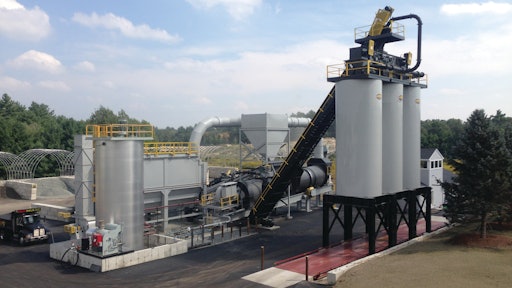
While the demand for stricter environmental standards grows, RAP piles do too. Policy changes are needed before state and federal projects can accept the higher mix percentages.
The road building and asphalt industry continue to feel the push for higher and higher sustainability standards. We want our roads to be made of less embodied carbon, we want to produce the asphalt in greener ways, we want to make the paving and transportation cleaner and more efficient, and, of course, we want our surfaces to last longer. Meanwhile, ever larger piles of RAP sit around, and contractor's hands are tied when it comes to just how much they can include in their mixes for public sector projects. All this while the technology and the research seemingly indicates and supports the reality that mixes with even higher rates of RAP are still capable of meeting quality guidelines and longevity standards.
In a paper authored by current NAPA president Audrey Copeland, she states, "Recycling asphalt pavements became popular in the 1970s due to the high cost of crude oil during the Arab oil embargo. As a result, construction practices and technologies quickly evolved to handle RAP." She goes on to outline the steady and widespread use of increasing RAP in the mix designs for the FHWA for nearly two decades, until the 1990s and the introduction of the Superpave mix design method. During this period, RAP usage in the mixes was largely kept below 15%, because it didn't require any extra testing. But the bell now swings back again, and maybe for good.
"Utilizing greater amounts of RAP [is] a priority in the HMA industry once again," said Copeland. "With changes in construction materials economics, stricter environmental regulations, and an emphasis on green technologies (e.g., warm mix asphalt) and sustainable pavements, the highway community is reassessing the economic and environmental benefits of allowing higher percentages of RAP in premium pavements and asphalt surfaces while also maintaining high-quality pavement infrastructures."
While Copeland's comments were originally directed to a different time period, they still ring true to our current situation. Some believe that it is long overdue for national standards to be implemented on the expanded use of RAP in mix designs. The technology already exists on the market to implement high RAP percentages, all the way up to 100%, theoretically.
What Makes It Possible: Softeners vs Rejuvenators
One of the types of products that make this possible has been in popular use since even before the oil crisis of the 1970s: asphalt additive rejuvenators. The first topical rejuvenators, applied to the pavement surfaces came to market 20 years before that, during a time when resources were plentiful. In the mid 1950 the rejuvenator Reclamite was developed out of the work done by Dr. Fritz Rostler and Richard White.
This was a topical rejuvenator, but set itself apart at the time, where most of the surface treatments acted as a sort of "glue" to hold aging pavements together. This was in contrast to what hot mix rejuvenators do, reversing the chemical defects of aged binder and restoring its original properties. However, there are other methods of softening binder and recycling asphalt that work somewhat differently.
"Before the use of additives or rejuvenators, asphalt producers would typically use bump grades to include more RAP and RAS," said Austin Hohmann, Product Manager at Colorbiotics. "For example, if a 58-28 grade of asphalt in the ground is required by the spec, contractors would source a 52-34 and add RAP/RAS to bring that grade back up to a 58-28. This is how you might traditionally save on costs. Currently, those 52-34 grades are synthetic, and the 58-28 grades are becoming less common. These softer binder grades are sometimes produced via rejuvenator dosing at the terminal and is more of a viscosity modification, or “softening” rather than a 'rejuvenating' process. A viscosity modifier is similar to adding vegetable oil to peanut butter. It makes the substance softer but doesn’t change the chemistry of the substance."
These methods, though, aren't really capable of handling the higher degrees of RAP content - greater than about 30% - where the standards need to go. "The idea that folks were using in the past was: if I put more recycled in, then I put in a binder softer and they should counteract each other," said Hassan Tabatabaee, Global R&D Leader for Cargill. "That works up to a certain amount of recycling, but when you go higher than that, it can destabilize the mix, which is where additives like the new generation of recycling agents really come in to stabilize the mix and enhance performance of higher recycled contents mixes."
But if the softeners are able to get close, how are rejuvenators that much different? The real answer to this question lies in the chemical science behind what goes on between the interplay of elements in your asphalt mix. It's a very complex process, and these rejuvenators are able to enact physical changes on the microscopic level. Like a time machine for asphalt binder, it reverses the impact of age. If higher RAP is the future, then chemical rejuvenators will need to be a part of the process.
"There's a degree of softening that is always going to be part of this. With petroleum based additives and oils, however, mix producers generally using a higher amount of the softner oils," Tabatabaee continued. "But with these newer bio-based recycling agents, they are effective at very low dosages, and they have a secondary mechanism in addition to softening, which acts differently."
As asphalt binder ages, molecular gelling occurs, which is the result of oxidation over time. The molecules associate into larger, stiffer, and more rigid structures internally. This makes the bitumen extremely brittle, and less able to be flexible and/or absorb stress without cracking or splitting. Rejuvenator's added ability is to be able to "disassociate" those rigid molecular structures, dealing directly with the issue of brittleness.
“Aged asphalt chemically has two interrelated problems,” said Tabatabaee. “Imbalances in the chemical fractions that are essential to make it work, and one of those important fractions is the resins that keeps those more heavy polar molecules disassociated. When you age asphalt, you lose these molecular spacers.”
This is what leads to the brittle structuring. Rejuvenators rebalance those fractions with fresh chemical agents. One rough example of this process would be that of how you make a bowl of oatmeal. If you add all the correct ingredients, but let it sit in the pot too long, everything will start to clump together as the milk evaporates. It will get thicker and thicker. If you go back and add milk and stir the mixture up, you can achieve a proper and more appealing consistency again. It’s not a perfect example, but it helps illustrate the basic concept.
Rather than softening the entire mixture, these agents directly address the underlying problem, making it much more effective. How they achieve this is pretty incredible.
Hohmann explains how it works, "Colorbiotics products have an Oxirane that is stable up to most chemistry within the asphalt, but only when in contact with acid groups, which arise from oxidation. The oxirane groups react. These acid groups or oxidative sites are the actual cause of asphaltene agglomeration. As more and more of these aged sites arise, the aging speeds up. Rejuvenators chemically react with the oxidized sites to eliminate the asphaltenes from clumping together and reseparate (or redisperse)."
Conditions and Limitations?
Rejuvenators are an incredibly useful technological solution in the fight to increase RAP usage and bring down material costs for the producers who can utilize more recycled material in place of the virgin ones. However, not much has been said about their possible limitations, or the conditions under which the products are most effective. How many times can you go back and add milk to the oatmeal? Is there a certain point where the quality of the asphalt inherently breaks down? Are there certain environments where these types of products are more or less effective?
Nobody wants to buy-in on a new product, in this case bio-based rejuvenators, only to find out after the fact, that the region they're located in doesn't have a conducive climate for it. These types of questions are worth asking, and digging into, especially if you've never used bio-based rejuvenators on a first-hand basis. According to Hohmann and Tabatabaee, there's no known limit on how many times the base material can go through the process of rejuvenation.
But in what types of mix design is it best used in?
“The proper rejuvenator can actually work quite well in both HMA or WMA,” Tabatabaee answered. “The incorporation of the rejuvenator will perform in the same manner, and the performance criteria for cracking and rutting resistance are going to be essentially the same as well.”
"Where there is an advantage," he continued. "is where rejuvenators can actually perform as a compaction aid. So, they allow you to actually produce a warm mix while you're rejuvenating, you have the potential possibility to kind of hit two birds with one stone in that case."
Rejuvenators can also be successfully used any many different types of mixes from base layers to surface layers, open graded mix to SMA.
When contractors are in the market to add these types of products to their production routines, there are a few things to consider, as well.
According to Hohmann, the incorporation of the rejuvenator is dependent on how much asphalt needs to be produced (ton/hour) and/or the mix designs approved for a set RAP usage. This is based on the customer’s needs and wants. But here are three common ways customers can incorporate a rejuvenator or additive:
Specify at the terminal to add in this material before loading the tank (Done at large mix plants that are limited on production space).
In-line blending of the rejuvenator in the asphalt before it hits the mix (Fairly common method but requires knowledge and constant monitoring of the mix and feed rates to verify).
Dose the rejuvenator into the storage tank upon refill (common when a mix facility is looking to use, but doesn’t have the money or influence to do option A or B).
How Much Rap?
One of the most revealing things from the research for this article was learning that, in the private sector, RAP usage has already pushed into much higher percentages. While there are cases of foreign markets utilizing 80-100% RAP mixes, there are markets here in the U.S. that are well above the curve too. States in the northeast, like New York, New Jersey, and even in Virginia, are running between 45-55% RAP mixes while maintaining a high quality criteria.
“The private asphalt industry has made great strides towards commercially implementing higher recycling and rejuvenation into pavements, I think the public sector and the governing regulations have lagged the industry in this case,” said Tabatabaee, “fortunately, the public sector can tap into the industry’s experience and knowledge as they’ve been doing this quite well for quite a while.”
What may come as a surprise to you, many states still don't track the data on RAP percentages, although that may be changing in the near future. With the implementation of Environmental Product Declarations as a matter of national policy, more specific data should become available on the makeup of mix designs as they vary sate-by-state. Perhaps, an analysis will reveal a potential future where even higher RAP usage will become the standard.
For more information visit https://asph.link/b5kz0x