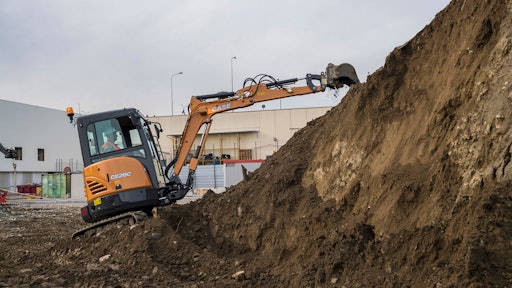
Without question, excavator operators are encountering more challenges on their urban construction sites than they ever have before. First, commercial and residential development is increasing at a steady pace, leading to larger buildings and homes on smaller lots. As these buildings and homes are being developed, construction sites are becoming restricted, and operators cannot move their excavators as freely as they used to.
“Tight corners, narrow pathways and confined areas can limit excavators’ abilities to navigate easily, thereby requiring careful planning and skilled operation,” said David Caldwell, national product manager, Takeuchi-US.
Aside from restricting excavators’ movements, present-day urban construction sites provide operators with another significant challenge—they typically don’t provide enough space to store their excavators. Therefore, they must use their equipment efficiently because they can generally only arrive at the construction sites, dig and then immediately leave, according to Brad Mace, product manager, CASE Construction Equipment.
To efficiently excavate on tight, urban construction sites, operators must be precise and cautious. After all, according to Caldwell, excavators are generally used near existing structures, like buildings, fences and walls. By being as precise and cautious as possible, operators can avoid collisions, along with any subsequent damage associated with them.
“Narrow gates or entrances can make it tough for some excavators to enter or exit construction sites,” Caldwell stressed. “In turn, delays can occur and additional efforts to create suitable access points may be required.”
At the same time, according to Drew Kolo, marketing manager, Doosan Bobcat, excavator operators must work near critical infrastructure that simply can’t be disturbed, including fiber optic cables, power lines and water and gas lines. And, of equal importance, they’ll have to overcome issues associated with noise. For example, while working in small, confined areas, the noise and vibrations produced by excavators will amplify, resulting in discomfort for operators, nearby coworkers, and occupants of businesses and homes that are nearby, according to Caldwell.
With the goal of protecting excavator operators and everyone near them, state and national governments have passed several noise restrictions for construction sites. Additionally, to protect the environment, state and national governments have enacted carbon emission restrictions too, which operators must bear in mind every time they use their excavators.
The bottom line? As a result of each of these issues, the smaller an excavator is, the better.
The CASE CX60C comes with a standard adjustable boom that can be offset to either side, enabling them to operate in tight urban construction sites.CASE Construction Equipment
Increase Efficiency, Minimize Disruptions, Reduce Injuries
Spatial awareness, precise control and adaptability are key skills that operators should strive to enhance as they use excavators—particularly compact excavators—and face several issues on their urban construction sites. In addition, according to Caldwell, they must have effective communication with their coworkers and implement safety protocols to guarantee their excavation operations run as smoothly and safely as possible.
Training and practice, regarding compact excavators, are vital too, as each will help operators become more efficient and precise whenever they use their machines. Aside from focusing on their excavators, operators should also verify whether any access or stability issues are present on their construction sites before they begin excavator operations.
“By finding ways to ensure clear access and impose additional safety measures, operators can prevent any potential of delayed projects once their compact excavators arrive on their construction sites,” Caldwell explained. “Because they won’t need to ask for additional time to dig or move materials, they can better meet and exceed customer expectations.”
Operators should seek compact excavators that either have zero or short tail-swing designs, along with swing booms that will effortlessly and safely dig next to walls and guard rails.Yanmar Compact Equipment North America
Along with focusing on people near their construction sites, operators must direct their attention to their colleagues, particularly by maintaining awareness of their surroundings and ensuring that all team members remain as far away from excavators as possible.
“Situational awareness also helps prevent impacts with structures or other obstacles,” said Wesley Foy, product manager, Yanmar Compact Equipment North America. “Aside from utilizing their own awareness, excavator operators can use certain equipment features too, which will help them minimize construction site injuries considerably.”
Consider Tail Swings
Above all else, contractors and operators should seek compact excavators that either have zero or short tail-swing designs, as well as swing booms that will effortlessly and safely dig next to walls and guard rails.
“If excavators don’t protrude over tracks, operators can get closer to structures or move around in tight areas more easily than if they had to use a conventional tail-swing excavator instead,” Foy added. “Yanmar offers excavators with zero and minimal tail swings.”
Operators should seek compact excavators that either have zero or short tail-swing designs, along with swing booms that will effortlessly and safely dig next to walls and guard rails.Yanmar Compact Equipment North America
“A zero-tail swing virtually eliminates any potential of a compact excavator’s tail inadvertently contacting surrounding objects and damaging them, along with the excavator itself,” he noted. “Meanwhile, a minimal tail swing significantly reduces the likelihood of inadvertent contact, thus minimizing the odds of damage to nearby objects and structures.”
Like Yanmar, Takeuchi-US provides excavators with short tail swings too, including its new TB335R and TB350R models, each of which enables operators to use their excavators in small spaces in a less risky way than they did in the past, especially with regards to damage and disruptions to their surroundings.
Retractable undercarriages, available on compact units like the TB210R, minimize excavators’ footprints, allowing them to access constricted areas.Takeuchi-US
As operators determine whether to use zero tail-swing excavators, minimal tail-swing excavators or conventional tail-swing excavators, the sizes of the gates and property lines they must pass through may be a substantial factor. Zero and minimal tail-swing excavators, after all, are roughly 70 inches wide. In contrast, conventional tail-swing excavators, like 3-metric-ton to 4-metric-ton compact excavators, are approximately 60 inches wide.
“If operators anticipate routine work in which they must pass through narrow gates or property lines, conventional, tail-swing excavators may be the best fit,” Kolo stated. “They’re also ideal for gaining additional lift capacity, yet they may limit operators’ abilities to efficiently work in tight spaces.”
Enhance Reach, Dig More Accurately
Doosan Bobcat’s excavators are always available with standard arm configurations too, offering operators maximum breakout force and lifting capabilities, leading to more enhanced digging performances. For further reach and dig depths though, Kolo advises operators to equip their compact excavators with a long-arm option instead. By having additional reaching abilities, along with higher dump heights, they’ll be able to conduct more work without ever having to reposition their excavators, ensuring that they can load trucks in a more effortless way. Since the long-arm option has an additional counterweight when compared to standard arm configurations, operators will be able to enhance their excavators’ (whichever ones have the long-arm option, that is) lifting capabilities.
If excavators don’t protrude over tracks, operators can easily get closer to structures or move around in tight areas.Yanmar Compact Equipment North America
“Additionally, Doosan Bobcat’s unique Pro Clamp system is optimized for a standard arm configuration, allowing operators to grab large, small or irregular objects with greater confidence,” Kolo emphasized. “This feature is ideal for snug working conditions, as it enables operators to perform demolition or tear-out work, create smooth trench bottoms, and install and repair utilities by removing the tool, as needed for optimum visibility.”
Earlier this year, Doosan Bobcat released the E10e and E32e battery-powered excavators. Releasing no emissions, the excavators can be used quietly for challenging job tasks on very tight construction sites.Doosan Bobcat
“All Bobcat compact excavators feature an exclusive in-track swing frame as well, which allows operators to get closer to their work,” Kolo continued. “The manufacturer’s boom swing castings and cylinders also stay within their tracks whenever operators conduct offset digging tasks, enabling them to truly dig flush against an obstacle and work in tight areas.”
Speaking of offset operation, Takeuchi-US presently offers two compact excavators that have side-to-side boom designs: the TB257FR and the TB280FR. As a result of their designs, the excavators can be used offset, while requiring minimal rotation of their counterweights. Providing high stability and lifting capabilities, particularly over their right-side tracks, these excavators offer high visibility for operators as they work offset, too.
“Each of our FR series excavators can also rotate almost completely within the track frame’s width, allowing each one to perform a full rotation in very tight spaces with their booms fully retracted,” Caldwell said.
Commit to Sustainability
According to Mace, compact excavators are currently the second largest category in construction equipment, and their popularity continues to rise. Aside from using excavators with zero, short and standard tail-swing designs, operators can also use electric compact excavators, enabling them to comply with emission and noise regulations more easily than they have in the past.
First, they can be used indoors without any risk of diesel or propane emissions being released into the air. And since they’re much quieter than the combustion-engine-driven excavators in the marketplace, operators can stand next to them as they’re running and have conversations with their colleagues at normal volumes.
“Electric excavators are being designed to deliver the same amount of power and performance as diesel-powered excavators too,” Mace said. “They also provide operators more adjustability, concerning their control panels—from adjusting performance modes, to setting flow rates for attachments, to customizing the machine parameters to their applications or preferences.”
Takeuchi-US also offers an electric compact excavator: the lithium-ion battery-powered TB20e. Because of its low noise operation and zero emissions, the TB20e is ideal for working in different applications, including in and around hospitals, municipalities, neighborhoods and schools.
“The TB20e provides excavator owners and operators a great opportunity to demonstrate their commitment to sustainability too, which many businesses, communities and organizations will look upon favorably,” Caldwell stressed.
Earlier this year, Doosan Bobcat released the E10e and E32e battery-powered excavators. Releasing no emissions, the excavators can be used quietly for challenging job tasks on very tight construction sites.Doosan Bobcat
“Because they release zero emissions, the excavators allow operators to work indoors, including when they need to conduct indoor demolition projects in which intensive manual labor is often the only other option that’s available,” Kolo stated. “They’re also quiet and can be operated at all hours of the day, even in dense urban areas where noise can, at times, limit operators’ work hours.”
Technology Offerings Increase Accuracy & Control
As operators use compact excavators in restrictive, urban construction sites, an array of technological offerings are available, some of which they may not even know they need.
According to Foy, boom swings can help them navigate around tight corners and dig around obstacles. In addition, by using a hydraulic quick coupler, operators can decrease their movements into and out of tight areas because they’re able to change attachments without ever having to move from their work areas.
According to Mace, operators can also use CASE Construction Equipment’s intelligent and integrated displays, including touchscreen operator controls, which are highly visible and ergonomically accessible. Consequently, they can enhance operators’ safety and excavating efficiency, especially in space-constrained construction sites.
Additionally, retractable undercarriages are available on some of Takeuchi-US’s excavators, including the TB210R, TB216, TB216H, TB20e and TB225. For instance, the TB210 can retract down to 29.5 inches, enabling it to fit through a standard doorway. On the other hand, the other models have undercarriages that can retract substantially, allowing them to fit through backyard gates. Once the excavators have entered the operators’ construction sites, their undercarriages can be expanded to ensure that they’re highly efficient and stable.
“Compact excavators are equipped with control systems that enable them to work with great precision and control,” said Caldwell. “Features like precise, low-effort pilot controls and proportional auxiliary hydraulic controls help reduce operator fatigue. Not to mention, they also provide operators greater precision, along with the ability to meter flow rates to the hydraulically driven attachments they may be using on confined construction sites.”
He continued, “With these offerings, operators can work on a wide range of projects, as they have the control and precision they need, resulting in improved performance, greater efficiency and higher profitability.”
Moreover, operators can adopt the latest generation of telematics equipment management platforms, including the CASE SiteWatch. Able to generate real-time, remote information concerning compact excavator performance, the platform also creates service schedules, enabling them to set alarms and receive notifications if excavators ever operate outside their normal parameters. In turn, operators can protect their excavators and prevent potential damage, as they won’t be used when they’re not supposed to. And they’ll be able to identify potential service needs before they evolve into issues that require considerable downtime.
Able to be towed with a conventional pickup truck -- without any need for a CDL -- compact excavators like the CASE CX26C are an easy addition to a majority of companies' fleets.CASE Construction Equipment
At the same time, they can also use Bobcat Machine IQ, a telematics system that helps them remain organized as they maintain their compact excavators. While using the system, contractors and operators can remotely track their compact excavators’ locations, maintenance and service issues, and operational statistics, thus minimizing maintenance costs and maximizing machine utilization.
“As construction booms in tight, urban spaces, by implementing these technological advancements, compact excavators will [allow] operators, managers and fleet owners to structure fleets that operate more easily and productively in these types of environments,” Mace concluded. “With ‘smarter’ excavators, operators can become more efficient and, in turn, reduce any of the issues that negatively impact productivity, profitability, safety and uptime.”