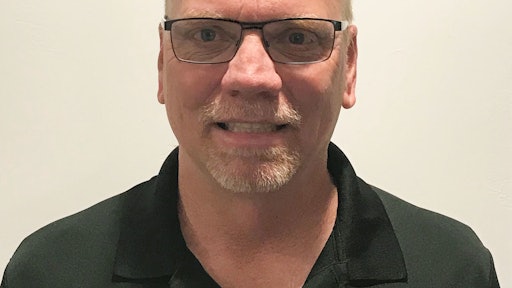
Safety is one of the biggest and most important considerations an equipment company should practice, preach, and prioritize. Fairchild Equipment, a material handling equipment dealer with locations in Wisconsin and Minnesota, who also serves the Upper Peninsula of Michigan, North Dakota, and northern Illinois as well, has taken that message to heart.
Founded in 1985 as Yale Materials Handling under the leadership of Gary Fairchild, Fairchild Equipment has grown from a five-person operation to having over 280 employees. They’ve added new manufacturers and brands to their portfolio, expanded their service areas to better serve the Midwest, and have established a strong company culture.
That culture is a big part of the company and who they are today. It encompasses visions and values such as Family Values (following the Golden Rule, a healthy work/life balance), Customers for Life (providing excellent customer service), Active in our Communities (being outstanding citizens), and Employer of Choice (happy and productive employees). It also mentions and prioritizes Safety Always, or being committed to safety always, no matter what.
Marty Schumacher, corporate safety manager at Fairchild Equipment, spoke with Rental to talk more about Fairchild’s safety culture and how that can be practiced properly throughout rental businesses and the industry as a whole.
R: Safety is one of Fairchild Equipment's top core values. How do you make it a priority within your company?
Schumacher: We promote safety at all times and in all places. What we mean when we say that is, we want our employees safe at work and at home, which we make a priority through training and our health and wellness programs. All our employees take the required safety training OSHA courses, and we even go above and beyond what OSHA requires. Our technicians are also trained and certified on the equipment they are working on.
To us, safety includes overall health too. We make being healthy a priority for our employees by having a health and wellness program. Employees are encouraged to participate, and they can be rewarded with a discount on their health insurance premium if they participate in our wellness program. We have company challenges such as being active or maintaining/losing weight where employees can accumulate points. The more points the employee earns in a year, the bigger insurance discount they can be eligible for. In the future, our plan is to get the employee’s family members involved in our wellness program too.
By having healthy employees, they are less likely to injure themselves at work or at home. That is why one of our top core values is Safety Always (we are committed to safety at all times and in all places), and it's so important because it reflects on our other core values (Family Values, Customers for Life, Employer of Choice, Active in our Communities, etc.).
R: Can you tell me more about your material handling solutions and OSHA-aligned courses? Why are they important for business owners and operators alike?
At Fairchild Equipment, we do more than just sell equipment; we partner with our customers to find the right solution to meet their needs and offer training to make sure they know how to safely use their equipment. We know safety is crucial to any company.
We provide OSHA-aligned courses for forklift training, aerial equipment operators, and in-house trainers. Our training ensures that your employees can safely and skillfully operate equipment from Hyster, Yale, JCB, Genie, JLG, and more.
We have forklift and aerial lift training classes that fulfill OSHA requirements for both initial training and refresher courses. Our certified in-house trainers that train our technicians and field personnel also offer training for our customers, both for operators and those who want to become a certified trainer to provide training themselves. The courses are designed around participants’ current skill level, the specific machine they will be operating, and any potential workplace hazards.
These courses are important for business owners and operators alike to ensure safety and that OSHA requirements are met.
R: What are the biggest challenges facing company safety practices today?
Keeping employees focused on the task at hand. With all the unsettling news today, it is more difficult for people to focus on what they are doing. A lot of attention is being focused on the new pandemic. Keeping employees from getting distracted and to keep them positive is the key to being safe.
R: What are some top safety considerations for rental business owners?
The main safety concern for companies that rent equipment is they need to be sure the employee operating the equipment is properly trained and familiar with operation controls. Because of this, Fairchild Equipment offers on-site operator training, and each rental unit is delivered with an operator’s manual. Fall protection might also be needed if the company is renting aerial equipment.
R: What are some questions customers should ask their rental houses in order to be prepared for renting a piece of equipment?
What is the down height and size of equipment? (To be sure equipment will clear doors.) What is the capacity? (How much can the unit lift and will the equipment meet the requirements for the job that it is being rented for?) What is the value of the rented equipment and what are the insurance requirements? (To make sure proper insurance coverage is in place just in case something happens.)
R: Are there safety tips that are particularly important for renting equipment during the winter months?
During the cold weather months, customers can request to see if the equipment they need is available with a cab and heater to protect themselves from the elements. Engine block heaters are common in colder climates. We recommend anyone who is looking to rent equipment for snow removal book early to ensure availability. Here are some additional tips for safe winter use:
- Train your team for cold weather conditions: A quick daily inspection can limit complications and ensure your equipment is ready to perform. Make sure your operators are educated on issues to look for during the winter months, so they can spot when machines require service and perform basic maintenance. In the winter, the elements can change quickly and so do the weather-related safety hazards.
- Adjust the way you operate: Engines take longer to warm up when it is cold outside, and roads are more treacherous when covered in ice and snow. Increase engine warm up times, always run the engine until it reaches operating temperature, lower travel speeds, and stay within the equipment’s reasonable capabilities to avoid situations that can result in downtime.
- Keep machines moving: Equipment that remains stagnant for too long during extended periods of cold can be negatively impacted. Machines that are less frequently used during the winter months should be started up on a regular basis and put through a basic series of movements and functions.
- Clean your equipment: Machines are susceptible to salt and other chemicals after it snows that can contaminate systems and cause erosion. Regular cleaning of equipment will not only protect the body and components, but it will also help you spot issues that may be affect the machine’s performance.
R: Now that we're in the midst of a global pandemic with COVID-19, there seem to be new safety concerns for business owners. What are some of these newer concerns, and how can they be managed/handled moving forward?
The biggest concern is not to have our employees or our customer’s employees get sick and spread any communicable disease. At Fairchild Equipment, we disinfect equipment with active microbial cleaner, which disinfects and knocks down germs and bacteria, and equipment is sprayed down before it is delivered to the customer.
We also offer the option to pick up customers’ equipment and repair it in our shop to help with concerns customers might have with subcontractors in their facility. All equipment is sprayed down before it is picked up and returned to Fairchild Equipment shops, and then again, before it is returned.