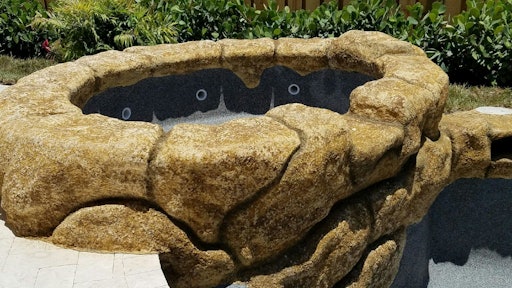
Rock Miller isn’t a typical artist. A concrete pump takes the place in his hands where others would grip a paintbrush or pencil. His canvas isn’t cotton or linen, but concrete and rebar. Yet Miller’s work designing commercial and residential swimming pools for his family business, Pool Crafters, in West Palm Beach, Florida, is nothing short of a masterpiece. Each pool features handcrafted rocks and waterfalls, showcasing Miller’s passion for design.
A Process Worth Preserving
Miller’s father, Charles D. Miller, founded Pool Crafters in 1962 and since the younger Miller was 12 years old he spent summers helping his dad while learning the tricks of the trade. Of course, back in those days, Miller and his father hand-packed the concrete to build the pool walls. Through the years, they added concrete piston pumps to speed up the process. While these pumps certainly proved more efficient, Miller recently found himself faced with a challenge. As with any artist, his desire and passion for the fine details led him to question the quality achieved with piston pumps when creating rocks.
“I had to run my piston ball pump at full throttle to pump a 2- or 3-inch slump and would end up giving myself too much concrete to work with when doing detailed work,” Miller says. “Not only that, but I’m turning 60 this year, so I need a machine that slows down the process.”
Miller’s process starts by setting rebar up to extend every six inches from the pool’s beam. He then ties and shapes the rebar into rock waterfalls, careful to round any sharp edges before spraying the concrete with a high pressure pump.
“We try to make the rocks with a bit more rounded edges,” Miller says. “You don’t really notice when you look at them, but they’re safer for pools, and safety is our No. 1 priority.”
The rocks are then waterproofed, colored and texturized. Miller combines sand and seashells from the beach with a cement product to form his specialty — artificial Palm Beach Cap Rock. It’s a popular item for Miller, as sandstone found in authentic Palm Beach Cap Rock absorbs water — a problem owners of older pools made with this rock are experiencing. Not only is Miller’s artificial Palm Beach Cap Rock a popular answer for these customers, but it also appeals to first-time pool buyers.
“As far as I know, I’m the only guy in south Florida making rocks like this,” Miller says. “We developed a niche market because of it, and it’s a process I knew I had to preserve.”
With increasing demand to repair older swimming pools as well as to build new pools with that look, it was time to find an innovative equipment solution.
Saying ‘No’ to the Naysayers
Miller stumbled upon Blastcrete Equipment Company, an Alabama-based manufacturer of concrete pumping equipment, while searching YouTube for ideas. He was impressed with what he saw and reached out to the company. After a few phone conversations with Tripp Farrell, Blastcrete president, and Scott Knighton, vice president, Miller faced the decision of whether or not to try using the squeeze pump model they proposed. He was skeptical at first after speaking with a few concrete pump manufacturers in south Florida who firmly believed a squeeze pump would not work. They said the challenges faced by contractors pumping in the South where concrete contains crushed limestone as opposed to river rocks in the North, would not be compatible with a squeeze pump.
“I remember Tripp saying, ‘Rock, you need to trust me on this’,” he describes. “It’s a big investment, but it ended up working out great. We’ve completed three jobs with our Blastcrete pump, and it’s already paid for itself.”
The Blastcrete D6528 concrete pump attaches to Miller’s T550 Bobcat, which powers the pump. This drastically cuts down on operation costs and is significantly less expensive than purchasing a stand-alone pumping unit. Blastcrete even customized the machine’s size for Pool Crafters by making the unit smaller. Most importantly, with the D6528 Miller can slow down his work to five or six yards of concrete pumped per hour, allowing more time for detailed shaping.
Solving the Maintenance Mystery
Beyond operational savings, the squeeze pump offers Miller maintenance and cleaning advantages. Unlike swing tube piston pumps that contain several wear parts, squeeze pumps only contain one, the rubber pumping tube, making them the most economical concrete pump. On average, maintenance costs are typically less than $1 per cubic yard of pumped material.
“There’s never going to be a guessing game on why the pump isn’t working,” Miller says. “If something happens with the squeeze pump, we know the issue has to be the hose. That’s a good insurance policy for me.”
Miller already purchased a spare hose and said it’s only a 20-30 minute job to replace it should anything happen. With piston pumps, maintenance is more of a mystery. Common wear parts on piston pumps include cup seals, piston cups, poly packs, wear plates and wear rings.
“Unless you’ve been around pumps for a long time, you wouldn’t know what part to replace when a piston pump stops working,” he says. This forces the operator to quickly place any remaining concrete from the truck or accrue additional expenses from sending the concrete back.
In addition to reduced maintenance, Miller said cleaning is easy with the D6528. Concrete is pumped out the hopper and a round sponge ball is sucked into the pump’s inlet pipe. The hopper is then flooded with clean water, which pushes the ball through the pump and delivery system.
“It’s easy to clean, like all of our pumps,” Miller notes. “However, the squeeze pump uses less water and doesn’t take as much time.”
The Payoff
In the end, Miller’s openness to different ways of doing things paid off and continues to pay off. A concrete squeeze pump was the ideal solution for Pool Crafters.
“I’m very happy with my decision and the experience with Blastcrete,” he says. “They listened to my needs and desire to preserve our detailed process of rock carving. Their customized solution was exactly what we needed.”