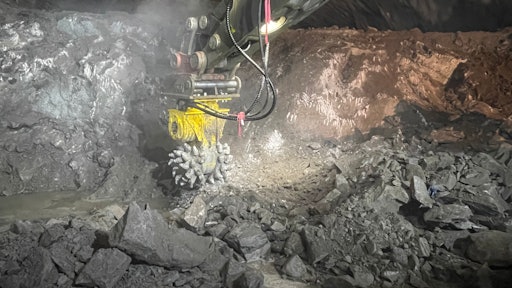
According to Common Ground Alliance’s Damage Information Reporting Tool (DIRT) report, more than 233,810 utility damage events were reported in 2022. The primary causes of these events were digs that occurred without calling 811; a lack of maintenance, including pothole fills; and the inability to locate issues because of incorrect or outdated maps.
Contractors, particularly those who undertake digging, must be mindful of each hazard posed by utility strikes. After all, damaging underground infrastructure can lead to more than just cut lines, especially as contractors work around gas pipelines.
“That’s why the construction industry emphasizes the importance of calling 811 before digging begins so that existing utilities can be located and marked,” said Jake Jeffords, director of sales, marketing and global accounts, Vermeer MV Solutions. “Contractors should also verify digging locations themselves while using their own utility locator and potholing and daylighting all nearby utilities in their path. The construction industry’s preferred method for doing that is soft digging while utilizing vacuum excavators.”
Aside from these three primary causes of utility damage, contractors must remember another aspect of the hazards associated with underground utility construction and repair: the U.S.’ overall underground infrastructure has become increasingly complicated during the past few decades. As a result, several networks of utilities—from electric and telecom cable to gas, sewer and water pipelines—constantly crisscross at different levels below the ground.
Because of this congestion, whenever utility workers dig or bore into the ground, a utility strike or a cross bore may occur. Not to mention, underground interference may increase too, thereby ensuring that proper locating is necessary on contractors’ jobsites, according to Chris Thompson, vacuum excavation product manager, Ditch Witch.
Furthermore, contractors must look out for falling rocks from walls and overhead as they conduct underground utility construction and repair tasks. Unwanted water may also enter areas at times, while cracks may occur in rock floors. Finally, according to Tim Schutte, product and application specialist, Epiroc USA LLC, contractors might encounter insufficient ventilation, too.
“To ensure contractors have air that’s as clear as possible, underground gases must be removed as soon as possible,” he said. “By overcoming these critical hazards, contractors will be able to safely work to the best of their abilities as they oversee underground utility construction and repair tasks.”An operator is photographed while using Ditch Witch's Subsite Marksman HDD guidance system on a jobsite.Ditch Witch
The bottom line is this: Hazards can—and will—vary considerably on underground jobsites. In turn, contractors never know exactly what they’ll find or, at times, exactly where the hazards are. As a result, according to Justin Steger, solutions marketing manager, John Deere, it’s crucial for locating services to mark any hazards they can find, whether they’re conducting new construction or repair services.
“Contractors still have to be careful though, as locating services are never pinpoint accurate,” Steger emphasized. “Safety is a critical component of locating services’ offerings, especially when they’re as accurate as possible.”
He continued, “To ensure safety, particularly on repair jobsites, locating services can locate and mark existing utilities so that operators will know when they’re getting close to pipes or fiber [that] they’re either interested in repairing or trying to avoid, leading to a lower potential for injuries and a decline in downtime.”
Utility Locating Devices Assist Contractors
As the landscape of underground construction and utility inspection continually changes, digital documentation has become a vital tool for underground construction professionals. For example, more professionals are using the most recently released utility locating devices to automatically acquire data in real-time—and with centimeter-grade accuracy—whether they’re conducting pre-drill planning or comprehensive post-drill reporting. And, according to Thompson, as the latest devices locate utilities, they can also map and label each one, thereby building a digital record that can be shared locally or on a cloud-based mapping service.
“While using a horizontal directional drill (HDD) guidance system, a drill operator, in particular, can download a bore plan and see it overlayed on their guidance display,” Thompson said. “This can help them stay on course, with regards to their plans, by monitoring critical waypoints as they drill.”
In addition, the system can log bore data in real-time. As a result, as drill operators are in the field, they’re able to download data to their computers, smartphones and tablets, to review a profile of each of their drills before comparing each profile to their specific drilling plans.
“This data mapping technology is critical for the future of underground construction and utility inspection [because] it enables operators to streamline data sharing and access shared information quickly,” Thompson added.By using the latest utility locating devices on the market, alongside integrated data mapping, operators can mitigate damage on their jobsites more effectively than they have in the past.Ditch Witch
By using the latest utility locating devices on the market, alongside integrated data mapping, operators can mitigate damage on their jobsites more effectively than they have in the past. Additionally, since the most recent devices often have enhanced receivers, operators and their fellow crew members can locate utilities with centimeter-grade accuracy. In turn, their overall planning processes become more efficient and simplified.
“And because all data is recorded and managed digitally, rather than manually, the risk of errors will decline too,” Thompson explained. “After all, when a bore or a dig is planned while using advanced data and digital mapping, crews will face fewer risks of human errors, as they’re more likely to safely navigate complex underground environments.”
As an example of utility locating device innovations, Vermeer recently introduced its Verifier G3+ utility locator, which offers contractors assistance as they verify utility locations. A new-generation locator, the Verifier G3+ provides accuracy, connectivity capabilities and intuitive controls. The locator can be paired with smartphones. While using the G3+ Map mobile app that’s available for Android and IOS, the Verifier G3+ helps contractors plot location information—ranging from the current index, depth and device name, to GPS data to operators who have conducted job tasks and utility type.
“Due to the Verifier G3+’s data capturing ability, contractors and utility owners can capture and store information about construction projects,” Jeffords said. “And, in doing so, they can provide more information to their team members and customers than they previously could.”
Excavators, Backhoes & Technology Innovations
At the same time, Vermeer has also released a vacuum excavator, known as the VXT300. Featuring an 8-cubic-yard spoil tank and a 6-inch dig tube, the excavator can carry up to 800 gallons of water, thereby helping crew members enhance their overall on-the-job productivity. Lightweight, one of the lightest truck vacs in its class, the VXT300 has a low overall height (11.5 feet) too, enabling operators to effectively transport spoils from their jobsites to dumpsites.
“Developed for utility contractors that are working on projects in which several holes have to be dug, the midsized PTO vacuum excavator has been created for drilling crews that utilize large volumes of drilling fluid as well,” Jeffords said. “Of equal importance, it’s also a great fit for municipalities and contractors that are working on sites that only allow for soft digging methods, such as data centers and solar farms.”Featuring an 8-cubic-yard spoil tank and a 6-inch dig tube, Vermeer's VXT300 vacuum excavator can carry up to 800 gallons of water, which helps crew members enhance their overall on-the-job productivity.Vermeer MV Solutions
For contractors that must conduct job tasks involving sewers or water, they’ll generally use backhoes instead. Or they may even prefer to use excavators, along with multiple attachments, to complete their tasks. To provide technology for backhoe users, John Deere Construction & Forestry recently released its G-Tier and P-Tier backhoes.
“Our 310 G-Tier, for example, is a rugged, reliable machine at a lower price point than some of our other offerings, as it has fewer options and features,” Steger said. “Yet, it still provides the performance and reliability that John Deere equipment has become known for.”John Deere Construction & Forestry's 310 G-Tier offers users high performance, along with cost effectiveness.John Deere
To compare, the manufacturer’s P-Tier backhoes offer operators more features and options, as well as higher performance than its G-Tier backhoes. As an example, the 320 P-Tier, a new offering, provides higher horsepower (a net peak of 113) than the 310SL model it has replaced. Moreover, it offers a heavy lift option, leading to a higher lifting capacity, which is ideal for the frequent setting of heavy underground structures, including manholes.
“The 320 P-Tier also provides automatic ride control for a more comfortable ride during transport and load and carry operations,” Steger stated. “At the same time, it has a lift mode, resulting in increased hydraulic pressure [because] craning—with backhoes—occurs.”
Furthermore, it has a precision mode that diminishes hydraulic flow as operators place structures and pipes carefully, or as they dig around existing utilities, thus ensuring it’s a highly manageable and predictable machine as well.With the 320 P-Tier’s, operators can overcome issues associated with underground jobsites, including congestion, continuous changes and obstacles.John Deere
“Our P-Tier excavators are great when they’re used underground too, as the 210 P-Tier, 350 P-Tier, 380 P-Tier and 470 P-Tier each offer a range of grade management solutions with valuable underground features,” he added. “For example, they feature 2D Guidance, 2D SmartGrade Ready Control or full 3D SmartGrade Control, while also enabling users to upgrade the technology offerings without requiring them to purchase new excavators. Each grade management solution is compatible with (or without) laser catchers, too.”
In the meantime, 2D SmartGrade Ready Control, along with all other SmartGrade offerings, for that matter, provide overdig protection too, which hydraulically restricts excavators. Therefore, they won’t dig deeper than operators’ set points, and over excavation will be prevented, resulting in time savings, as rework won’t need to occur. Bedding material costs will decline as well, while operators will also be able to “get to grade” accurately and quickly the first time they need to—all within a tenth of a survey foot.John Deere Construction & Forestry's P-Tier excavator lineup, including the 350 P-Tier, offers operators grade management solutions.John Deere
“SmartGrade offerings, including 2D SmartGrade Ready Control, have virtual fences too, allowing operators to set, adjust or turn off left, right and upper limits, in order to manage dynamic jobsite obstacles,” Steger said. “As an operator approaches one of these obstacles, the excavator will alert the operator, yet it won’t be stopped while doing so.”
As a result of the 320 P-Tier’s offerings, operators can overcome many of the key issues associated with underground jobsites, including congestion, continuous changes and several obstacles, whether they’re in the ground or around the trenches in which work is being conducted.
“Backhoe features, like lift mode, enable the 320 P-Tier to be more capable, while precision mode ensures that it’s easier to operate around obstacles,” Steger stressed. “Excavator features, such as any of the grade management solutions, either provide reference or exact elevation feedback, resulting in less frequent manual grade checking. Consequently, less manual labor needs to check grading in trenches or trench boxes, allowing managers to repurpose their employees elsewhere on their jobsites so that job tasks can be completed faster and more safely.”
Drum Cutters Enhance Operators’ Safety
Often, operators will need to implement blasting to loosen very hard rock, while using tunnel boring machines (TBMs) on a large scale. As operators conduct blasting and use TBMs, they must also scale ceilings, floors and walls to remove potentially dangerous, loose materials. To do so in an accurate and safe way, they can use Epiroc ER and VC drum cutters as they trench and scale.
One benefit of the VC double drum model is that it doesn’t have to move side by side. This allows operators to dig various trenches, including those with flat bottoms and straight walls. If operators need to conduct job tasks for narrow trenches, they can use Epiroc’s ER L model instead because it has a single drum or cutting wheel, which can be installed on each of the manufacturer’s ER models. For further flexibility, each of the double drum offerings can be installed on every type of carrier, too.
“At Epiroc, we can offer numerous attachments that ensure underground mining occurs properly, leading to employee safety as well,” Schutte said.By using Epiroc's VC double drum model, which doesn't have to move side by side, operators can dig different trenches, including those with flat bottoms.Epiroc
Using drum cutters like the ER and VC, operators will be protected in another significant way: they won’t have to use hand tools. In fact, they won’t need to use any tools that may leave loose rocks on ceilings and walls, each of which can be dangerous.
“Our drum cutter products will accurately and safely remove loose materials on ceilings and walls,” Schutte added. “And, just as importantly, they’ll enable operators to cut or profile materials with minimal vibration, ensuring that cracks or fractures in materials on ceilings, floors and walls aren’t added, resulting in even further safety down the road—and, in turn, a decline in downtime, as well as the costs associated with it.”
Trenchless Equipment Benefits
Aside from using techniques like blasting on the job, operators can also implement trenchless installation methods, such as horizontal directional drilling, especially if they’re conducting construction and repair activities for utilities in suburban and urban areas. By using trenchless equipment, they can minimize their restoration efforts and traffic disruptions while ensuring that property owners are pleased with everything that is occurring.
“Boring a utility line is often more cost-effective and requires less time since it goes under roads and sidewalks, rather than through them,” said Clint Recker, product manager for trenchless products, Vermeer. “Additionally, above-ground obstacles, such as driveways, fences, roadways and sidewalks, are no longer a concern.”
As contractors determine whether they should trench or use an HDD, the location must be considered.
“In urban areas, there are typically more above-ground obstacles that contractors have to account for,” stressed Ed Savage, product manager, Vermeer Corporation. “So, the usage of trenchless installation methods, like horizontal directional drilling, auger boring and piercing tools, tends to be more efficient than cutting through hard surfaces and then repairing them.”
Rural areas, on the other hand, have fewer road intersections or other obstacles to be concerned about. Trenching or using a vibratory plow is typically easier in these areas, rather than using an HDD alone. HDDs are still often used for road and river crossings.
In addition to location, contractors must bear in mind ground conditions, installation depth and utility bundle size because each factor influences the sizes of the HDDs, trenchers and vibratory plows used on the jobsites.
“For example, if contractors are installing small-diameter electrical or fiber lines at shallow depths in soft soil conditions, vibratory plows are likely their best options,” Savage emphasized. “However, if they’re installing larger distribution lines at depths of more than a few feet, they’ll likely need to choose midsize trenchers instead.”
If contractors are conducting installations in rock or installing large diameter products at depths of more than 5 feet, they should consider using a higher horsepower trencher instead—particularly one that has a large boom and chain configuration that enables them to cut a trench at whichever width they need to.
“One more consideration that can influence the decision between HDD and trenching is equipment availability,” Savage added. “Unlike directional drills, trenchers are typically available at rental stores. Renting can be an attractive solution, particularly if contractors only have a minimal amount of products that they need to install.”
Options Improve Operations
In conclusion, a variety of technology offerings and equipment options—from utility locating devices and excavators to backhoes and drum cutters—allow contractors to conduct underground utility construction and repair tasks more effectively and safely. Not only will productivity rise, but downtime will diminish and injury risks will decline.
Employees will be more effective, employers’ bottom lines will increase and a significant figure (217,000 utility damage events) will potentially begin to decrease as a result.
Now is the time for underground utility construction sites to implement these technology offerings and equipment options to witness their positive influences firsthand, preferably sooner than later.