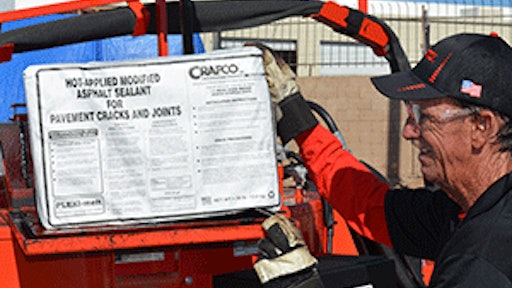
Use of pavement preservation treatments extends the remaining service life of asphalt pavements. These treatments typically include spray applied surface seals, thin overlays, crack treatments, chip seals, slurry seal/micro surfacing, surface recycling and others.
Each preservation treatment reduces damaging effects of aging and deterioration of the pavement surface layer and helps protect the integrity of the underlying pavement structure. If proactive preservation treatments are not used, pavements deteriorate more rapidly and require major rehabilitation with structural overlays or reconstruction much earlier.
We all know the ever-growing concerns about our environment and many feel that the construction industry has a large negative impact on the health of our air and water.
However, a recent paper, Energy Usage and Greenhouse Gas Emissions of Pavement Preservation Processes for Asphalt Concrete Pavements by J. Chehovits & L. Galehouse, found significant energy and greenhouse gas (GHG) emissions savings are achieved when using pavement preservation techniques.
Not surprisingly, new construction, major rehabilitation, thin hot mix asphalt (HMA) overlays have the highest energy use and range from 5,000 to 10,000 BTU/yd2– yr (6.3-12.6 MJ/m2-yr).
Chip seals, slurry seals, micro-surfacing, and crack filling utilize lower amounts of energy per year of extended pavement life and range from 1,000 to 2,500 BTU/yd2– yr (1.3-3.3 MJ/m2-yr).
Crack seals and fog seals use the least amount of energy per year of extended pavement life at less than 1,000 BTU/yd2-yr (1.3MJ/m2-yr).
Therefore, the study concluded that in order to minimize energy use and GHG emissions over the life of a pavement, all preservation treatments should be utilized as appropriate to the maximum extent possible for the existing pavement conditions.
Another Sustainable Step
Manufacturers tend to pride themselves on knowing what their customers need before they need them. In anticipation of the need in the market for a “green” crack sealant solution, Crafco has developed a packaging called PLEXI-melt.
PLEXI-melt is an innovative high-strength, low-density, protective packaging used to contain Crafco hot-applied sealants and mastics. This environmentally friendly packaging quickly and thoroughly melts into the material at normal operating temperatures without affecting product installation characteristics or specification performance.
Not only does this product eliminate the waste of traditional cardboard boxes that contain crack sealing material, but it also eliminates the need for an additional crew member on hand to handle the waste, saving both time and money.
The PLEXI-melt patented designed packaging allows users to move the package directly from the pallet to the melter where they can drop it in, eliminating the time and labor needed to open boxes and remove the sealant/mastic. The PLEXI-melt packaging melts completely, preventing messy clogs and potential down time.
Crack sealing is an important preservation step that not only prevents water from entering and destroying pavements, but can also help to greatly reduce energy, waste and pollution over remove and replace pavement repair methods.