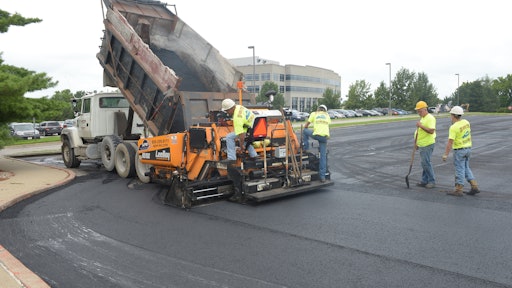
Companies around the world are testing a variety of additives in hot mix asphalt. Last summer, Asphalt Paving & Maintenance (APM) became the first contractor in the United States to tackle a significant job using a mix containing an additive derived from end-of-life printer cartridges.
Lexmark International, a printer manufacturer based in Lexington, KY, sends its toner powder, a waste product from printer cartridge recycling, to Close the Loop (CtL) in Hebron, KY. Close the Loop, a clean tech and resource recovery company for imaging consumables, has established a global reputation for providing end-of-life management services and recycle a variety of materials into environmentally friendly products. CtL approached Lexmark with an innovative idea of using recycled toner powder in hot mix asphalt. As the two companies pursued the idea, they approached contractor APM in Lexington, KY, who previously completed work for Lexmark. APM outlined and bid the job: a 1-1/2-in. overlay of a 17,000-sq.-yd. parking lot that was split between traditional hot mix overlay and a test section containing the additive containing recycled toner called MTP.
The additive (MTP) is produced by Close the Loop, and is made of 100% recycled materials including crumb tire rubber, waste oils, and waste toner powder. Finding a high-volume and economically sustainable reuse program for the powder has been an environmental challenge on a global scale, and therefore made this project very significant.
“When we first heard about their product, we thought that it was a pretty interesting idea. We did some research and no one had installed a mix using this additive in North America and we were intrigued to be part of the process for the first installation,” says Peter Kramer, APM president. “We worked very hard for this project. It’s a unique product and a process and we’re really excited to be part of it.”
A “Customer Centric” Contractor
While APM does a good amount of new construction, Kramer says the full-service pavement maintenance company’s bread-and-butter is rehabilitation of existing commercial sites including milling, patching, overlays, sealcoating, and striping. He described the work for rehabilitation as 75% paving related, and 25% is sealcoating and striping.
“We’re very customer centric,” Kramer says. “We work hard to meet their needs and to come up with the best possible solution – not the cheapest or the easiest necessarily, but what’s best for what the customer needs. And that approach has opened some doors for us.”
Kramer says APM runs two crews: a three-person sealcoating crew and a six-person paving crew. Occasionally APM will reorganize crews to create a prep-work crew to create efficiencies for the paving or sealcoating crews to start and finish jobs. Kramer says the “top lean” company employs up to 20 people in peak season with virtually everyone in the field. He says the company is able to operate as lean as it does because they developed a stand-alone project management software process that relies on texting and email to track jobs, disseminating information to crews and enable teams to send information back in an efficient manner.
Bill Shaw, Kramer’s father-in-law, started the company in 1982; and when Kramer, a biologist by training, married into the family in 1998, his father-in-law approached him about doing some striping work. That discussion evolved into a partnership, and Kramer worked for five years in the field, learning the business from on-the-job field work to preparing bids. Kramer eventually transitioned into his current managerial position, where he takes the lead on estimating production and operations while Shaw focuses on the financials (however, both pitch-in where they’re needed).
Paving in Two Halves
APM coordinated the Lexmark project, working closely with Allen Co. (the hot mix asphalt producer), Denham Blythe (general contractor), and Close the Loop to get the job done. Located 15 miles from the jobsite, Allen Co. used a drum plant to produce the mix for the job, and the nature of the drum plant created just one of the challenges for the producer/contractor team.
Kramer says that while all work flowed through Denham Blythe, the project was a team effort that involved numerous meetings among all the partners to establish a schedule and cover all details.
Kramer said Steve Hall, APM superintendent, controlled the job from start to finish. “He made sure the work progressed and was completed the way we said when we bid it and talked it through with all the players involved,” Kramer says.
Overall, the Lexmark project included 1,600 sq. yds. of pavement repair including localized areas of failure that had to be milled full depth. APM then installed binder asphalt to bring the milled areas up to grade before placing the 17,000-sq.-yd. overlay. Because the project was the first U.S. use of hot mix containing the MTP additive, APM and Close the Loop wanted to design a control area so they could monitor how the mix held up over time relative to a traditional hot mix.
“Early on, it was determined that the project would be set up as a test case with a control pavement segment so everyone involved could evaluate the use of the toner based additive,” Kramer says. “Close the Loop donated the additive to the project for half the parking lot paving.”
APM divided the parking lot into two halves, paving half using a traditional surface mix asphalt and the other half using the mix with the recycled toner additive. “We divided it so the traffic volume would be equal on both halves over time,” Kramer says.
The work was completed in early August in four days following a week of preparation. Kramer says the first week crews removed existing asphalt curbs, installed extruded concrete curbs, and installed and repaired other concrete areas. APM crews paved half the lot in two days using a traditional mix, then followed with two days of paving with the toner additive mix.
“We could have done the job in two days but because they had to make sure the parking lot was accessible to Lexmark International employees we spread it over four days for their convenience,” Kramer says.
Overcoming Challenges
Kramer says one of the early challenges the group faced was how to introduce the toner additive into the hot mix. The additive is available in 30-lb. bags of pellets. Although the asphalt drum plants are continuous feed operations “it’s a lot more difficult to put a given quantity into a continually fed process,” Kramer says.
Close the Loop came up with a mechanical solution to feed the pellets into the process using an auger screw, turning at a precise rate. “That enabled us to deliver the material into the mix at a constant rate,” he says.
Another challenge was dealing with the 15-mile distance of the plant from the jobsite. Kramer says APM paid close attention to scheduling and tarping to make sure the mix was workable throughout the paving process. “Material delivery was a real challenge,” Kramer says. “We had to get the proper amount of trucking, make sure to schedule it correctly and then adhere to the schedule. We paid close attention to deliver the material to the site in a timely fashion.”
APM didn’t want to risk having its haul trucks sitting in line waiting – like most pavers do on most jobs – or its special toner-modified mix. So to make sure APM got the mix it needed, when it needed it, the contractor and Close the Loop paid a lump sum to Allen Co. to reserve and rent a HMA storage silo just for their drivers on this job.
“We rented the silo on the day of production. That enabled us to not only make sure the mix was available but that our trucks could get in and get out quickly as we were the only people using the material from that silo,” Kramer says.
He says there were some additional haul costs because of the added distance (the job was quoted using a closer plant) and the extra trucking APM brought in to maintain the schedule. But Kramer says that additional cost was mitigated by the fact APM was able to rent its own silo.
“The biggest challenge was coordinating with the plant, but that was made easier because we had exclusive use of the plant for the days we were paving,” Kramer says.
But even that created additional concerns – particularly with the weather. “Like any contractor we’re always watching the weather, but because we had to rent the plant and silo for the days we were paving we had to make sure we could pave on those days,” Kramer says. “It made watching the weather more important than normal because we had the plant on the days we were paving. We were much more aware of the weather on this job.”
“The mix with the toner additive went down just like traditional hot mix asphalt,” Kramer says. “There were no installation differences between the two materials. From laydown to compaction to handwork there was no apparent difference.”