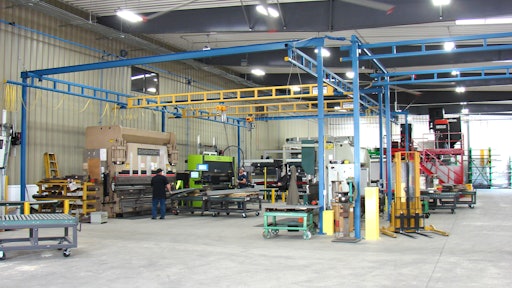
Felling Trailers Adds New Fabrication Center
In the time frame just a bit short of a year, Felling Trailers, Inc. has moved buildings, built buildings, acquired new technologies and moved existing equipment to streamline the production process and increase manufacturing efficiencies. All of this has transpired with the result of a state-of-the-art Fabrication Center.
In the fall of 2016 Felling Trailers worked with Thein Moving Co. Structural Movers to relocate existing Building 51 to make way for an expansion of the Main Warehouse to incorporate space for a new Fabrication Center. Over the 40 plus years of Felling Trailers’ existence, equipment and manufacturing space have been added as the company grew to meet demands of the market. The addition of the Fabrication Center is step-one of many in Felling Trailers’ goal to
The Fabrication Center now houses all three of Felling Trailers' press brakes. The Accupress Edge 250 ton press brake and Cincinnati CB-II 350 ton press brake were moved from the front production bays in mid-June with the help of Quick-Way Rigging of Minneapolis. This fall, Felling Trailers’ Marvel 2150 Vertical Band Saw and Hyd-Mech S23A horizontal band saw were moved into their places in the Fabrication Center.
The layout design of the Fabrication Center was based on the equipment used to complete the processing of fabricated parts. The key goals for the Fab Center were to: reduce non-value time inefficiencies, reduce the number of times material was being handled, increase safety and work environment comfort. The location of equipment was based on process flow. For example, the laser processes 30,000 jobs. Twenty-eight thousand of those jobs move on to the press brake, and from the press brake, the finished parts are placed on a conveyor cart where they are transported to a custom conveyor system to the warehouse side of the building. Once on the warehouse side, a sensor triggers a strobe light notifying the Material Handler to pick-up the finished parts.
"It's really about machine relation. The shorter the distance a part has to be moved during the process equals less time and movement that is required of the worker to complete the job. Flow is everything. A lot of the material handling solutions and concepts have been custom designed and made by our internal people. We are very lucky to have such a talented staff of custom fabricators,” said Chris Berg, Felling Trailers’ project manager.
"Worker safety is always a top priority. We have three Gorbel workstation bridge crane systems in place. These crane systems are a safe, worker-friendly solution for handling the large-scale material that we need to [handle],” said Berg.
A two-bridge crane system is used to feed the press brake for larger production part jobs, which reduces the chance of a lifting injury. The second crane feeds the laser parts sorting area reducing the amount of forklift traffic. The third crane system resides over the new saw conveyor system. This placement allows the saw operator to handle the longer, heavier parts while the saw is still producing parts. Worker comfort was also factored in regarding airflow and environment temperature. This was achieved by a combination of two 18-foot in diameter, SkyBlade HVLS (high volume low speed) fans and Reznor heaters for recovery when overhead doors are opened/closed. In warmer months, the fans can operate at a higher speed to move more air to create a cooling sensation and create a perceived temperature drop of up to 15 degrees. In colder months, the fans run at a lower speed to gently push heat generated by the heating units and equipment trapped at ceiling level back down to worker level with a draft.
Yanmar CE, ASV Become Yanmar Compact Equipment NA
Yanmar Compact Equipment North America (YCENA), encompassing the Yanmar Compact Equipment and ASV brands, finalizes its status as a single legal entity. The major milestone comes three years after the Yanmar Group acquired ASV Holdings, Inc. Now, the Yanmar Compact Equipment division in North America and ASV officially join to become YCENA.
“This is a huge step for us, our dealers and our customers,” said Tate Johnson, president of YCENA. “The alignment of the two brands allows us to focus on expansion, new products, and overall strategic growth in North America while finding new ways to serve our customers.”
Yanmar CE and ASV have operated as YCENA from a commercial standpoint since July 2020. The alignment as a single, legal entity allows for a better, more capable, and dedicated compact equipment entity focused on leadership in the North American compact equipment market. It will also allow a wider range of compact equipment offerings long-term, offer a single way for compact equipment dealers to do business with YCENA and strengthen the global Yanmar Compact Equipment team, the company said.
The Yanmar CE and ASV brands will remain distinct under YCENA with each brand retaining its product lines and dealer networks. Currently, Yanmar Compact Equipment offers mini excavators, compact wheel loaders and tracked carriers with a focus on commercial construction, residential construction, utility and rental applications. ASV offers compact track loaders and skid steers in the landscaping and forestry markets.
Ishee New President of FP2
Mark Ishee is the new president of FP2 Inc., succeeding Tim Harrawood.
Ishee is vice president, Pavement Preservation & Specialty Products, Ergon Asphalt & Emulsions, Inc., of Flowood, Miss. Harrawood is Southern Regional general manager for Vance Brothers, Conway, Ark. The position is a two-year term.
Ishee brings a strong background in asphalt emulsions to FP2 leadership. He's been employed with Ergon for the past 42 years, the last 39 of which have been with the Asphalt & Emulsions division. He has experience in many aspects of the emulsion industry, including plant operations and management, laboratory testing, research and development, field applications, troubleshooting, specification development and product marketing.
With Ergon’s support, Ishee also has worked with the asphalt emulsion industry at-large. From 2002 to 2006, he served on the board of the International Slurry Surfacing Association, including two years as ISSA’s technical director. He's been a member of the Asphalt Emulsion Manufacturers Association’s board since 2008, and served as AEMA president in 2017-2019. He wrapped up his extended term as immediate past president in February.Mark Ishee
His work with FP2 began around 2004, as a contributor of content, and serving on diverse committees and task forces. In 2011 his commitment increased as he worked with the FP2 steering committee charged with representing the industry on the successful pavement Preservation Group Experiment, a multi-year research project quantitatively measuring the performance of pavement preservation techniques, conducted by NCAT and later MnROAD. It was during this time he began his direct involvement with the board as a proxy representative, and was officially seated on the board in 2014. Mark was elected for terms as secretary/treasurer in 2018 and as vice president in 2020.