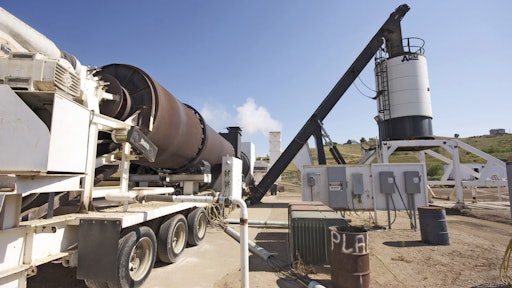
Based in Pierre, S.D., Morris Inc. has something for everyone. Since 1970, this construction company has grown into a full-service highway-heavy-utility business. Among the services it offers is producing a wide variety of concrete and asphalt aggregate products, along with its own asphalt plant, which is ideal for all types of asphalt projects throughout central South Dakota.
Founded by Milton Morris, the company got its start as Morris Irrigation, with just a few employees servicing irrigation systems for farmers in central South Dakota. From there, the company expanded its services to include installation of pivot irrigation systems. In the 1980s, Morris added a concrete Redi-Mix plant and began installing sewer, water and utility services. And in the 90s, it got into the aggregate mining and asphalt production businesses. Since the beginning, Morris has prided itself on safe, timely and efficient work.
The asphalt division of Morris started with the purchase of a used 100-tph asphalt plant. Despite its lower capacity, the plant kept up with most of Morris’ needs, due to the limited number of large projects in the area. “It’s kind of hit and miss being out here in the middle of South Dakota,” said Chris Boom, Morris estimator/project manager. “So we do a lot of specialty work that requires 25,000 tons of asphalt or less. We do highways, streets, parking lots, driveways and airports — pretty much anything that we can find.”
One of the main challenges the company faced with its first asphalt plant was becoming familiar with the aggregates in central South Dakota. “The aggregates in central South Dakota are durable and sound, but the pits vary in quality. Some pits are high in shale and lightweights, but with our ability to wash and jig the material with our Allmineral jigs, we are able to remove the lightweights and shale to produce top quality asphalt and concrete aggregates that can be used on state and federal projects.
Growing into highway work
Eventually, the market picked up around Pierre, and Morris required a new plant so it could bid on highway jobs. “We needed a bigger plant to get more competitive on state projects,” said Boom. So, after doing some research, the company more than doubled its capacity by purchasing a new 220-tph RoadBuilder plant from Asphalt Drum Mixers (ADM).
RoadBuilder asphalt plants are available in portable and stationary versions with capacities ranging from 110 to 350 tph. They feature a parallel-flow drum that uses ADM’s unique flight design to move moisture-laden aggregate in a rotating veiled pattern away from the burner. The fuel-efficient burner produces the dryer flame, which is shaped to minimize asphalt cement burn-off, resulting in cleaner emissions.
Although Morris keeps its work close to home, the company decided to purchase a portable RoadBuilder plant, which allows the flexibility to move when a good opportunity arises. “We try to stay in the central part of the state,” said Boom. “We maybe move once or twice a year.”
Over the last several years, the company has also added multiple components — some of which Morris fabricated in its manufacturing facility. “Over the last four to five years, we’ve made our own crushing equipment and other components,” said Boom. The plant now includes oil tanks, a 50-ton self-erecting silo, a scrubber, and one of its latest additions — a recycle system that Morris built.
Today, Boom achieves a better asphalt mix than he experienced with his previous setup. Not only has the new plant played a role, but the aggregate quality has also increased significantly over the last 10 years. “Ever since we’ve had this plant, the quality has been excellent,” he said. “We don’t have trouble with the plant or aggregates like we used to.”
When the plant does require service, Boom typically finds the issue to be a quick fix, thanks to the use of off-the-shelf-parts and an overall simple product design. “The parts are easy to get, and ADM’s service is excellent,” said Boom. He is also impressed by the top-notch support received when adding new components. “Even when we built our own recycle setup, ADM sent a guy to tie it into the computer and help get us going.”
Still upgrading for success
Since buying the new plant, Morris has produced between 65,000 and 100,000 tons of asphalt per year. This year, the company is projecting to reach the higher end, thanks to a sizeable state project on highway 14B, a truck route that goes around Pierre. The project kicked off in May 2012, and the scheduled completion date for the paving work is the end of August. It is welcomed after the company experienced a slow 2011, when dramatic flooding from the Missouri River caused operations to come to a halt. “This is the biggest highway project we’ve had in two years,” said Boom. “It’s right at 25,000 tons of asphalt, and it will put us closer to 100,000 tons for the year.”
In addition to producing asphalt for its own projects, Morris sells to other entities as well. “We sell a lot to the state, cities and counties as patch mix,” Boom said.
Overall, Boom is extremely pleased with how the plant has functioned in his operation. It fits well in the Morris line of companies, as it allows them to offer one more service to its customer base in central South Dakota. Furthermore, the ADM team that Boom has worked with seems to maintain the same commitments to integrity, quality, relationships and success that Morris has embraced for more than 40 years.
However, the company isn’t finished upgrading its asphalt plant setup. In fact, Boom plans to eventually replace the parallel-flow drum of his RoadBuilder with a new counterflow drum. This would allow him to use a higher percentage of RAP in his mixes. “We’ve used up to 20 percent RAP, which is at the top end for a parallel-flow drum,” he said. “The more you can use, the better. Counterflow technology is where things are going.”
Although the upgrade to a counterflow drum will allow Boom to use more RAP in his mixes, he will face the challenge of finding more to use. “RAP is scarce in this part of the country because a lot of people hold onto it,” he said. “Trying to get people convinced to not use it as gravel has been a challenge, but it is getting better.”
Coincidentally, ADM recently released a new line of portable and stationary counterflow plants, the EX Series. With capacities ranging from 100 to 425 tph, these plants are able to meet the needs of both large and small operations. The single-drum design allows contractors like Morris to incorporate as much RAP as mix specifications allow.
Even with the switch to a counterflow plant on the horizon, Boom is certainly satisfied with the production he has experienced with the parallel-flow drum. And though he’s not prepared to make purchase decisions yet, he said, “I’ve been really happy with ADM, and I don’t see any reason for changing.”