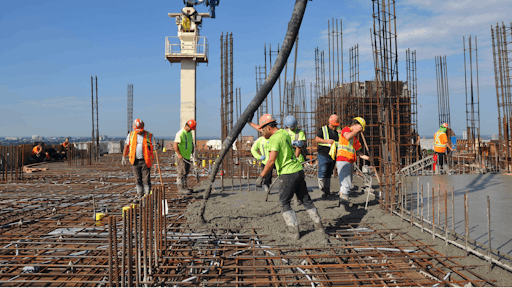
Summer can be the busiest time for the construction industry. Not only do the summer months provide the chance to get a lot done, but it also helps you avoid the challenges that come with cold weather concreting, like the freezing of concrete at early stages. However, hot weather concreting places several risks to the strength and durability of your mass concrete pour if adequate measures and calculated precautions are not taken to cool your concrete during the curing process. High ambient temperature, high concrete temperature, low relative humidity, and high wind speed—all of these are factors that could affect the quality of freshly mixed or hardened concrete which according to ACI 305.R10, could accelerate “the rate of moisture loss and rate of cement hydration, or otherwise [cause] detrimental results”.
Potential Problems When Pouring Concrete in Hot Weather
- Increased temperature may result in a higher early hydration process potentially affecting the strength at later stages (i.e. 28 days) affecting the durability.
- The concrete may fail to hydrate properly due to the lack of the presence of water, which could lead to the loss of strength as well as cracking.
- Increased rate of setting, causing difficulty with handling, compacting, and finishing, and a greater risk of cold joints.
- Increased tendency for plastic shrinkage.
- Increased difficulty in controlling entrained air content.
Those challenges can affect any type of structure built during hot weather conditions; however, additional considerations need to be taken into account for mass concrete elements.
What is Mass Concrete & Its Challenges?
Maintaining appropriate temperatures and temperature ranges within mass concrete is a key to maintaining its durability and longevity. Click the image to read about how to use temperature monitoring to meet a required specification.Giatec Scientific Inc.
From a temperature perspective, mass concrete has two main challenges:
- Ensuring that the core temperature does not exceed maximum temperature limits.
- Ensuring that the temperature differential between surface and/or edges (colder) and core (warmer) is maintained below a specific limit.
Both of those temperature limitations will be affected by ambient conditions and hot weather concreting.
Concrete generates a significant amount of heat as the cement gets hydrated. In a thin concrete element, such as a slab, that heat gets dissipated to the environment rapidly until it stabilizes with the environment temperature. In a mass element, typically 4 ft. (1 m) or thicker, that heat gets trapped inside the core (center) and will rise to high concrete temperatures. Because of the intrinsic concrete property to slowly dissipate heat, the concrete element will slowly cool down at its core. The concrete must be designed in such a way that the maximum temperature should not be higher than 160º F (70º C), unless otherwise specified by the engineer, based on pre-construction tests and the use of supplementary cementitious materials in the mix design. In any case, the concrete temperature must never reach over 185º F (85º C). Such high concrete temperatures would be detrimental in the long term and potentially cause delayed ettringite formation (DEF) which leads to significant concrete cracking. The heat rise (∆T, see figure 1 below) can be defined as the temperature gain in the concrete from placement until it reaches its maximum temperature.
Figure 1. The temperature of concrete over a seven-day period.Giatec Scientific Inc.
Hot weather concreting is going to play an important role regarding the concrete temperature at placement (initial temperature) and subsequently will affect the maximum concrete temperature as higher placement temperatures will lead to higher core maximum temperature. For example, a change in 10 ºF (5.5 ºC) in initial temperature will almost directly correlate to an additional 10 ºF (5.5 ºC) at the maximal temperature measured, which must be maintained below a certain limit.
Curing promotes the chemical hydration of the cementitious materials within the concrete. Click the image to read about how to manage moisture loss and temperature of freshly placed concrete.Giatec Scientific Inc.
- Pouring at night when it is cooler outside.
- Cooling water in the mix, or cooling the aggregates.
- Adding ice to the mix.
- Adding liquid nitrogen to the mix.
How Does Hot Ambient Condition Affect the Temperature Differential in Mass Concrete?
During the construction of mass concrete structures, tensile stresses and strains could emerge because of the difference between the temperature at the core and surface of the structure, and this difference is known as the “temperature differential”. These thermal stresses develop since the volume of the warmer region of the concrete expands while the cooler region contracts. The possibility of thermal cracking increases as the inner core of the mass concrete continues heating (hydration) while the outer surface of the concrete cools (heat dissipation).
The maximum concrete temperature differential should not exceed 35 ºF (19 ºC) during the curing process. Monitoring temperature differentials in mass concrete is essential for contractors and project managers to be able to prevent running into critical issues such as cracking, reduced service life, and project delays.
Figure 2. The temperature of the concrete at its center and surface as compared to the ambient environment.Giatec Scientific Inc.
In this case, high ambient temperature conditions might be in your favor. Since the concrete at the surface will be highly affected by the ambient condition, the concrete at the surface will be warmer (as illustrated in figure 2 above). Higher surface temperature will reduce the temperature differential between core and surface. Even though it might be easier to maintain smaller temperature differential limits in hot weather, it is still crucial to monitor the concrete temperature at both locations (core and surface) during the early construction phases to ensure that the limits are not surpassed.
About the authors
Sarah De Carufel, M.A.Sc., is the Manager of Engineering Solutions at Giatec Scientific Inc. where she utilizes her civil-engineering background to assist in the development of innovative products. She has over 5 years of experience in the use of technology in the construction industry and she brings this expertise to Giatec, the market leader in concrete testing technology innovation.
Keya Shirali is a Content Marketing Assistant at Giatec Scientific., where one of her responsibilities includes researching, writing, and publishing comprehensive content about various aspects regarding smart testing technologies in the concrete industry.