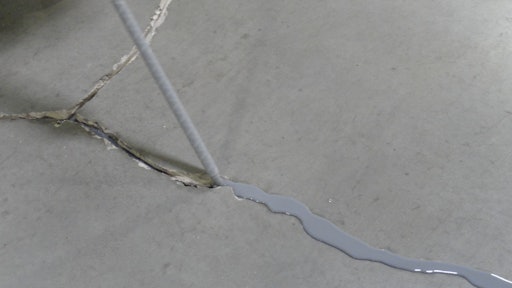
Concrete cracks. That’s a fact.
After investigating the cracks and establishing the repair objectives, designing or selecting the best repair material and procedure is fairly straight forward. This summary of crack repair options addresses the following procedures: clean and fill, rout and seal/fill, epoxy and polyurethane injection, autogenous healing, and “no repair.”
Investigating Cracks
As discussed in "Part I: How to Evaluate & Troubleshoot Concrete Cracks," investigating cracks and determining the root cause of the cracking is the key to selecting the best crack repair option. Briefly, the critical items needed to design a proper crack repair are average crack widths (including minimum and maximum widths) and determining if the cracks are active or dormant. Of course, the objective(s) of the crack repair is just as important as measuring crack widths and determining the potential for future crack movements.
Active cracks are moving and growing. Examples include cracks resulting from continuing ground settlement or cracks acting as contraction/expansion joints for the concrete element or structure. Dormant cracks are stable and future movements are not anticipated. Typically, cracking caused by concrete drying shrinkage will be active at the beginning but eventually stabilize and become dormant as the moisture content of the concrete stabilizes. Also, if there is sufficient reinforcing (steel rebar, steel fibers, or macro-synthetic fibers) crossing through cracks, future movements are controlled and cracks may be considered dormant.
For dormant cracks, use either rigid or flexible repair materials. Active cracks require flexible repair materials and special design considerations to allow for future movements. Using a rigid repair material for active cracks typically results in cracking of the repair material and/or the adjacent concrete.
Photo 1. Using a needle tip mixer (14, 15 and 18 gauge), a low viscosity repair material can easily be injected into hairline cracks without routingKelton Glewwe, Roadware, Inc.
Of course, it is important to establish the cause of cracking and to determine if the cracks are structurally significant or not. Cracks indicating there may be a design, detailing, or construction error raise concerns about the load-carrying capacity and safety of the structure. These types of cracks may be structurally significant. Cracking can be load-induced or related to intrinsic volume changes of the concrete such as drying shrinkage, thermal expansion, and contraction and may or may not be significant. Before selecting a repair option, identify the cause and consider the significance of the cracking.
Repairing cracks caused by design, detailing, and construction errors is beyond the scope of a simple article. This situation typically requires a comprehensive structural analysis and may require special strengthening repairs.
Repair Objectives
Restoring the structural soundness or integrity of a concrete member, stopping water leaks or sealing out water and other harmful elements such as deicing chemicals, providing crack edge support, and improving the appearance of the crack are common repair objectives. Considering these objectives, repairs can be loosely divided into three categories:
- Integrity repairs - Restoring the element to the original strength and stiffness,
- Sealing/filling, and
- Cosmetic repairs.
With the popularity of exposed and architectural concrete, the demand for cosmetic crack repairs is increasing. Sometimes integrity repairs and crack sealing/filling are required to be cosmetic repairs too. Before selecting the repair technique, be sure to clearly establish the objectives of the crack repair.
Before designing a crack repair or selecting a repair procedure, there are four key questions that must be answered. Once these are answered, it will be easier to select a repair procedure option.
- What are the average, minimum, and maximum crack widths?
- Are the cracks active or dormant?
- Is the repair an integrity repair or crack sealing or filling?
- Is the repair a cosmetic repair?
Photo 2. Using clear adhesive tape, drilled holes, and a rubber-tipped mixing tube attached to a hand-held, dual-cartridge gun, a repair material can be injected with low pressure into hairline cracks.Kelton Glewwe, Roadware, Inc.
Crack Repair Options
Clean and Fill
This simple technique has become popular, especially for architectural type repairs because of the very low viscosity repair materials that are now available. Because these repair materials can easily flow into very narrow cracks via gravity, no routing (i.e., installing a square or V-shaped sealant reservoir) is required. Since no routing is required, the final repair width is the same as the crack width which is less noticeable than routed cracks. Also, cleaning with a wire brush and vacuum is considerably faster and more economical than routing.
First, the crack is cleaned to remove dirt and debris, and second, filled with a low viscosity repair material. Manufacturers have developed very small diameter mixing nozzles attached to hand-held, dual-cartridge guns to install repair materials (photo 1). If the nozzle tip is larger than the crack width, some crack routing may be required to create a surface funnel to accommodate the size of the nozzle tip. Check the manufacturer’s literature for the viscosity; some manufacturers state the minimum crack width that is appropriate for the material. Measured in units of centipoise, as viscosity's value decreases the material becomes thinner or flows more easily into narrow cracks. A simple, low-pressure injection process can also be used to install repair materials (see photo 2).
Photo 3. Routing and sealing consist of first cutting a sealant reservoir with either a square or V-shaped blade and filling with an appropriate sealant or filler. As shown, the routed cracking is being filled with a polyurethane and after curing, it was scraped flush with the surface.Kim Basham
Rout and Seal/Fill
This is the most common procedure to repair isolated, fine, and large cracks (photo 3). It is a nonstructural repair that consists of enlarging the crack (routing) and filling it with a suitable sealant or filler. Depending on the size and shape of the sealant reservoir and the type of sealant or filler used, routing and sealing can repair both active and dormant cracks. This method is ideal for horizontal surfaces but can also be used for vertical surfaces with non-sag repair materials.
Appropriate repair materials include epoxies, urethanes, silicones, polyureas, and polymer mortars. For slabs, designers must choose a material with suitable flexibility and hardness or stiffness properties to accommodate both the anticipated floor traffic and future crack movements. As the flexibility of the sealant increases, tolerance to crack growth and movement increases but the load carry-capacity of the material and crack edge support decreases. As the hardness increases, load carry-capacity and crack edge support increase but the crack movement tolerance decreases.
Figure 1. As the shore hardness number of a material increases, the hardness or stiffness of the material increases and the flexibility decreases. To prevent crack edge spalling of cracks exposed to hard-wheeled traffic, a minimum shore hardness of about 80 is required.Kim Basham
For active cracks, the size and shape factor of the sealant reservoir is just as important as selecting a suitable sealant that can accommodate future anticipated crack movements. The shape factor is the depth to width ratio of the sealant reservoir. In general, recommended shape factors are 1:2 (0.5) and 1:1 (1.0) for flexible sealants (see figure 2). Reducing the shape factor (by increasing the width relative to the depth) will decrease the sealant strain caused by crack width growth. If the maximum sealant strain is reduced, the amount of crack growth the sealant can tolerate increases. Using the manufacturer’s recommended shape factor will ensure maximum elongation of the sealant without failure. If needed, install a foam backer rod to limit the depth of the sealant and to help form the “hour-glass” elongated shape.
The allowable elongation of the sealant decreases as the shape factor increases. For a 6-in. thick slab with a full-depth 0.020-in. crack, the shape factor without a sealant reservoir is 300 (6.0 in. / 0.020 in. = 300). This explains why active cracks sealed with a flexible sealant without a sealant reservoir commonly fail. Without the reservoir, the strain quickly exceeds the tensile capacity of the sealant if any crack growth occurs. A sealant reservoir with a shape factor as recommended by the manufacturer of the sealant should always be used for active cracks.
Figure 2. Increasing the width versus depth ratio will increase the sealants ability to tolerate future crack moments. Use 1:2 (0.5) to 1:1 (1.0) shape factor or as recommended by the manufacturer of the sealant for active cracks to ensure the material can properly stretch with future crack width growth.Kim Basham
Epoxy Injection
Epoxy injection bonds or welds cracks as narrow as 0.002 in. together and restores the concrete’s integrity including strength and stiffness. This method consists of applying a surface cap of non-sag epoxy to confine the crack, installing injection ports into drilled holes at close intervals along horizontal, vertical or overhead cracks, and pressure injecting epoxy (photo 4).
Tensile strengths for epoxies exceed 5,000 psi. For this reason, epoxy injection is considered a structural repair. However, an epoxy injection will not restore as-design strengths nor strengthen concrete cracked due to design or construction errors. Seldom will injecting cracks with epoxy resolve issues associated with load-carrying capacity and structural safety concerns.
Photo 4. Before injecting epoxy, the surface of the crack must be capped with non-sag epoxy to confine the pressurized epoxy. After injection, the epoxy cap is removed by grinding. Typically, cap removal leaves grind marks in the concrete.Kim Basham
Epoxy injection is a rigid, full-depth repair where the injected crack will be stronger than the adjacent concrete. If active cracks or cracks acting as contraction or expansion joints are injected, expect other cracks to form next to or far away from the repaired crack. Only inject dormant cracks or cracks that have sufficient amounts of reinforcing crossing the crack so future movements are restrained. The table below summarizes the important selection features of this and the other repair options.
Summary of Crack Repair Options
Repair Method | Active Cracks | Dormant Cracks | Structural Repair | Crack Sealing |
Clean and Fill | √ | √ | ||
Routing and Sealing/Filling | √ | √ | √ | |
Epoxy Injection | √ | √ | √ | |
Polyurethane Injection | √ | √ | √ | |
Autogenous Healing | √ | √ |
Polyurethane Injection
Polyurethane resins can be used to seal wet and leaking cracks as narrow as 0.002 in. This repair option is primarily used to stop water leaks and consists of injecting a reactive resin into cracks that combines with water to form an expanding gel that chokes off the leak and seals the crack (photo 5). These resins will chase the water and penetrate into tight micro-cracks and pores of the concrete creating a firm bond to the wet concrete. Also, cured polyurethanes are flexible and will tolerate future crack movements. This repair option is a permanent repair and works with either active or dormant cracks.
Photo 5. Polyurethane injection consists of drilling holes, installing injection ports and pressure injecting resin. The resin reacts with moisture in the concrete forming a stable, flexible foam that seals cracks, even leaking cracks.Kim Basham
Autogenous Healing
It is a natural process of crack repair that occurs in the presence of moisture for cracks with maximum widths between 0.004 in. and 0.008 in. The healing process is due to the hydration of unhydrated cement particles that are exposed to moisture and the formation of insoluble calcium carbonate on the surface of the crack created by leaching of calcium hydroxide from the cement paste to the surface that reacts with the carbon dioxide in the surrounding air. A 0.004-in. wide crack can heal after several days and a 0.008-in. crack may heal in several weeks. Healing will not occur if cracks are subjected to fast-flowing water and movements.
No Repair
Sometimes “no repair” is the best repair option. Not all cracks require repair and monitoring the crack may be the best choice. If needed, the crack can be repaired later.