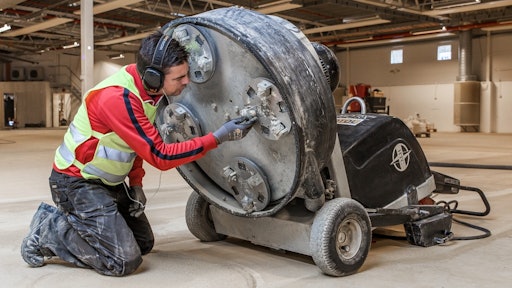
There are several levels of maintenance required for concrete grinders; daily, weekly, monthly and annually. Before we take a closer look at what should be done and when, remember, safety first. Use personal protective equipment when working on any grinder: safety shoes, eye protection, ear plugs, breathing mask and gloves are always a good idea. Make sure to disconnect electrical supply or unplug the spark plug cord when performing any kind of service or cleaning on a grinder.
Daily Care
Before using the grinder look at cables and hoses, paying attention to their general appearance, cracks, folds as well as plugs and connections. Replace any damaged cables.
Keep your equipment clean. After each use of the grinder, disconnect power and brush or wipe off dust and sludge (if grinding wet or using a built-in misting system). Tip back the grinder, remove tooling and wipe off the heads. Inspect plates and shroud, make sure screws and bolts are in place and tightened.
Check the tooling for uneven or abnormal wear. This may indicate the tool holder is damaged.
Check tool holder and grinding head for cracks or other visible damage. Replace any damaged parts. It is a good idea to use manufacturer’s original parts, as they are made to strict standards and hence higher quality. Pirate parts may be priced lower, but will not last as long nor perform as well as original parts.
If the grinder is equipped with remote control, make sure to remove any dust and residue from the radio control unit.
Weekly Maintenance
Weekly (or when needed), give the grinder a more thorough cleaning. Using a hose, rinse off dirt and grime. Use a soft brush and soapy water if needed. Spray the heads and plates hard with the hose to remove dirt and other build- up. Do not use a high-pressure washer, as moisture may penetrate electrical components and damage them. The machines drive system can also be damaged by high-pressure washing.
Check the grinding heads. After removing tools, tip the machine back and run in mid-air at lowest speed. Look for heads significantly wobbling or oscillating. If they are, they have been damaged and should be replaced.
Check for lower belt slip by leaning the machine back, grasp the grinding heads and try turning them toward each other. If you are able to turn them, a new belt is needed.
Check for upper belt slip by turning the large wheel in one direction or the other. If there is resistance the belt is OK, if it turns freely the belt needs to be replaced.
Several manufacturers offer belt change kits, containing all the parts needed for belt changes. This is a very convenient solution that will save many trips to the parts place, and free up time for productive use.
Self-propelled grinders use a separate battery for the drive wheel motor. This battery charges continuously when the machine is connected to power. Since batteries deteriorate with age, visually inspect the battery looking for leaks or cracks, and occasionally check the voltage. Replace it when needed.
Monthly Maintenance
Set aside time once a month for a more detailed look at your machine. This will help keep it in good working order.
When doing the monthly (or 100 hour) maintenance, inspect fasteners as they may come loose from vibrations and require tightening. Clean or replace the filter to the electrical box.
Check for lower belt slip by leaning the machine back, grasp the grinding heads and try turning them toward each other. If you are able to turn them, a new belt is needed.
Check for upper belt wear by tipping the machine back, grabbing on to one of the grinding heads and apply downward pressure attempting to rotate the drum without allowing the head to spin. If the drum turns, and the head does not, the upper belt is worn and needs to be replaced. Also check the seals on the shafts on which the upper belt runs. Replace if necessary.
Test run the machine in tilted back position, listen for any dissonance from the bearing. Replace them as needed.
If the grinder has a remote control unit, check the function of the STOP button, and check wear parts like the dust cover for damage or cracks.
Maintaining Propane-Powered Grinders
Electric motors require minimal maintenance, but if the grinder is powered by a propane engine, this needs additional attention. When working on propane engines, it is important to remember to bleed off the pressure on lines or valves before removing components.
Additives in the engine oil get depleted over time and with use, so to keep the lubrication effect it is important to change the engine oil at recommended intervals. Replace the spark plug when you change the oil. Disconnect the spark plug wire, remove the existing spark plug with a wrench or pliers. Make sure you use the right replacement plug, screw it in place without over- tightening, and reconnect the spark plug wire.
A clogged or dirty air filter puts added stress on the engine. Clean or replace the air filter once or twice a year. Let it air dry thoroughly before replacing.
Things to Keep in Mind When Servicing Grinders
For best results, always use original spare parts. To make sure you get the correct part, identify the part number when ordering. This is available in the spare parts list, which typically comes with the machine or can be found on line. On the grinders name plate you will find model name and serial number, which can help identify correct part if they have changed or been upgraded.
The electronics in remote control grinders are sensitive to electric shocks, so make sure to disconnect the radio receiver if doing any welding work near the machine or its components.
Finally, get a professional tune up once a year. All major manufacturers have authorized service shops, where maintenance, repairs or rebuilds can be done. And remember, it is never a bad idea to read the manual!
About the author
Brad Burns was the Technical Director at HTC Professional Floor Systems.