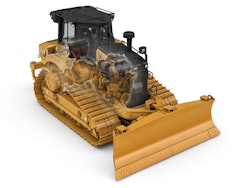
Today’s crawler tractors have become technological marvels. Automated grade control functions simplify operation and allow novice operators to proficiently hit grade, while advanced drivetrain technology cuts fuel consumption, and production data is transmitted to the office in real time.
“As technology evolves at a rapid pace, it is becoming more relevant in the construction industry, and dozers are no exception to this,” says Matt Goedert, solutions marketing manager, John Deere Construction & Forestry. “One of the biggest struggles facing contractors today is finding and retaining skilled operators. John Deere is developing several features to help overcome this challenge.”
Simplified grading technologies help operators perform basic grading tasks. “While the adoption of 3D grade control systems has been significant over the last 5+ years, there is still a place for entry-level grade control technology to grow adoption and simplify tasks,” says Goedert. “Over the last couple of years at John Deere, we have launched Slope Control on many of our dozers, including the 450K, 550K, 650K, 700L and 750L models. Slope Control fills a need for less complex technology which doesn’t use a 3D model or external reference, such as a base station or laser, while still automatically controlling the blade for the operators.”Over the last couple of years at John Deere we have launched Slope Control on many of our dozers, including 450K, 550K, 650K, 700L and 750L models. Slope Control fills a need for less complex technology which doesn’t use a 3D model or external reference such as a base station or laser while still automatically controlling the blade for the operators.”John Deere
Machine control of slope allows the operator to concentrate on efficiently moving the dirt instead of on maintaining grade. “The operation of slope control is extremely simple and gives the operator a choice between two operating modes: target and joystick mode,” notes Goedert. “Target mode allows operators to define a cross slope and main slope for the blade to automatically maintain, while joystick mode allows the operator to make manual blade corrections and the system will maintain the slope of the last operator command. The slope can easily be flipped by the operator when turning the machine around.”
This provides added flexibility. “This entry level technology puts another tool in the operator’s box, enabling simplified operation in many applications,” says Goedert. “Slope Control helps operators and jobsites maintain drainage throughout the job, whether you’re grading an area to stage equipment or quickly grading the site before a rainstorm arrives.”
Slope Control can be easily upgraded to SmartGrade at any time. “SmartGrade is John Deere’s integrated mastless 3D grade control system and has added features, like Auto SmartGrade that allows operators to dial in specific settings like load levels, material types and dozing activities,” Goedert explains. “This system automatically controls the blade to reduce track slip and boost productivity.”
The Road to Autonomy
The road to autonomy will start with semi-automated functions such as automated slope control. “Depending upon how you define semi-autonomous, I would argue that we are there today with grade control,” states Sam Meeker, market professional at Caterpillar.
Caterpillar offers a suite of features on its current generation dozers including:
- Cat Grade with slope assist, which maintains a pre-established blade position without a GPS signal;
- Stable Blade, which works seamlessly with operator inputs to help produce a smoother surface;
- traction control to automatically reduce track slip;
- and AutoCarry, which automates blade lift to maintain a consistent blade load.
“All of these features are designed to help the operator do his job a little bit easier, maybe a little bit faster, with a little higher quality output,” says Meeker.
While these tools are beneficial to novice operators, they also bring your best operators to a new level. “The good operators are always going to be the ones that figure out how to use the tool the best,” says Meeker. “They’ll take grade control and figure out how to make it even better and make their life even better, make their job easier and at the same time be more productive.”
One key to being able to utilize these new technologies is an intuitive user interface. Caterpillar currently uses a 10-in. touchscreen on many of its crawler dozers. “It’s not a two-line LCD display anymore,” says Meeker.
The full graphical displays run on an Android OS platform. “It’s very similar to what a customer is using in their smartphone. It uses the same type of gestures — the pinch to zoom, push to select and push and hold to edit,” Meeker explains. “Just having a good, consistent menu structure that makes sense throughout the system helps operators as well.” By pushing the question mark on the screen, basic functions such as Slope Assist or traction control are explained in detail, with graphics, for the operator.
Remote machine control has also been a focus for Caterpillar and is starting to gain traction. “I’ve been really impressed with the amount of interest there is on remote control,” says Meeker. The advantages include opening up the workforce to more potential operators and increased safety by not having people in dangerous situations.
The Liebherr Operator Assistance Systems (OAS) offers three levels – Free Grade, Definition Grade and 3D Grade for 1D, 2D and 3D applications. Free Grade assists with creation of flat surfaces, ramps and dams. Definition Grade is for basically modelling of 2D surfaces. It operates without additional equipment such as GNSS receivers or base stations and provides automatic position control of the blade to a specified target inclination. 3D Grade offers automated six-way blade control for exact blade positioning to create 3D site models.Liebherr
Free Grade is active blade stabilization for free/creative grading. This assists with creation of flat surfaces, ramps and dams. Definition Grade is for basic modeling of 2D surfaces. It operates without additional equipment such as GNSS receivers or base stations and provides automatic position control of the blade to a specified target inclination. 3D Grade offers automated six-way blade control for exact blade positioning to create 3D site models.
The Liebherr OAS is controlled by a 9-in. touch display that allows the operator to fine-tune dozer operating parameters such as responsiveness of work hydraulics, responsiveness of drive hydraulics, ECO mode, automatic speed reduction and engine shutdown.
Komatsu has also expanded to level of automation possible with IMC 2.0 integrated machine control. The company added more features into the suite, now the Komatsu crawler dozers can use automatics from grass to grade.
Bulk earthmoving accounts for the vast majority of most projects. “When you get a new operator, if they are only using automatics when they get to the final grading, that means they are still having to work manually for all the other operations stripping the soil,” notes Jennings. This amplifies any deficiency in the operator’s skill level. “Now, with 2.0, they can use automatics when stripping and really focus on the job, learning what they are doing.”
A key feature that enables Komatsu’s automation is proactive dozing. “As you move the machine over the jobsite the first time, it’s reading and learning that terrain,” explains Jennings. “When you pass over it again, it knows what’s coming ahead. Like an experienced operator, it’s managing the blade load. It’s going to proactively lift the blade just like an experienced operator would know to do.”
With every pass, you maximize the blade load. “Anytime you can optimize and fill your blade with each pass, you are doing it the most efficient way possible,” says Jennings. “You’re reducing maintenance costs to the owner because you are not slipping the tracks. Every time you are overloaded, you are burning more fuel and you might slip the tracks.”
As you approach the finish grade, the blade will adjust. “The system is smart enough to look at the target design and existing ground and transition automatically,” says Ron Schwieters, product marketing manager, Komatsu America.
Integrated Technology Adds Reliability
More technology is being integrated into crawler dozers at the factory, with key sensors and processing technology coming standard. These machines are ready and pre-wired to incorporate the grade control system of choice.
“The reason customers like integrated systems is all about reliability,” says Meeker. “Today, [Caterpillar’s] most popular option is going to be the Attachment Ready Option with assist.” All of the sensors are built into the tractor so a grade control system can be added later. Inertial measurement units (IMUs) are pre-installed on the blade and C-frame.
The technology must be flexible to fit into the customer’s existing operations. “Factory grade control is important. But it is maybe just as important to have all of the difficult components factory installed and then have the ability to update that and [install] the components the customer wants,” says Meeker.
This gives customers the ability to set the machine up for their specific applications. “Some customers don’t just want GPS grade controls. Some of them want lasers or universal total stations (UTS),” says Meeker. “The flexibility and versatility of being able to put whichever system you want on there is really important.”
As accuracy demands increase and allowable jobsite tolerances continue to tighten, UTS will continue to gain popularity. “The ability to do UTS is pretty important,” says Meeker. Laser, GPS and UTS all have their place. “It’s all about choices.”
“It’s a combination of GNSS antenna, IMU and cylinder stroke sensors, with all the combination suite technologies to get that final position of the blade,” says Jennings. “[The dozer] knows what other parts of the machine are doing, whereas the third-party [grade control] may not have that visibility to ‘What’s my engine rpm? Do I need to speed the machine up or slow the machine down?’” With machine integration, various components are in constant communication with each other and machine intelligence can be used to optimize the end result.
The integration allows advanced technologies such as track slip reduction. “None of those aftermarket systems know what load is on the machine,” says Schwieters. “All they know is blade up and down to grade.” Managing track slip allows you to maximize productivity.
“Precision construction technologies such as [John Deere’s] SmartGrade, which come from the factory integrated into the machine, come with many benefits both on and off the machine,” says Goedert. “Of course, protection of the system from damage is a big benefit. We try to protect harnesses and components as much as we can, whether it’s with guarding or just how we route the hoses.”
Machine integration can also help with customer support. “John Deere is constantly looking for ways we can support our customers better. For example, all SmartGrade machines released moving forward will have SmartGrade Remote Support,” says Goedert. “This tool allows customers and dealers to remotely view and control the display as if they were sitting in the cab.”
SmartGrade Remote Support enables support for remote troubleshooting, and if the dealer ends up having to visit the machine, it allows them to know which parts to bring. Similar to IT remotely controlling your computer, the operator can watch what’s going on as the display is being remotely controlled, which makes it a useful training tool, as well.
This connectivity expands beyond grade control to machine health and diagnostic capabilities, as well as productivity data. “John Deere Service ADVISER Remote allows service technicians to interact with our machines at a level they haven’t seen before. The dozers can receive wireless software updates, avoiding a technician making a trip to the jobsite. This also links the machine to the John Deere Machine Monitoring Center that is supported by both the dealer and factory support personnel, who are standing by ready to help.”
Dozer owners are provided with a wealth of information about the usage of the machine directly in the machine’s display or through JDLink, a telematics solution that remotely connects customers to their equipment through a desktop or mobile device.
Drivetrain Technology Drives Efficiency
Drivetrain technologies for crawler dozers continue to evolve with advanced hystat or electric drives.
“The key efficiencies in electric drive are going to be basically not wasting any energy,” says Meeker. “When you have a torque converter or even a hystat type of system, you’re required to transfer the power from the engine down to the tracks. You are required to compress oil and heat it up. The electric drive system does not create nearly as much heat because we’re not compressing that fluid and using it for work. We are using the electric system for work.”
The D7E was Caterpillar’s entry into the electric drive crawler dozer market. “The D7E was our first-generation electric drive,” says Meeker. “It had a permanent magnet generator and motor and a non-serviceable inverter.”
The D7E proved the viability of the electric drive concept and the technology has now evolved with the introduction of the D6 XE. “When we went to the D6 XE, we went to a different style of motor and generator, which was lighter weight and more efficient at the same time,” says Meeker.
While the older D7E required a cooling system around the generator, the increased efficiency of the D6 XE technology has eliminated the need for this system. “We basically don’t generate the heat, so we don’t have to cool it,” says Meeker. “We do run oil through the rotor so that we can cool and lubricate the bearings.
“The electric drive system allows the diesel engine to run at the most optimized rpm to get the best efficiency,” he continues. Excess engine speeds result in high rotational mass and the friction creates energy loss. That is why over-the-road trucks try to run at around 1,200 rpm. “The lower the engine rpm can be, the more efficiency and the least amount of waste you have. The D6 XE is designed automatically to want to run at 1,400 rpm.”
Size does matter when looking at electric drive technology. “Electric does cost a little bit more to manufacture than what a traditional powertrain does,” Meeker notes. “So, going bigger is less of a challenge than going smaller.”
It boils down to the ability of the fuel savings to offset the cost of the components. For instance, saving 10% fuel doesn’t save you much when you are burning 2 to 3 gal./hour.
“If you have a D11 and you save 10% fuel, now you have something to really think about,” says Meeker. “The larger you go, the easier it is to scale up.” Thus, the technology is well suited for the D6 and larger crawler dozers and wheel loaders such as the 988K XE.
Hydrostatic drive technology has also evolved to increase efficiency. The Liebherr Generation 8 crawler dozers build on the electronically controlled, continuously variable drive with ECO mode. Power can be tailored to the application. If large quantities of material are to be moved, the hydrostatic drive works at constant engine speed to save resources and keep costs down. For light work, there is also an Eco mode.
Hydrostatic drive offers advantages in terms of technology integration vs. mechanical drivetrain technology. Electronically controlled hydraulics allow full adjustability of speed and responsiveness of hydraulic movements in the Liebherr 9-in. display.
As electronic technologies evolve, new productivity-enhancing features will continue to find their way to the next generation of crawler dozers, resulting in simplified, yet more productive operation.
“Increased technology will be a key focus moving forward across machine platforms,” says Goedert. “Whether it’s productivity-enhancing solutions like SmartGrade, using technology to make jobsites safer or thinking about how data and digital environments help customers more efficiently manage their business, we never stop listening to customers. Technology evolves every day, and we continuously work to help our customers run smarter and more sustainable. The future in the construction industry is exciting.”