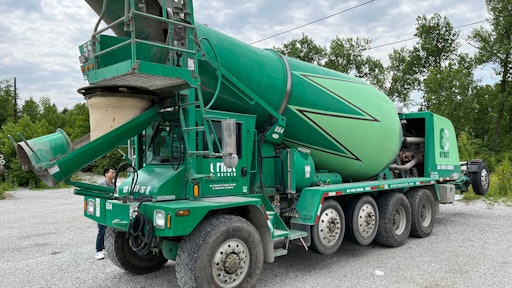
Summer is tough on tires, especially when those tires are hauling a heavy load, like those on the Terex front discharge mixers that Ernst Concrete uses. When empty their Terex front discharge mixers weigh in at 33,500 pounds – loaded it tips the scale at closer to 70,000 lbs. Tires that were properly inflated that morning can pick up debris on the construction site and lose air throughout the day. Run flats were causing headaches for Fleet Manager Mike Jones.
In addition to the schedule disruptions and delays caused by roadside tire service, there is the potential to ruin a fresh batch of concrete, and the out-of-pocket costs. A tire monitoring program is helping to eliminate the run flats and all of the problems associated with them, saving Ernst time and money, while improving their service.
Ernst Concrete operates roughly 350 front and rear discharge mixers from their 43 locations across Ohio, Indiana, Kentucky, and Georgia. They’ve been in business for over 75 years, so dealing with summer heat and its issues is nothing new to them.
“The biggest issue we were having was run flat issues,” recalls Jones. “Drivers would run on low tires, and when we changed out those tires or when we turned them in for credit they would be junked because the cords inside were broken.”
With the cost of a new tire close to $1,000, and casing credit of $200, every trashed tire was costing Ernst $1,200. Jones suggested that they try the Doran tire monitoring system in a single Kentucky location.
“When we put the system in, we went from seven run flats to zero. As many tires as we go through a year, that was a huge savings for us,” says Jones
Armed with these figures, Jones approached upper management with the idea of rolling it out fleetwide. The initial decision was to let each location general manager decide whether to implement it or not. A few decided to, and the results were impressive enough to warrant implementation across the whole company.
In addition to eliminating run flats, and saving those associated costs, Jones credits the Doran system with shortening their response time to incidents. “It’s a proactive system. Instead of waiting for the tire to go down completely, and then pull over, drivers can alert maintenance that a tire is going down,” says Jones. “If we can’t get to them right away, we automatically dispatch a tire company to them. The response time has decreased a lot because we know what’s going on.”
Terex
How it works
Monitoring temperature is important, because even if a tire is fine, but a brake is sticking or a wheel bearing is going bad causing the temperatures to rise, the system will alert the driver. This is important because the belts inside a tire can separate from the rubber at around 200° F, creating a safety issue for unsuspecting drivers and those in their vicinity. Doran tire monitoring system monitors tire pressure and temperatures on all connected tires, then alerts drivers when tire temperatures reach 175° F. If a tire reaches that temperature, the driver will receive a visual and audible warning on the in-cab display which then allows them to find a safe place to pull over and lets their tires cool off and avoid a catastrophic event.
A Look Inside
External, valve stem-mounted sensors pass tire pressure and temperature data to the in-cab monitor/display, providing drivers with real-time information and alerts. Doran 360 tire monitoring systems include visual and audible alerts for low inflation pressure, rapid deflation events and high tire temperatures. Drivers can see which tire is impacted and exactly what is going on with it.
Ernst Concrete
“When they’re working in the yard, they dig into the piles, then back out and turn to offload,” says Jones. Stooping into the piles can raise tire temps. “We were seeing elevated temperatures in the loaders, especially the left rear loader tires. The operators adjust how they attack the pile, and we’re seeing a lot less tire wear.”
That is another substantial cost savings opportunity because the tires cost $2,300 to $2,500 a tire. “That’s a huge savings if we can extend the life of that tire,” said Jones.
Doran
Jones attested to the ease of installation, saying “Most of our shops are one man deep, and they can do it by themselves. For the most part its simple to install, the longest part is calibration.”
Initial installation may take two hours or so, but technicians can typically accomplish an install in an hour to an hour and a half per ready-mix vehicle.
Despite the summer heat and constant threat of hazards at virtually every job site, Ernst Concrete is better at managing their tire program with Doran. Monitoring and continually reporting tire pressures and temperatures allows Ernst drivers to communicate with the maintenance teams to schedule repairs and corrections. That is shortening service call response times and improving their customer service. Proactively monitoring tire inflation pressures helps to reduce tire-related maintenance costs, extend tread life, protect casings, and minimize catastrophic tire failures.