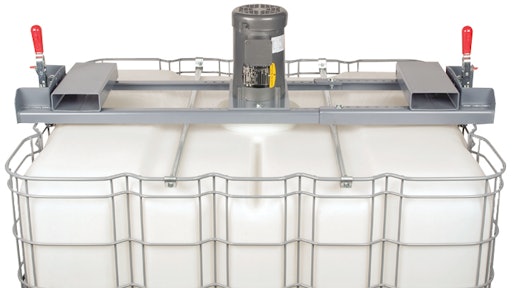
The commercial construction industry is largely responsible for how the man-made features of our country look, function and last. Whether it’s the buildings in which we work, the roadways and mass transit infrastructure we travel, or the single and multi-family homes in which we live, construction contractors play a critical role in the quality of our daily lives. While heavy materials such as steel beams, formed concrete, lumber and glass form the structural foundations of major building projects, liquid products also play an important role; from protecting raw materials against the elements to improving the aesthetics of buildings and homes. Functional liquid products used in construction include admixtures for improving concrete physical properties, asphalt cements and emulsions, traditional paint and coating products, and even pigments that produce the growing variety of mulch colors used in modern landscaping.
Each of these product types and countless others like them are originally blended in a variety of batch sizes and mixing processes. A common set-up might include an 800-gallon stainless steel mixing tank with a sloped bottom for better agitation, and a top mounted industrial mixer. This set-up allows for a wide variety of materials to be processed in large batch sizes. The mixer could be electric or air-powered to suit the preferences and utilities available. However, following the original production process, these products are distributed to the field for storage and use on or near a job site.
Intermediate bulk containers, or IBC totes, are commonly used for transportation and use on site. Their cubic shape makes them easy to store, and an integral shipping pallet base allow them to be moved with a forklift. But while the totes are well shaped for shipping, they are not ideal for mixing due their cubic shape. The most common volume is 275-gallons although they are available in other capacities as well. A 6-in. diameter plastic screw cap at the center of the tote’s top surface provides access to the products stored in the totes. While some products can be pumped directly from the tote for use, others have suffered product degradation while in storage. Suspended solids often settle and emulsion components can stratify such that the originally homogeneous product quality is lost. To restore liquid products to their original quality, distributors and on-site contractors utilize portable mixers. For IBC totes specifically, there are multiple designs that can be utilized. Selection is based on product properties such as density and viscosity as well as the degree of agitation required to produce the required results.
Portable mixer models can range from 1/2 to 2 hp - depending on the need.INDCO Inc.
Higher powered models are available for more intense agitation or for greater versatility; steel bracket mounts that span the top of the tote can be included for added stability.
Denser Materials Need More Torque
For mixing liquid formulations with higher density and solids content or overall viscosity, such as industrial polymers used in plastics or adhesives, epoxies, polyurethanes, zinc-rich primers and other commercial coatings designed for protection against the elements and corrosion, a mixer with greater horsepower and torque is recommended. To generate more torque these mixers are larger overall—including horsepower, shaft diameter, and impellers. Mixing impellers for these applications fold open so that they fit within the 6-in. opening but reach optimal size when extended during use. A common mixer for heavier, dense, viscous materials (up to 3,000 cps in an IBC tote), includes a 2 HP electric motor, and three 14-in. foldable stainless-steel impellers, mounted to a 1-in. shaft. Because the larger components weigh more, heavy-duty bracket mounts are normally used. Ergonomic toggle clamps easily adjust to attach to the tote cage and can be optionally provided with forklift channels or a lifting bracket for placement on the tote.
Materials used in commercial construction continue to evolve, as formulations are tweaked to include longer protection against the elements, or better corrosion protection, deeper penetrating dyes for mulches, and more. Many will continue to need mixing or stirring on site before usage to return the settled solids into a suspended state. As a general recommendation direct-drive models with smaller diameter single mixing impellers are suitable for low viscosity fluid mixing, those with viscosities similar to water or not more than a few hundred centipoises. However, due to the less-than-ideal cubic tote configuration and the limitation on impeller size by the opening, higher viscosities will benefit from higher horsepower, gear-driven models with multiple folding impellers and a mounting bracket for added stability.
When in doubt, confer with the mixer manufacturer as they should be happy to assist, and ensure that your selection has the torque needed for the application at hand.