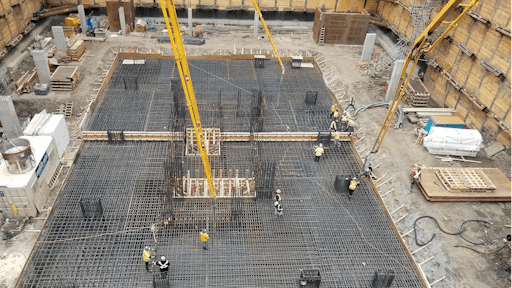
The thermal monitoring of concrete plays an important role in ensuring performance and avoiding early-age cracking. Often, this scenario involves a mass-concrete placement such as a building’s large foundation or piers for a bridge. However, soon the concrete in the country’s crumbling infrastructure will need to be addressed—funded by the billions set aside in the Infrastructure Bill—and careful analysis of the maturity can help ensure each placement reach its expected life.
Traditional ways of capturing temperature data from concrete can be time-consuming and labor-intensive. Despite the effort, it may be feasible to accomplish on smaller projects. But once the work is “ramped up”, these manual methods might just be as overwhelming as an interchange of freeways: projects like infrastructure, bridges, public transportation, dams, cast-in-place, or large precast products. And with labor being a tough issue to solve, two big questions are on many contractors’ minds: How can contractors automate more? How can contractors get more done with the same or fewer people than they are used to?
EXACT
Enter temperature monitoring systems.
Wanting to help, Korenzvit went into action and built a prototype of a wireless temperature logger to place into fresh concrete. This early model transmitted data online every 15 minutes and, as he puts it, “was game-changing for that project.” After a trial, he received a purchase order which launched a company.
“From there,” says Korenzvit, “we started hiring hardware engineers, software engineers, and put the team together.” They’ve now grown to a group of 33 people focused on providing technical data solutions for large users of concrete-like ready-mix companies, precasters, cast-in-place projects with various GCS, building infrastructures, high rise, and more.
EXACT’s concrete temperature technology collects data from the concrete in real-time and is analyzed online via a web portal providing contractors with actional decisions to build faster, safer, and more sustainably. “A huge amount of data that comes in and comes out with good answers about how to run the business better,” says Korenzvit. With a focus on providing products and solutions, he sees businesses struggling with labor shortages but solving the puzzle won’t be as easy as only polishing up the ‘help wanted’ sign. “It’s not a matter of throwing more people at the problem,” he says. “It’s a matter of working smarter with people. You have to get more done. If we monitor and match temperatures, we can get higher break strengths earlier and we can increase or decrease the number of shifts—there’s a number of things you can do through data analysis to achieve some of those goals and ultimately get more done.”
At first, they started with temperature; it was the only need in the beginning and remains to be a significant piece of data for today’s contractors – especially in the infrastructure space.
With the Bipartisan Infrastructure Law (BIL) signed in January 2022, the full impact of the $1.2 trillion investment has yet to be fully realized. Within the legislation, it’s reported:
- The US Department of Transportation has released $53 billion to modernize highways for FY2022
- The USDOT and Federal Highway Administration announced $27 billion in funding to replace, repair, and rehabilitate bridges across the country
- USDOT awarded $1 billion in Rebuilding American Infrastructure with Sustainability and Equity (RAISE) grants to invest in 90 major projects across 47 states
However, as of January 31, nearly $12 billion have been placed on hold pending final congressional action on the appropriations bills. Find more on what the BIL includes at ForConstructionPros.com/infrastructure.
“The Infrastructure Bill is a huge step forward in rebuilding the nation’s crumbling roads and bridges. The key to actually getting a 125-year service life this time around will be transparency on material performance,” says Korenzvit.
Temperature monitoring technology is able to interpret the data and project a concrete’s maturity or strength. In EXACT’s software analysis, they are able to provide real-time strength as information flows into the system. Beyond that, environmental temperature information can be captured and replicated in a testing lab allowing concrete test cylinders to behave in similar conditions. This, according to Korenzvit, ensures new concrete structures are cured right.
“Beyond that, there are many different modules on the software portal in terms of quality control, tracking, inventory tracking GPS locations, and particularly on precast pieces. And it's gone a lot wider than just temperature,” says Korenzvit. Aside from a sacrificial internal concrete temperature, EXACT’s products include sensors on humidity, moisture, hydrostatic pressure, strain, and more. Each is connected wirelessly with technology from IoT communications technology partner Soracom, ensuring an always-on IoT connectivity streaming data 24/7.
“With Soracom as our partner, we can focus on the data and delivering the longevity that these massive infrastructure projects require,” says Korenzvit.
EXACT
According to lifewire.com, WiFi routers operating on a 2.4 GHz band can reach up to 300 ft. outdoors, but construction sites can run a far greater distance. The temperature data packet being sent is very tiny—sending an update every 15 minutes. EXACT uses lower frequency, modulated radios to take advantage of better throughput and traveling capability. Korenzvit explains that sacrificial probes within the concrete are connected to a wireless logger—a construction site or precast plant would have multiple transmitting data over a lower frequency radio to a relay. That relay is then connected to the cloud with a Soracom SIM card. Depending on the scope of the project, he adds, the logger can be planted within the concrete.
According to Korenzvit, the logger’s battery lifespan should last from six months to up to two years on a single charge depending on the size of the battery. The gateway’s battery lifespan should be about a month and, if necessary, can be connected to a solar panel to keep it charged. Yet, even six months far exceeds the attention typically needed for a single concrete placement. Where the battery may survive for up to six months, it's common for contractors to only monitor the temperature for seven days. Afterward, the logger can be recharged and recalibrated for another project.
Saving Money
Almost any infrastructure project will likely include a crane—with that requires a large concrete pad for a base. Monitoring the concrete’s temperature would allow assurance of strength but could also save days off the schedule. Normally, explains Korenzvit, labs would start breaking test cylinders in four to seven days to watch the strength gain until enough PSI is obtained. Instead, EXACT Match uses the real-time data from the real concrete and mimic’s the environmental conditions in the lab.
“Those cranes are going up in three or four days, rather than seven to ten,” he says. “Right off the bat, right at the start of any project – high rise or infrastructure…they’re getting started faster.”
EXACT’s technology is also being utilized in projects like large-scale locks, cast-in-place bridges, and tunnels. Since the monitoring system was designed to be always online, alerts on concrete strength and maturity are always being sent to the cloud. This saves contractors the trip to the jobsite to capture data, saves the concrete from overheating because problems can be known, and saves the chance of signing a multi-decade bond to take responsibility to maintain the concrete – potentially a huge amount of money.
The important takeaway here, the communication technology has been taken care of so contractors can focus on the concrete at hand.
As plug-and-play as the device may be for the construction end-user, Soracom developed partnerships with a number of cellular network providers and a proprietary SIM card. While the customer may not be aware of the kind of connectivity technology used behind the scenes, explains Kenta Yasukawa, CTO and co-founder of Soracom, the company that built the product purchased the Soracom SIM card and integrated it into the product. For end-users (contractors), this allows them to open the box and get to work.
Operating behind the scenes, it's likely many are already using Soracom technologies without knowing. For example, Komatsu has reportedly been utilizing cellular connectivity to monitor its machines and sending information back to the worker. Additional examples include an advanced monitoring system with TOKU Systems for pressure-sensing devices for wells, tanks, and pipelines; a consumer pocket translator that connects to a cloud-based translation engine; ruggedized tire monitoring sensors logging tire pressure data of mining equipment with SST Wireless deployed in mines around the world; as well as within Nikon-Trimble's VISIONLINK transmitting telematic data from excavators.
EXACT
For a contractor placing the concrete for a bridge and utilizing temperature monitoring technology from EXACT, the SIM card would already be installed into the device/s. Putting this into perspective, as of January 2022, 4 million devices have been connected with the Soracom platform.
Odd Thought: If one considered concrete as the entity one is capturing data on (like one would for an asset in a fleet), could the monitoring of concrete’s temperature and maturity analysis with technology be considered a type of telematics?
But this isn’t the same scenario as a customer would receive from a cellular phone carrier—Soracom charges by byte received instead of a monthly rate. Considering the small size of the data packet being sent, this is great for a concrete temperature monitoring situation. Customers (in this case, EXACT) are provided a management dashboard to turn on/off SIM cards—one level of control but one that the contractor doesn’t have to manage first-hand.
Again, this is all happening in the backend. “For the concrete, construction sites, and monitoring concrete, we work with a company like EXACT Technology to be able to offer a solution so the construction workers are the people who manage the construction sites, they don’t necessarily have to know about Soracom,” says Yasukawa. “We enable EXACT Technology and enable construction workers and managers through them – that’s our model.”
Controlling Tomorrow’s Concrete Infrastructure
Concrete runs the risk of thermal cracking if temperatures are not managed properly in the first week of a new concrete placement. Thermal cracking can occur if the differential between the temperature of the concrete’s core and the surface is too high, or if the concrete overheats. These cracks could then allow water, salts and more to penetrate into the concrete, reach the reinforcement below and start to cause issues.
Over decades of research, today's academics and engineers have learned that maintaining proper temperatures within certain ranges can reduce or eliminate thermal cracking. “And if you eliminate thermal cracking, then you don’t have different things seeping into the concrete,” says Korenzvit. “As a result, you can have a much better chance of achieving the surface life—often 125 years for these concrete structures. There are very few concrete structures [built] from the middle of the century of the last century that are lasting that long. They all need a lot of remediation.”
EXACT
This technology can also control the application and heat (or cool) the precast beds as well. Korenzvit explains that through an acquisition done in February 2021, EXACT can add heat to the beds to gain strength quickly – essentially allowing the producer be proactive in their concrete’s maturity. “It's all part of the same kind of world of data temperatures and control. But now we're actually applying heat to these beds in a controlled manner.”
This can be done via steam, radiant systems, floor heating solutions, and boilers. However EXACT preference is to use electric. Korenzvit explains: “It's more sustainable and future-friendly. What we do is install specialized electric heaters on the undersides of the beds. We insulate the heaters in place so the electric heat and heat of hydration id directed back into the concrete. Then control the application of heat via our cloud platform…with very, very fine, granular control.”
This control can aid in further optimizing the mix by reducing cement content and admixtures in the concrete. “You don't have to necessarily add some extra chemicals to get those strengths in the right amount of time, you can often do that just by adding some insulation and the right amount to heat with a carefully programmed control system.”
Ultimately, Korenzvit remains optimistic for the future of construction and the concrete projects for the country’s infrastructure. “I'm pretty confident that we will achieve 125-year lifespans with a lot of the current projects going on,” he says. “As long as the people running those projects have good data and do things honestly and transparently.”