reach the steel reinforcing. However, because the cathodic sites are primarily confined to the crack-free regions of the concrete, any oxygen and moisture that penetrates into the crack will not affect the onset or rate of steel corrosion along the rebar or where the crack intersects the rebar. Therefore, transverse cracks do not increase the risk of steel corrosion unless the concrete is of poor quality and/or the concrete cover is inadequate so that oxygen and moisture easily penetrate the concrete. Theory Two applies to transverse cracks.
When evaluating new cracks and the potential for rebar corrosion, crack orientation, concrete cover, quality of the concrete and exposure conditions are just as or more important than crack widths.
References
- Darwin, D., “Debate: Crack width, cover, and corrosion,” Concrete International, American Concrete Institute, www.concrete.org, May 1985
- Beeby, A. W., “Cracking, Cover and Corrosion of Reinforcement,” Concrete International, American Concrete Institute, www.concrete.org, February 1983
- Technical Report No. 44, “The Relevance of Cracking in Concrete to Corrosion of Reinforcement,” A Report of a Concrete Society Working Party, The Concrete Society, www.concrete.org.uk, 1995
- Beeby, A.W., “Cracking, Cover and Corrosion of Reinforcement,” Concrete International, American Concrete Institute, www.concrete.org, February 1983
Additional Reading from the American Concrete Institute, www.concrete.org
ACI 224R-01 Control of Cracking in Concrete Structures
ACI 224.1R-07 Causes, Evaluation and Repair of Cracks in Concrete Structures
ACI 222.2R-92 Cracking of Concrete Members in Direct Tension
ACI 222.3R-11 Guide to Design and Construction Practices to Mitigate Corrosion of Reinforcement in Concrete Structures,