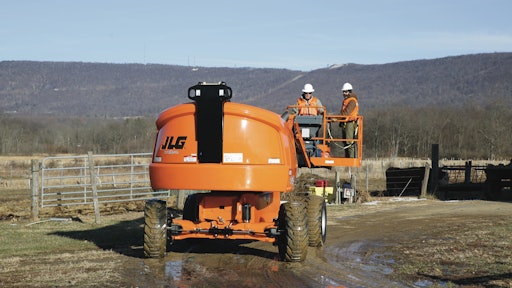
Access control is an idea whose time has come. A growing number of fleet owners are recognizing that it’s a wise investment because it helps them create a safer jobsite and ensures that their machines are being operated properly.
This optional tool allows equipment owners to safeguard their machines and improve jobsite safety by preventing unauthorized personnel from accessing equipment. In the process, it helps to bring order to the chaotic environment of the jobsite.
The typical construction site is not a neat, well-organized, perfectly orchestrated place. Machines and workers are moving everywhere, often on surfaces that are not level. That’s not an environment where you want untrained, unqualified operators using aerial lifts.
Most of the equipment on the jobsite is unsecured. If the keys are in it, anyone can use it. Untrained operators can not only put themselves and other workers in danger but also increase the odds of property or equipment damage.
Safety is Job One
Access control restricts the operation of the aerial lift equipment to qualified and properly-trained people. This list of approved operators can be remotely managed from a centralized web portal, enabling one person to manage hundreds of machines on multiple jobsites.
A list of authorized users is communicated to each machine in the field using telematics and is stored on its access control keypad. That means the system continues working, even if the machine is operating indoors or in areas with little or no cellular connectivity. Once it’s back in range of a cell tower or satellite, its database of authorized users is automatically updated.
It’s in the Cards
Machine operators receive a unique ID number or RFID card that allows them to access only the equipment they are authorized to operate via a keypad on the machine. The RFID cards, produced by the International Powered Access Federation (IPAF) and certain aerial lift manufacturers (including JLG) contain operator data, a list of machine models they’re qualified to operate and when each certification expires.
Access control can be managed via a PIN code, the RFID card or both. Without proper authentication, the machine cannot be started or moved.
RFID cards transform access control from a list of operator numbers and PIN codes into a knowledge system. For example, JLG provides operator training and RFID cards with corresponding qualifications to its customers. That integrated approach helps fleet owners simplify operator administration.
In addition, the RFID cards enable fleet owners to track certifications that need to be renewed regularly. For example, OSHA considers telehandlers to be powered industrial trucks. It mandates that operators of them must be recertified every three years.
Other types of aerial lifts are governed by a voluntary set of ANSI standards, which specify that operators should be certified to operate them. Even though compliance isn’t mandatory, Eckel says that savvy fleet owners are recognizing that it makes sense from a safety and liability standpoint to align themselves with it.
Improved equipment utilization
Access control, in combination with telematics data collected from machines in the field, gives fleet managers a more complete picture of who is using each machine and how. A web-based portal provides them with up-to-date data on hundreds of machines in dozens of locations within one centralized interface. This gives them a more complete picture of machine utilization.
Without access control, the machine’s telematics system reports when a machine is being used and where, along with basic condition data. But, you can’t see who is operating it. Access control helps fleet managers to connect the dots by showing them who is operating each machine. That enables them to do a more effective job of managing machines and people —and ensuring jobsite safety in the process.
For example, if a daily inspection shows that an aerial lift was damaged, the access control system can tell you who the last person was who operated it. And if it’s unsafe to operate, the fleet manager can send a lockout code to the machine that prevents anyone from using it until it’s repaired.
The Future of Access Control
To communicate with machines in the field, access control systems rely on the communications backbone offered by equipment telematics systems. The volume of data that can be transmitted is currently limited by communications bandwidth and the capabilities of today’s telematics hardware. As they evolve and improve in the coming years, they may enable many enhancements to access control.
Currently, telematics systems report on basic equipment data: Location, whether or not the machine is operating and a limited amount of conditional data, such as hour meter readings. Imagine if that could be expanded to include data on how a machine is being used.
Soon, it may be possible to establish a profile of best-operating practices and then compare that to the telematics data from each machine. That could provide key insights into the true level of proficiency of each operator.
For example, are they attempting to move the machine without using the proper interlocks? Do they forget to hit the enable switch? Are they using the footswitch properly? Are they exceeding the machine’s maximum slope capabilities? Is the machine generating alarms that indicate they’re pushing the limits of the machine’s capacity when performing lifts?
In many cases, this data is captured on electronic control systems on the machine; it just isn’t being reported by its telematics system — yet. But, it will be as the technology improves. Once this detailed operating data becomes available, it may ignite a revolution in operator training.
It would enable you to provide operators with customized training to correct the areas where they need help. You could even put them in a virtual training environment where they could practice the operations and procedures where they need reinforcement. The data is all there. It's just a matter of developing a prescriptive training plan based on their on-the-job performance.
A Global Groundswell of Support for Access Control
Even though these advanced training capabilities are a few years away, rental companies and contractors can enjoy the benefits of access control today. As more safety-conscious fleet owners adopt it, its momentum is growing worldwide.
One driver of this trend is that a growing number of countries are adopting ISO standards for operator training and qualification. It was designed to align U.S. aerial lift standards more strongly with the popular European mandate.
There’s no question that a safer jobsite is a more productive one. Making sure that only authorized users are operating equipment is a big part of that equation. If you’re concerned about keeping your people safe and protecting the value of your equipment assets, access control is a no-brainer.