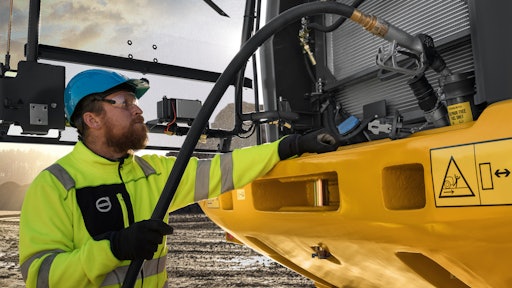
There is no doubt about it. Reliability is critical for wheel loader owners. And, over the years, traditional wheel loaders have proven to be highly reliable, day after day, year after year.
It is no surprise then that manufacturers like John Deere continue to offer a variety of traditional wheel loaders in its lineup. In fact, a majority of its wheel loaders are considered traditional. And they provide operators several performance features that, simply put, enable them to be highly capable for practically any application.
Yet, despite some customers’ hesitancy to explore hybrid style wheel loaders, as they’re afraid of replacing their longstanding, reliable machines, John Deere is certainly not afraid to think outside of the box, as it’s looking ahead to the future. And the future — without question — is wheel loaders powered by alternative fuels.
Alternative fuel-powered wheel loaders are definitely not “new” or unproven in the field either, as several have been in the marketplace for years. One such example is John Deere’s E-drive loaders, particularly its 644 X-Tier and 944 X-Tier, each of which is hybrid powered.
“If customers are on the fence between purchasing a traditionally powered wheel loader and a hybrid-powered wheel loader, they should know that John Deere’s E-drive loaders have accumulated more than 3 million field hours between them,” said Luke Gribble, solutions marketing manager, John Deere. “The 944 X-Tier is even backed by an 8-year, 20,000-hour electric drive component warranty that covers its electric drive components. An annual inspection, conducted by a certified dealer technician, is required though.”
Aside from its high aggregate of field hours and its electric drive component warranty, the 944 X-Tier — along with the 644 X-Tier, in fact — provides the same productivity benefits (if not better) that conventional drive train machines do. And each of the E-drive wheel loaders burn less fuel than traditional wheel loaders. Not to mention, E-drive wheel loaders have various features and modes that are offered exclusively by them, leading to fuel efficiency gains within a wide array of jobsite applications.
“One of these features is coast control, which enables each wheel loader’s dynamic braking to automatically slow it down whenever an operator’s foot is removed from the throttle pedal,” Gribble explained. “Due to this feature, fuel consumption will decline, while each wheel loader’s service brakes’ lifespans will increase.”
He added, “Three setting levels will allow operators to adjust the aggressiveness of machine deceleration while using electric brake resistors. When enabled, one pedal will control each wheel loader’s forward movement and dynamic braking.”
In addition, the 944 X-Tier has an exclusive feature that automatically limits torque to any of its wheels whenever slippage occurs: traction control. As a result, the potential for runaway wheel spin is not only eliminated, but tires’ lifespans will increase as well. Although operators can establish just how aggressive their wheel loader’s traction control is, the feature is actually automatic, so it doesn’t require any operator input whatsoever as the wheel loader is in operation.
“Both of these machine’s systems offer high performance, longevity and operation ease,” Gribble stressed. “The machines will also help jobsites lower their carbon emissions, as they’ll burn less fuel, use their tires for a longer time period and decrease the volume of fuels and oil they need, when compared to traditional wheel loaders.”
Furthermore, the 944 X-Tier features an electric drivetrain that has a John Deere 13.5L engine, a gearbox, two 3-phase Alternating Current (AC) permanent magnet generators and power electronics or inverters. Its electric drivetrain also has four 3-phase AC Switched Reluctance (SR) motors, along with four 2-stage reduction final drives and two brake resistors.
“The John Deere 13.5L engine — which operates at either a limited engine speed range or at constant speed, like a generator set — connects to a gearbox, which houses the hydraulic pumps,” Gribble said. “From there, the gearbox will then transfer engine power to the electric generators and hydraulic pumps.”
Afterwards, the electric generators will convert rotational energy from the engine into 3-phase alternating current (AC) electrical energy. The power electronics or inverter will deliver the electrical energy from the generators to the electric motors, based on operators’ demands. And then the electrical motors will convert the 3-phase AC back to rotational energy and torque into the final drives.
“Excess energy is passively consumed through two brake resistors that assist in maintaining reversal performance and engine over speed while coasting downhill,” Gribble added.
On the other hand, the 644 X-Tier is powered by a John Deere 6.8L engine, yet it’s also composed of a brushless electric generator and motor, as well as power electronics (via an inverter), an electric brake resistor and PowerShift transmission that Gribble stresses is “simplified”.
“Its brushless generator will convert rotational energy from the engine into 3-phase AC electrical energy, too,” he said. “The AC energy is supplied to the inverter, which delivers energy to the motor, based on operators’ demands.”
Its single brushless electric motor will convert AC energy back to rotational energy and torque as well, thereby replacing a torque converter’s typical job. Due to its simplified PowerShift transmission, shifting will remain smooth as operators have four operating speed ranges to choose from.
As operators decelerate, the 644 X-Tier’s electric motor can also be utilized as a generator, as it will recapture energy from its loader’s inertia and then recycle it back into the system. Whenever the wheel loader’s engine’s inverter actively controls its circuit, its brake resistor will passively consume any excess recycled energy.
While reflecting on the differences and similarities between hybrid-powered wheel loaders like the 944 X-Tier and the 644 X-Tier, Gribble believes a variety of aspects stand out. First, with regards to differences, traditional loaders always have major components like axles, an engine and a transmission. However, hybrid-powered wheel loaders can vary, as some of these components may be removed, simplified or substituted with electric components, according to Gribble.
“Some similarities definitely exist though, as each one of John Deere’s hybrid- and traditionally powered wheel loaders is still powered by diesel engines, and the 644 X-Tier still contains traditional axles,” he said. “Regardless of whether a wheel loader is hybrid- or traditionally powered, our dealer network will be able to help customers resolve any issues that may arise, as they prepare to utilize whichever machine is the most suitable for them and their needs.”
The Case 721G is powered by an FPT engine with patented selective catalytic reduction (SCR) emissions technology — there’s no diesel particulate filter (DPF) and no regeneration.CASE Construction Equipment
High Fuel Efficiency, Lower Emissions
With regards to Volvo Construction Equipment’s traditionally powered wheel loaders, Eric Yeomans, product manager, stresses that they’re very fuel-efficient and also have high traction control and gear shifting. In addition, they’re compatible with various technologies that support operators’ productivity, including Connected Maps, Load Assist and onboard weighing.
However, its electric-powered, hybrid prototype 20-ton wheel loader achieved a roughly 50% improvement in fuel efficiency during testing, leading to a 35% decline in emissions. Consequently, operators would be able to decrease their operating costs, while also increasing their productivity, as they’d spend less time on refueling.
“The operators who tested the wheel loader also noted its significantly quieter operation, ease of use and powerful hydraulics,” Yeomans said. “By using more environmentally friendly wheel loaders like our prototype, operators’ employers may also acquire clients that have sustainability requirements.”
As Yeomans compares Volvo Construction Equipment’s traditionally powered wheel loaders with its electric-powered, hybrid prototype 20-ton wheel loader, he believes they provide practically the same amount of power and the same level of performance. They also both have an attachment or a bucket, front and rear frames, loader arms, rims, tires and cabs that will offer operators safe environments. Yet, some key differences exist too, aside from fuel efficiency.
“Our prototype hybrid wheel loader’s driveline consists of a battery energy storage system, electrically driven hydraulics and electric drive motors, which are mounted at the wheels,” he said. “The prototype, which has 98% new parts and a fundamentally new machine design, can do the work of a wheel loader that’s one size larger.”
First Green Industries' Elise 900 electric-powered wheel loader has lower noises and vibrations than traditionally powered wheel loaders.First Green Industries
Less Noise, Less Vibrations, More Comfort
Meanwhile, Joe Schinasi, vice president, sales, First Green Industries, has noticed a variety of benefits, concerning the usage of traditionally powered wheel loaders. First, their performance capabilities and limitations are well known. And they can be refueled quickly on operators’ jobsites.
“There is an expansive universe of service documentation and experienced service technicians, as many professionals know how to diagnose problems and fix diesel equipment,” he said. “Furthermore, if owners purchase a new traditionally powered wheel loader, their out-of-pocket expenses will be lower than if they had purchased new electric-powered wheel loaders instead.”
Of course, electric-powered wheel loaders are less expensive throughout their lifespans than traditionally powered wheel loaders are, as they require less maintenance, particularly since they have fewer moving parts and fluids than diesel-powered wheel loaders. Additionally, they have lower noises and vibrations, leading to higher operator comfort.
“And since they utilize electric power, any risk of contamination to the environment, in which fuel is typically stored, is alleviated,” Schinasi stated. “They can also be used in confined interior spaces, as they promote cleaner air, too.”
Another key difference? Electric-powered wheel loaders may not always have enough power to be used for operators’ entire work shifts. And, since they aren’t typically recharged quickly, they may be “offline” until they’re recharged.
“These concerns can be eased by having multiple batteries for hot swapping, which First Green Industries offers,” he added. “And operators can utilize fast charging systems — offerings that our company will have in its pipeline.”
The 644 X-Tier wheel loader is powered by a John Deere 6.8L engine and composed of a brushless electric generator and motor.John Deere
High Performance, Regardless of Your Preference
Brady Lewis, product manager, CASE Construction Equipment, agrees with Schinasi, adding that “wheel loaders with traditional combustion engines are practical, well-established and familiar to fleet managers and operators alike.” They’re also highly powerful and they’ve been proven “to get the job done” over and over again. In addition, they can operate practically anywhere in which operators can acquire fuel.
But electric-powered wheel loaders have a variety of benefits too, from the elimination of all costs associated with diesel engines, to their ability to be utilized indoors, to the aforementioned impact on jobsites’ emissions. And, as Schinasi mentioned, their quiet performances shouldn’t be overlooked, as the sounds of an electric motor and its hydraulic systems are considerably less than a diesel engine’s, enabling operators to talk to their co-workers more easily on their jobsites.
“Not every job will be right for electrified wheel loaders, as there are sites in which access to electricity, production levels and size obviously make machines with combustion engines more practical,” Lewis said. “But there are also jobs in which electrified wheel loaders excel, from big box stores that require wheel loaders to be used inside, to large, existing factories that are being renovated, to supply yards that have access to regular power and need to utilize wheel loaders at various times throughout the day.”
Whether operators choose to use a traditionally powered wheel loader or an electric-powered wheel loader, CASE Construction Equipment is focused on ensuring each product offers them high performance, along with a variety of capacities.
“Everything is relative to scale, but operators should experience the same capabilities and feel, regardless of the wheel loader they utilize,” Lewis emphasized. “In some cases, operators will need some time to become accustomed to not hearing a diesel engine running, but they’re generally satisfied with the equivalent performances of electric-powered wheel loaders, in comparison to diesel-powered wheel loaders of similar sizes.”
Volvo Construction Equipment’s electric-powered, hybrid prototype 20-ton wheel loader achieved a 50% improvement in fuel efficiency during testing, leading to a 35% reduction in emissions.Volvo Construction Equipment
Prepare for the Future
As operators choose between a traditionally powered wheel loader and an alternative fuels- or electric-powered wheel loader, their decisions are based on the requirements they have for their specific job tasks, according to Schinasi. However, with that being said, he does believe the future of wheel loaders will be tied to alternative fuels and electricity.
“The benefits of electric-powered wheel loaders are substantial,” he stressed. “And, without a doubt, a higher percentage of wheel loaders will progressively be powered by clean energy power.”
Lewis believes that, as with practically every buying choice in the construction industry, the decision between purchasing a traditionally powered wheel loader or an electric-powered wheel loader comes down to operators knowing their specific applications.
“If operators are running wheel loaders in a supply yard where they aren’t running at production levels all day, electrified wheel loaders may be the best option,” he said. “Likewise, if operators are conducting indoor renovation and reclamation work, electrified wheel loaders will be the most suitable.”
He continued, “But, if operators are working in outdoor production environments for multiple shifts, they should utilize a wheel loader with a traditional combustion engine. And if a jobsite has primary power that hasn’t been run to it yet and a wheel loader has to stay on site indefinitely, traditional power will be the best bet.”
In the meantime, if operators need wheel loaders for heavy V-pattern loading style applications, they will prefer the fuel efficiency enhancements offered by hybrid-powered wheel loaders, according to Gribble.
“When operators lay off their wheel loader’s accelerator pedal, change its direction or drive it downhill, inertia and gravity will continue to drive it,” he said. “When this happens, the wheel loader’s electric motors are mechanically driven by its wheels through its driveline, as they temporarily become generators, adding supplemental energy to its electric drive system.”
This energy is then distributed to the wheel loader’s power electronics, which can, in turn, use the energy to drive its generators to offer assistance, with regards to its hydraulic pumps’ drivability. Consequently, the load on its engine will decline, thereby enabling its engine controller to transmit less fuel to its engine, resulting in highly evident fuel gains.
“As more and more operators realize the benefits that hybrid-powered wheel loaders provide, including increased production, less fuel burn, and lower owning and operating costs, they will likely continue to become more and more popular in the years to come,” he added.
In preparation for the future, Yeomans believes hybrid-powered and traditionally powered wheel loaders will continue to have roles on their respective jobsites — as will other alternatively powered wheel loaders like fully electric models.
“At Volvo Construction Equipment, we believe there is no single solution when it comes to sustainable power,” he said. “That’s why we’re working with technologies such as battery-electric, hybrid and hydrogen fuel cells, along with alternative fuels like hydrogen combustion, on various products.”
Regarding its internal combustion wheel loaders, the company is striving to ensure they’re more efficient and environmentally friendly.
“For example, we recently upgraded our L350H wheel loader, leading to 10% faster working cycles and up to 15% greater fuel efficiency,” Yeomans stated. “And we’ve introduced two compact wheel loaders that are fully electric, the L20 Electric and L25 Electric. They have zero emissions, a significant reduction in noise levels and similar performances, when compared to their diesel counterparts.”
The bottom line? According to Lewis, “electrification is here to stay.”
“As electric technology improves every day, operators are going to see it expand more into larger machines and more diverse applications,” he added. “There will always be a demand for traditionally powered wheel loaders, due to the applications they’re most ideal for. But, without a shadow of a doubt, electrification is the future — and electrified models and capabilities will only continue to expand.”