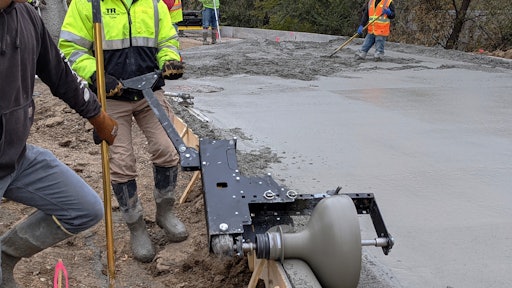
Traditionally, curb and gutter work has been performed with large machines or through a back-breaking manual process that requires a high degree of skill that can be difficult to find.
But what jobs are best suited for this equipment? What factors affect how it is used? And how should equipment options be considered when estimating curb and gutter work? We connected with Seth Ulmer of Curb Roller Manufacturing, to help explore some of the most common questions facing contractors when considering curb and gutter jobs. Seth Ulmer, Curb Roller Manufacturing sales managerCurb Roller Manufacturing
What’s the key to a successful curb and gutter project?
Whether pouring new curb and gutter or repairing existing concrete, the key is to plan ahead. It’s important to partner with a concrete supplier who understands the scope of the project to provide the correct concrete mix at the right time.
Additionally, contractors should carefully select the proper equipment and ensure they have a crew that has the skill to operate the machinery and successfully shape and finish the concrete. While some contractors can rely on crews with years of experience and a high skill level, less experienced operators can also perform quality work if they have equipment that is easy to learn and designed to produce consistent results that meet the requirements of the job.
Is there a water/cement ratio to aim for in curb and gutter work? How does slump fit into the process?
Slump is a critical aspect of shaping concrete, and curb and gutter work is no exception. If the slump is not correct, the concrete won’t hold the correct shape, leading to delays and additional costs. Most curbing machines work best with a curb mix of concrete that has a higher sand-to-rock ratio, but the ideal slump is determined based on the equipment selected for the job. Large slipform machines often require a 1-2-inch slump. Smaller walk-behind curbing machines typically use a 3-4-inch slump, leading to a larger window of time available to shape and finish the concrete.
How important is speed when shaping curb and gutter?
A key phrase in curb and gutter work is, “steady pace wins the race.” Operators need to find a proper, consistent speed to produce a uniform shape, whether they are working with a large slipform paver or a smaller walk-behind machine. For walk-behind curbing machines, the pace is generally determined by the slump, with a higher slump requiring slower speeds and a lower slump allowing a faster pace.
What would be your advice in estimating curb and gutter jobs?
It’s important to know all the details when estimating curb and gutter jobs, including the overall width and depth of the concrete that will be poured, specifications for the concrete mix and any tear-out and removal requirements. Additionally, contractors should understand how much of the jobsite will be released while the work is completed. Crowded jobsites can limit the ability to use a large machine efficiently, so understanding this factor may influence what equipment a contractor should account for in their estimate.
Walk-behind curbing machines are ideal for small- to mid-size projects. They are also able to tackle projects that have a large amount of radius work, small cut-ins or hard-to-reach corners more efficiently than larger machines. These walk-behind machines also really shine in patch and repair jobs.Curb Roller Manufacturing
What scenarios would be best for each type of curbing machine?
Walk-behind curbing machines are ideal for small- to mid-size projects. They are also able to tackle projects that have a large amount of radius work, small cut-ins or hard-to-reach corners more efficiently than larger machines. These walk-behind machines also really shine in patch and repair jobs.
Slipform pavers are designed for large projects. They are capable of shaping thousands of feet of curb and gutter a day. Often, contractors find that a combination of equipment is ideal. They can use a slipform machine to efficiently shape the majority of concrete in large jobs, passing over inside corners and tight radiuses, then follow with a portable walk-behind curbing machine to finish these areas.
Does interest and investment in residential concrete lead to increased curbing jobs or are these projects more related to the infrastructure funding?
Most residential projects are privately funded and based on demand. Much of this pent-up demand for housing seems to have come from a pause in building during the COVID-19 pandemic, with people now looking to relocate or invest in real estate for the first time. This has led to an increased need for contractors that specialize in curb and gutter. While this is often outside a contractor’s scope of work, intuitive and operator-friendly equipment can help contractors self-perform curb and gutter work. Down the road, we could see this ability become even more critical if infrastructure funding leads to additional repair work in residential areas.
There seems to be a big push toward batteries in concrete tools. Is battery power the future of concrete power tools and machines?
The construction market is seeing a strong demand for and investment in battery-powered machines that reduce emissions. Battery power has many benefits, including unparalleled portability and efficiency that comes with the elimination of cords, hoses, and fumes. Batteries are now powering a wide variety of machines on jobsites, and there is growing trust in the ability to rely on battery-powered equipment. This is allowing contractors to consider new ways to approach project demands. There is still a place for other power sources on a site based on project needs, and we are excited to be leaders in offering options that help contractors select the best equipment for the job.